Oxidized Bitumen 90/15
Oxidized Bitumen 90/15

At the Oxidized bitumen 90/15 production reactor, during the air acting, the mixture of the two Vacuum Bottom (VB) and Vacuum Silas (VS) feedstock is put under a special degree of pressure and temperature between 200-300˚C of which the hydrogen atoms content in bitumen molecular oxidize to the oxygen of the air, and obtains with higher hydrocarbons polymerization reaction that has lower penetration and higher softening points than the primary pure bitumen. This kind of bitumen 90/15 has the softening point of 90 and permeability of 15.
Oxidized bitumen is a specially formulated plastic for construction. Oxidized bitumen characterized by being a product of great thermal amplitude. Oxidized bitumen has the flexibility to cold, has no sag at high temperatures, and has good adhesion. It can be applied to any kind of work. Oxidized bitumen is available in different grades. Bitumen 90/15 is produced by either Continuous or Staggered Blowing Process. Heated Penetration Grade Bitumen under controlled environment is blown with air which controls the Oil Content in the Bitumen while it oxidized. The different grades for suited applications produced are designated by two numbers to indicate the mid-points of their softening point and penetration ranges.
As said before, Bitumen 90/15 is based on petroleum bitumen which is made by blowing bitumen 60/70 by very hot air. In addition, the numbers relate to the midpoint of the material’s softening point and penetration respectively. The softening point value measured by the Ring and Ball method as determined by ASTM D36. Also, the penetration value is in 1/10 mm as determined by IP49 or ASTM- D5.
Oxidized Bitumen 90/15 Applications
Oxidized bitumen 90/15 uses in the chemical, fuel, paints, lacquers, varnishes, paper-pulp-board, textile processing, road construction, pavement, crack seal and repairmen, civil works, roofing, construction industries; sealing and insulating buildings, adhesive, construction materials additive, dust-binding, insulating and impregnating agent, make rubber and plastic products. The Oxidized asphalt 90/15 products are for paving. also used in asphalt-based paints for corrosion protection of metals, inlining public works structures, adhesives in electrical laminates, a base for synthetic turf; typical uses for oxidized bitumen 90/15 used also for water-proof application and corrosion resistance for pipe coating, Portland cement pavement, hydraulic applications, paint manufacturing, caulking, mastics, and damp proofing. Oxidized bitumen 90/15 is using the insulation and isolation bitumen membrane sheet. Also, Car undercoating Automobile industry is especially required for Blown Asphalt. Vehicle undercoating material is based on Bitumen. Bitumen provides excellent waterproof, dustproof, and noise proof for automobile undercoating.
Oxidized bitumen 90/15 should be heated double temperature against the softening point to be able to have flow and viscosity. To use oxidized bitumen 90/15, surfaces must be dry, clean, and free of loose particles, formwork, curing products, irregularities, slurry, etc.
- Oxidized bitumen is used as a sealing of expansion joints.
- Oxidized bitumen is used as a repair of joints or cracks.
- Oxidized bitumen is used as a fixation of parquet floors.
- Oxidized bitumen is used as an adhesive to be used in thermal insulation.
- Oxidized bitumen is used as a repair of unexposed cracks.
- Oxidized bitumen is used as bonding of wet briquettes
- Oxidized bitumen is used in various industries like roofing, isolation, insulation flooring, mastics, pipe coatings, electrical applications.
Technical Advantages of Oxidized Asphalt 90/15
- Durability
- Flexibility
- Water-Resistant
- Chemical Stability
Compared to paving grade bitumen:
- Reduced temperature susceptibility
- Exhibits a more ‘solid’ nature at ambient temperatures
- High penetration index
Recommendations for Handling / Storage
The heating of packaged bitumen is a critical phase in most of the final uses. Typically, the packaged material is heated and melted in boilers out on site.
However, control at the heating phase is very important in terms of health and safety as well as in maintaining the quality of the product.
A note must be taken of the maximum safe handling temperature of 230 C and this should not be abused. Bitumen is a poor conductor of heat, consequently, control of the heating phase is of paramount importance.
The Oxidized Asphalt material should be broken up prior to placement in the boiler. This exposes a larger surface area to the heat and encourages a more even heating regime. Without the larger exposed surface area, aggressive heating at the base and sides of the boiler may well result in localized overheating, altering the characteristics of the modified bitumen, and potentially causing thermal cracking of the bitumen, creating the release of low lash vapors. The flashpoint of the oxidized bitumen then becomes irrelevant; as these low flash vapors determine the fire risk.
Melted bitumen should not be left in the boiler and reheated from cold, as there is then a high potential for localized overheating around the heating area (lack of convection means poor heat transfer) and potential development of a pressurized pocket of low flash vapors.
Be aware of the placement of any temperature monitoring or control devices. As a result of the poor thermal conductivity of the bitumen, a thermometer in the bitumen some distance from the heat source could read significantly different (even hundreds of degrees) from the true temperature of the bitumen near the heat source.
For Health and Safety information, please make reference to the relevant MSDS.
Health & Safety
Workers should wear protective masks, gloves, and goggles during application. The asphalt can be removed from equipment and tools with kerosene or gasoline. Care should be taken when heating Oxidized Asphalt 90/15 to avoid overheating.
Packing of Oxidized Asphalt 90/15
Oxidized Asphalt 90/15 in various packing, including bitumen 90/15 is available in 20 & 50 kg Kraft Paper Bags / Poly Amide Bags, 25 kg Carton box, and 150, 180, 200kg Steel Drums. In addition, oxidized bitumen packing also palletize, 40 bags can stack on the pallet. 20 pallets can load to the 20ft container.
Oxidized Asphalt 90/15 Specifications
Bitumen 90/15 | Test method | Unit | Specification |
Specific gravity @25/25 C | ASTM D70 | (Kg/m3) | 1.05 approx. |
Penetration @ 25°c | ASTM D5 | mm/10 | 10/20 |
Softening point °c | ASTM D36 | °C | 85/95 |
Ductility @25 °c | ASTM D113 | Cm | 1.5min |
Loss on heating(wt) % | ASTM D6 | Wt. % | 0.2 max |
Flashpoint c | ASTM D92 | °C | 250 min |
Solubility is CS2(wt) % | ASTM D4 | Wt. % | 99.5 max |
Spot test | A.A.S.H.O.T102 | — | Negative |
Oxidized Bitumen 90/40
Oxidized Bitumen 90/40 Description

Oxidized bitumen 90/40 (in other words, Blown asphalt 90/40, blown bitumen 90/40) is Semi Solid grade of pure petroleum bitumen manufactured by air-blowing through an asphalt flux. Special physical properties of its grade can be used in different applications in the construction business. blown asphalt 90/40 is based on petroleum bitumen which is made by blowing asphalt 60/70 by very hot air. The numbers relate to the midpoint of the material’s softening point and penetration respectively. The softening point value is the degrees Centigrade measured by the Ring and Ball method as determined by ASTM D36. The penetration value is in 1/10 mm as determined by IP49 or ASTM D5.
Oxidized Asphalt is a solid or semi-black solid material and gradually liquid when heated, oxidized asphalt is the predominant content bitumen, asphalt, molten (oils), and aromatic resins. The oxidized asphalt or blown asphalt is producing in different softening point and penetration.
Oxidized Bitumen 90/40 Applications
Blown Asphalt 90/40 is a semi-solid oxidized grade of pure petroleum bitumen categorized in polycyclic aromatic hydrocarbons that are normally used for different purposes in the construction business.
Blown Asphalt 90/40 is widely used as an anti-slip layer compound in the piling industry, for the manufacture of roofing felts, the roofing and waterproofing industries, for sound dampening felts and undercarriage sealant in the automotive industry, electric cable joint protection, joint filling compound, carpet-backing, corrosion protection, acoustic panels, chemical, fuel, Manufacture of paints, sealant compound, and many others. Also used in sealing saw cuts and joints where expected movements are minimum. It is also used in the manufacturing of bituminous marine mastic for the oil & gas pipeline joints. Further, Blown Asphalt is used in the manufacture of bituminous marine mastic, which is required for the oil and gas pipeline joints.
Blown Asphalt has several usages in the industry
Oil and Gas industries:
- Coating materials for pipelines and pipe joints of Oil Also Gas Pipelines.
Electrical industries:
- The sealant of wire coating
Waterproofing industries:
- Building roofing felts in factories and first materials components who are producing waterproofing roofing felt sheets
Bitumen and Asphalt:
- Road paving, Asphalt, construction.
- Making Sound insulation layers.
- Car tires and lining.
Technical Advantages of Oxidized Bitumen 90/40
- Durability
- Flexibility
- Water Resistant
- Chemical Stability
Compared to paving grade bitumen:
- Reduced temperature susceptibility
- Exhibits a more ‘solid’ nature at ambient temperatures
- High penetration index
Recommendations for Handling / Storage
The heating of packaged bitumen is a critical phase in most of the final uses. Typically, the packaged material is heated and melted in boilers out on site.
However, control at the heating phase is very important in terms of health and safety as well as in maintaining the quality of the product.
A note must be taken of the maximum safe handling temperature of 230 C and this should not be abused. Bitumen is a poor conductor of heat, consequently, control of the heating phase is of paramount importance.
The Oxidized Bitumen material should be broken up prior to placement in the boiler. This exposes a larger surface area to the heat and encourages a more even heating regime. Without the larger exposed surface area, aggressive heating at the base and sides of the boiler may well result in localized overheating, altering the characteristics of the RAHA modified bitumen, and potentially causing thermal cracking of the bitumen, creating the release of low lash vapors. The flashpoint of the oxidized bitumen then becomes irrelevant; as these low flash vapors determine the fire risk.
Melted bitumen should not be left in the boiler and reheated from cold, as there is then a high potential for localized overheating around the heating area (lack of convection means poor heat transfer) and potential development of a pressurized pocket of low flash vapors.
Be aware of the placement of any temperature monitoring or control devices. As a result of the poor thermal conductivity of the bitumen, a thermometer in the bitumen some distance from the heat source could read significantly different (even hundreds of degrees) from the true temperature of the bitumen near the heat source.
For Health and Safety information, please make reference to the relevant MSDS.
Health & Safety
Workers should wear protective masks, gloves, and goggles during application. The asphalt can be removed from equipment and tools with kerosene or gasoline. Care should be taken when heating Blown Asphalt 90/40 to avoid overheating.
Packing of Oxidized Bitumen 90/40
Blown Asphalt 90/40 in various packing, including bitumen 90/40 is available in 20 & 50 kg Kraft Paper Bags / Poly Amide Bags, 25 kg Carton box, and 150, 180, 200kg Steel Drums. In addition, oxidized bitumen packing also palletize, 40 bags can stack on the pallet. 20 pallets can load to the 20ft container.
Technical Data Sheet of Blown Asphalt 90/40
Bitumen 90/40 | Test method | Unit | Specification |
Specific gravity @25/25 C | ASTM D70 | (Kg/m3) | 1.05 approx. |
Penetration @ 25°c | ASTM D5 | mm/10 | 35/45 |
Softening point °c | ASTM D36 | °C | 85/95 |
Ductility @25 °c | ASTM D113 | Cm | 5.5min |
Loss on heating(wt) % | ASTM D6 | Wt. % | 0.2 max |
Flashpoint c | ASTM D92 | °C | 250 min |
Solubility is CS2(wt) % | ASTM D4 | Wt. % | 99.5 max |
Spot test | A.A.S.H.O.T102 | — | Negative |
Oxidized Bitumen 95/25
Oxidized Bitumen 95/25 Description

Oxidized Bitumen 95/25 is Semi Solid grade of pure petroleum bitumen manufactured by air-blowing through an asphalt flux. Special physical properties of its grade can be used in different applications in the construction business. Oxidized bitumen95/25 is based on petroleum bitumen which is made by oxidized bitumen 60/70 by very hot air. The numbers relate to the midpoint of the material’s softening point and penetration respectively. The softening point value is the degrees Centigrade measured by the Ring and Ball method as determined by ASTM D36. The penetration value is in 1/10 mm as determined by IP49 or ASTM- D5.
oxidized Bitumen is industrial bitumen which is dark, petroleum residue modified by the oxidation process. Oxidized Bitumen is produced by passing air through bitumen under controlled temperature conditions. Its consistency ranges from highly viscous to solid. Blown bitumen grade has technical advantages such as durability, flexibility, water-resistant and chemical stability. There is a different grade of blown bitumen.
Oxidized Bitumen 95/25 Applications
Oxidized Bitumen 95/25 is widely used as an anti-slip layer compound in the piling industry, for the manufacture of roofing felts, the roofing and waterproofing industries, for sound dampening felts and undercarriage sealant in the automotive industry, electric cable joint protection, joint filling compound, carpet-backing, corrosion protection, acoustic panels, chemical, fuel, Manufacture of paints, sealant compound, and many others. Also used in sealing saw cuts and joints where expected movements are minimum. It is also used in the manufacturing of bituminous marine mastic for the oil & gas pipeline joints. Further, Oxidized Bitumen is used in the manufacture of bituminous marine mastic, which is required for the oil and gas pipeline joints.
- Oxidized bitumen is used as a sealing of expansion joints.
- Oxidized bitumen is used as a repair of joints or cracks.
- Oxidized bitumen is used as a fixation of parquet floors.
- Oxidized bitumen is used as an adhesive to be used in thermal insulation.
- Oxidized bitumen is used as a repair of unexposed cracks.
- Oxidized bitumen is used as bonding of wet briquettes
- Oxidized bitumen is used in various industries like roofing, isolation, insulation flooring, mastics, pipe coatings, electrical applications.
Technical Advantages of Oxidized Bitumen 95/25
- Durability
- Flexibility
- Water-Resistant
- Chemical Stability
Compared to paving grade bitumen:
- Reduced temperature susceptibility
- Exhibits a more ‘solid’ nature at ambient temperatures
- High penetration index
Storage/handling of oxidized bitumen 95/25
bitumen 95/25 has 10 years validity with multi-time heating and cooling, please refer to MSDS.
Packing of Blown Asphalt 95/25
Various pickings are available for customer’s purpose and conveniences. oxidized bitumen 95/25 in various packing including Kraft bag, meltable plastic bag, drum, and bulk bitumen 95/25 from penetration grade bitumen, which is blown by hot air in a controlled process until the desired specification is reached. oxidized bitumen 95/25 can be supplied in any grade and are designated by two numbers to indicate the softening point and penetration ranges. The bitumen grade 95/25 means the softening point is 95°c and penetration is 15 desi millimeter is produced in compliance and conformity with ASTM standard and meets the following specification.
Specification of Blown Asphalt 95/25
Analysis of bitumen 95/25
Bitumen 95/25 | Test method | Unit | Specification |
Specific gravity @25/25 C | ASTM D70 | (Kg/m3) | 1.05 approx. |
Penetration @ 25°c | ASTM D5 | mm/10 | 20/30 |
Softening point °c | ASTM D36 | °C | 90/100 |
Loss on heating(wt) % | ASTM D6 | Wt. % | 0.2 max |
Flashpoint °c | ASTM D92 | °C | 250 min |
Solubility is CS2(wt) % | ASTM D4 | Wt. % | 99.5 max |
Spot test | A.A.S.H.O.T102 | — | Negative |
Oxidized Bitumen 115/15
Oxidized Bitumen 115/15 Description
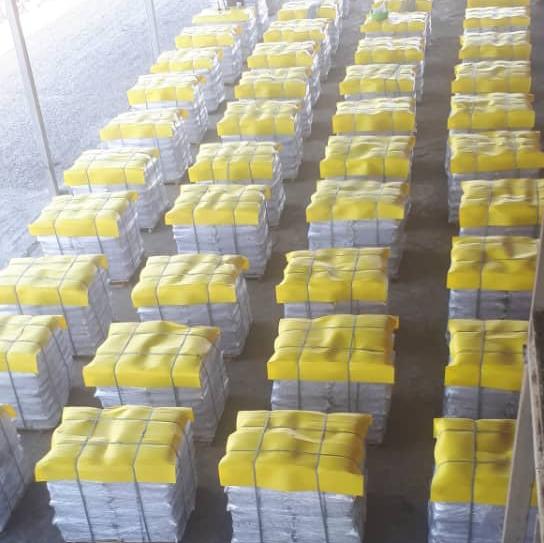
Oxidized bitumen 115/15 is based on petroleum bitumen which is made by blowing bitumen 60/70 by hot air. The most oxidized bitumen usable grade is bitumen 115/15 and 70% of our capacity is dedicated to this grade. bitumen 115/15 is a semi-solid oxidized grade of pure petroleum bitumen categorized in polycyclic aromatic hydrocarbons and oxidized bitumen normally used for different purposes in the construction business. Bitumen 115/115 has a high softening point, high flash point and it is highly stable during melting.
Oxidized Bitumen 115/15 Applications
Blown Asphalt 115/15 is widely used as an anti-slip layer compound in the piling industry, for the manufacture of roofing felts, for sound dampening felts and under carriage sealant in the automobile industry, electric cable joint protection, joint filling compound, sealant compound and many others.
Bitumen 115/15 is widely used as an anti-slip layer compound in the piling industry, for the manufacture of roofing felts, for sound dampening felts and undercarriage sealant in the automobile industry, electric cable joint protection, joint filling compound, sealant compound, and many others.
It’s using as raw material for bitumen coat, roofing, insulation also in Isolation bitumen membrane sheet. Also, Bitumen 115/15 uses in chemical, fuel, paints, lacquers, varnishes, paper-pulp-board, textile processing. In road construction, pavement, crack seal and repairmen, civil works, roofing also construction. Besides, it uses for sealing and insulating buildings, adhesive, construction materials additive, dust-binding, coating. With the wide range uses in the insulating and impregnating agent, make rubber and plastic products.
Bitumen 115/15 products are for paving, roofing. Also used in asphalt-based paints for corrosion protection of metals, inlining public works structures, adhesives in electrical laminates, a base for synthetic turf. Typical uses for Bitumen 115/15 also include roofing, pipe coating, Portland cement pavement, hydraulic applications, paint manufacturing.
Besides, it uses in asphalt-based paints for corrosion protection of metals. Also in lining public works structures, adhesives, electrical laminates, a base for synthetic turf. Furthermore, typical uses for Blown Asphalt 115/15 include roofing, pipe coating, Portland cement pavement, hydraulic applications, paint manufacturing.
Technical Advantages of Blown Asphalt 115/15
- Durability
- Flexibility
- Water-Resistant
- Chemical Stability
Compared to paving grade bitumen:
- Reduced temperature susceptibility
- Exhibits a more ‘solid’ nature at ambient temperatures
- High penetration index
Blown Asphalt 115/15 Storage/handling
Oxidized bitumen 115/15 has 10 years of validity with multi-time heating and cooling, please refer to MSDS. It is better to keep the bitumen 115/15 under shelter and out of the rain, sun. By mopping or by the pour and roll method. Should be heated to a temperature between 180 to 200.
Blown Asphalt 115/15 Packing
The bitumen 115/15 is available in bulk, drum, meltable, and craft bag. This bitumen 115/15 is generally shipped as a solid and heated in a kettle at the worksite.
Blown Asphalt 115/15 CHARACTERISTICS
CHARACTERISTIC | Test method | Unit | Specification |
Specific gravity @25/25 C | ASTM D70 | (Kg/m3) | 1.05 approx. |
Penetration @ 25°c | ASTM D5 | mm/10 | 10/20 |
Softening point °c | ASTM D36 | °C | 110/120 |
Ductility @25 °c | ASTM D113 | Cm | 1.5min |
Loss on heating(wt) % | ASTM D6 | Wt. % | 0.2 max |
Flashpoint c | ASTM D92 | °C | 250 min |
Solubility is CS2(wt) % | ASTM D4 | Wt. % | 99.5 max |
Spot test | A.A.S.H.O.T102 | — | Negative |
Oxidized Bitumen 105/35
Oxidized Bitumen 105/35 Description

Oxidized bitumen 105/35 is a good grade of oxidized asphalt to use as bonding compounds as hot melt adhesive at an application rate of approximately 1 Kg/m3 to bond the preformed sheets together and to structure which is made by Oxidized bitumen 60/70 by hot air. Blown bitumen 105/35 is a semi-solid oxidized grade of pure petroleum bitumen manufactured by air-blowing through an asphalt flux. Special physical properties of its grade can be used in different applications in the construction business.
Oxidized Bitumen 105/35 Applications
Oxidized bitumen 105/35 uses in the chemical, fuel, lacquers, varnishes, paper-pulp-board, textile processing, road construction, pavement, paint, crack seal and repairmen, civil works, roofing, construction business; sealing and insulating buildings, adhesive, construction materials additive, dust-binding, insulating and impregnating agent, make rubber and plastic products. The bitumen 105/35 products are for paving. also used in asphalt-based paints for corrosion protection of metals, inlining public works structures, adhesives in electrical laminates, the base for synthetic turf; typical uses for bitumen 105/35 used also for water-proof application and corrosion resistance for pipe coating, Portland cement pavement, hydraulic applications, paint manufacturing. Blown bitumen 105/35 is using the insulation and isolation bitumen membrane sheet. The car undercoating Automobile industry is especially required for blown bitumen. Vehicle undercoating material is based on Bitumen. Bitumen provides excellent waterproof, dustproof, and noise proof for automobile undercoating.
Blown Asphalt 105/35 should be heated double temperature against the softening point to be able to have flow and viscosity. To use blown bitumen 105/35, surfaces must be dry, clean, and free of loose particles, formwork, curing products, irregularities, slurry, etc.
Storage/handling of blown bitumen 105/35
bitumen 105/35 has 10 years validity with multi-time heating and cooling, please refer to MSDS.
Packing of blown bitumen 105/35
Different packing is available for the customer’s purpose and convenience. bitumen 105/35 in different packing including Kraft bag, meltable plastic bag, drum, and bulk. Blown asphalt 105/35 from penetration grade bitumen, which is blown by hot air in a controlled process until the desired specification is reached. bitumen 105/35 can be supplied in any grade and are designated by two numbers to show the softening point and penetration ranges. The bitumen grade 105/35 means the softening point is 105 and penetration is 35 desi millimeters is produced in compliance and conformity with ASTM standard and meets the following specification.
Specification of blown bitumen 105/35
Analysis bitumen 105/35
Bitumen 105/35 | Test method | Unit | Specification |
Specific gravity @25/25 C | ASTM D70 | (Kg/m3) | 1.05 approx. |
Penetration @ 25°c | ASTM D5 | mm/10 | 30/40 |
Softening point °c | ASTM D36 | °C | 100/110 |
Loss on heating(wt) % | ASTM D6 | Wt. % | 0.2 max |
Flashpoint c | ASTM D92 | °C | 250 min |
Solubility is CS2(wt) % | ASTM D4 | Wt. % | 99.5 max |
Specific gravity @25/25 C | ASTM D70 | (Kg/m3) | 1.05 approx. |
Oxidized Bitumen 105/15
Oxidized Bitumen 105/15 Description

Oxidized asphalt 105/15 (another word, blown asphalt 105/15, oxidized bitumen 105/15) is Semi Solid grade of pure petroleum bitumen manufactured by air-blowing through an asphalt flux. Special physical properties of its grade can be used in different applications in the construction business. Oxidized asphalt 105/15 is based on petroleum bitumen which is made by blowing bitumen 60/70 by very hot air. The numbers relate to the midpoint of the material’s softening point and penetration respectively. The softening point value is the degrees Centigrade measured by the Ring and Ball method as determined by ASTM D36. The penetration value is in 1/10 mm as determined by IP49 or ASTM- D5.
Oxidized Bitumen 105/15 Applications
Oxidized asphalt 105/15 uses in the chemical, fuel, paints, lacquers, varnishes, paper-pulp-board, textile processing, road construction, pavement, crack seal and repairmen, civil works, roofing, construction industries; sealing and insulating buildings, adhesive, construction materials additive, dust-binding, insulating and impregnating agent, make rubber and plastic products. The oxidized asphalt 105/15 products are for paving. also used in asphalt-based paints for corrosion protection of metals, inlining public works structures, adhesives in electrical laminates, a base for synthetic turf; typical uses for asphalt 105/15 used also for water-proof application and corrosion resistance for pipe coating, Portland cement pavement, hydraulic applications, paint manufacturing, caulking, mastics, and damp proofing. Asphalt 105/15 is using the insulation and isolation bitumen membrane sheet. The car undercoating Automobile industry is especially required for Blown Asphalt. Vehicle undercoating material is based on Bitumen. Bitumen provides excellent waterproof, dustproof, and noise proof for automobile undercoating. The oxidized asphalt 105/15 should be heated double temperature against the softening point to support have flow and viscosity. To use asphalt 105/15, surfaces must be dry, clean and after loose particles, formwork, curing products, irregularities, slurry, etc.
Technical Advantages of Blown Bitumen 105/15
- Durability
- Flexibility
- Water-Resistant
- Chemical Stability
Storage and Handling
The heating of packaged bitumen is a critical phase in most of the final uses. Typically, the packaged material is heated and melted in boilers out on site.
However, control at the heating phase is very important in terms of health and safety as well as in maintaining the quality of the product.
The note must be taken of the maximum safe handling temperature of 230 C and this should not be abused. Bitumen is a poor conductor of heat, consequently, control of the heating phase is of paramount importance.
The Blown Bitumen material should be broken up before placement in the boiler. This exposes a larger surface area to the heat and encourages a more even heating regime. Without the larger exposed surface area, aggressive heating at the base and sides of the boiler may well result in localized overheating, altering the characteristics of the modified bitumen and potentially causing thermal cracking of the bitumen, creating the release of low lash vapors. The flashpoint of the oxidized bitumen then becomes irrelevant; as these low flash vapors determine the fire risk.
Melted bitumen should not be left in the boiler and reheated from cold, as there is then a high potential for localized overheating around the heating area (lack of convection means poor heat transfer) and potential development of a pressurized pocket of low flash vapors.
Be aware of the placement of any temperature monitoring or control devices. As a result of the poor thermal conductivity of the bitumen, a thermometer in the bitumen some distance from the heat source could read significantly different (even hundreds of degrees) from the true temperature of the bitumen near the heat source.
For Health and Safety information, please make reference to the relevant MSDS.
Health & Safety
Workers should wear protective masks, gloves, and goggles during application. The asphalt can be removed from equipment and tools with kerosene or gasoline. Care should be taken when heating Blown Bitumen 105/15 to avoid overheating.
Blown Asphalt 105/15 CHARACTERISTICS
CHARACTERISTIC | Test method | Unit | Specification |
Specific gravity @25/25 C | ASTM D70 | (Kg/m3) | 1.05 approx. |
Penetration @ 25°c | ASTM D5 | mm/10 | 10/20 |
Softening point °c | ASTM D36 | °C | 100/110 |
Loss on heating(wt) % | ASTM D6 | Wt. % | 0.2 max |
Flashpoint c | ASTM D92 | °C | 250 min |
Solubility is CS2(wt) % | ASTM D4 | Wt. % | 99.5 max |
Spot test | A.A.S.H.O.T102 | — | Negative |
Blown asphalt 105/15 Packing
Various packings are available for customer’s purpose and conveniences. TAVOIL CO is the manufacturer of asphalt 105/15 in various packing including Kraft bag, meltable plastic bag, drum, and bulk oxidized asphalt 105/15 from penetration grade bitumen.
TAVOIL asphalt 105/15 perchance is supplied in any grade and is designated by two numbers to indicate the softening point and penetration ranges. The oxidized asphalt grade 105/15 means the softening point is 105 and penetration are 15 desi millimeters is produced in compliance and conformity with ASTM standard and meets the following specification.
Oxidized Bitumen 150/5
Oxidized Bitumen 150/5 Description
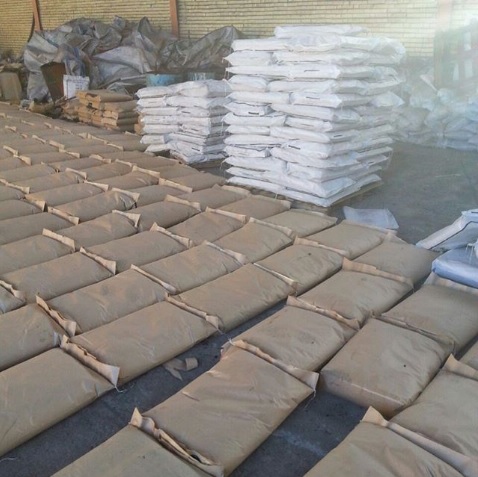
Oxidized bitumen 150/5 is based on petroleum bitumen which is made by blowing bitumen 60/70 by hot air. This type of bitumen is hard and breakable. Oxidized bitumen 150/5 is the semi-solid oxidized grade of petroleum bitumen categorized in polycyclic aromatic hydrocarbons is normally used for different purposes in the construction industries. bitumen 150/5 should be heated double temperature (200ᵒ-300ᵒC) against the softening point to be able to have flow and viscosity. Normally heating of such hard oxidized bitumen should be arranged via hot oil by circulation inside of the isolated jacket. Bitumen oxide 150/5 from penetration grade bitumen, which is blown by hot air in a controlled process until the desired specification is reached. HJ Oil oxidized bitumen 150/5 can be supplied in any grade and are designated by two numbers to indicate the softening point and penetration ranges. The oxidized bitumen 150/5 means the softening point is 150°c and penetration is 15 desi millimeter is produced in compliance and conformity with ASTM standard.
Oxidized Bitumen 150/5 Applications
This Grade of Oxidized uses in the chemical, raw material for bitumen coat, lacquers, varnishes, paper-pulp-board, textile processing, pavement, crack seal and repairmen, civil works, bitumen coat for piping, roofing, construction industries; sealing and insulating buildings, adhesive, construction materials additive, road construction, dust-binding, insulating and impregnating agent, isolation bitumen membrane sheet, make rubber and plastic products. bitumen 150/5 products are for paving, roofing; also used in asphalt-based paints for corrosion protection of metals, inlining public works structures, adhesives in electrical laminates, the base for synthetic turf; typical uses for bitumen 150/5 include roofing, pipe coating, hydraulic applications, 150/5 is mainly using in paint manufacturing and coating in the hot area.
Before using bitumen 150/5 surfaces must be dry, clean, and free of loose particles, curing products, irregularities, and slurry. If you use this type of bitumen without cleaning the area the bitumen 150/5 will easily remove.
Blown Asphalt 150/5 Storage/handling
blown asphalt 150/5 has 10 years validity with multi-time heating and cold, please refer to MSDS. It is better to keep the bitumen 150/5 under shelter and out of the rain, the sun.
Blown Asphalt 150/5 Packing
bitumen 150/5 is available in 25 kg meltable and craft bag, drum, and bulk. Normally oxidized bitumen packing on the pallet and 40 bags can stack on the pallet. 20 pallets can load to the 20ft container.
Specification of Oxidized Bitumen 150/5
Analysis of Blown Asphalt 150/5
Bitumen 150/5 | Test method | Unit | Specification |
Specific gravity @25/25 C | ASTM D70 | (Kg/m3) | 1.05 approx. |
Penetration @ 25°c | ASTM D5 | mm/10 | 4/6 |
Softening point °c | ASTM D36 | °C | 145/155 |
Ductility @25 °c | ASTM D113 | Cm | 1.5min |
Loss on heating(wt) % | ASTM D6 | Wt. % | 0.2 max |
Flashpoint c | ASTM D92 | °C | 250 min |
Solubility is CS2(wt) % | ASTM D4 | Wt. % | 99.5 max |
Spot test | A.A.S.H.O.T102 | — | Negative |
Health & Safety of Blown Asphalt 150/5
Workers should wear protective masks, gloves, and goggles during application. The asphalt can be removed from equipment and tools with kerosene or gasoline. Care should be taken when heating oxidized Bitumen 150/5 to avoid overheating.
Micronized Gilsonite Powder
Micronized Gilsonite Powder Description

HJ Oil Group Supplies Micronized Gilsonite powder with a diameter of 80 to 400 mesh and ashes from 0% to 25%.
The company is taking advantage of experts who are capable of processing Gilsonite lump to alter them to powder with the size 80 to 400 mesh and packing according to customer’s order.
Gilsonite is a Soft Rock, meaning that it can be simply made into Gilsonite Powder. A 200m2 industrial unit is sufficient to set up a grinding mill, while complimentary packaging equipment is also necessary to wrap Gilsonite into different packaging, from 1 MT jumbo bags to 25 kg worker bags.
The technology of grinding minerals is vast and advanced expertise which has been developed in different countries. The tricky part of Gilsonite pulverizing is about one of its principal characteristics, i.e. having BITUMEN CONTENT inside. Applying energy into natural bitumen releases the bitumen content, therefore taking the rock asphalt under grinding, makes it a sticky powder, especially if the temperature is not properly controlled during the process.
Depending on the method of grinding, Gilsonite can be made in different mesh sizes, starting from 30 to 400 for Simple crushing machinery. Mesh size goes up to 500 – 1000 Mesh in case a Fusion unit is added.
Still many claims to supply a 3,000 Mesh Gilsonite Product which is a myth, considering there is no economical way to measure such dust particle size.
Another challenge is an environmental hazard. Pollution resulting from grinding the natural bitumen can end up in stopping the facility from production by the authorities in many countries. Still, There are primitive (using back filters) and advanced ways (using output Catalysts) to rectify the issue.
Packing of Micronized Gilsonite Powder
1– (25 kg± 5%) multi-layer laminate bags.
2– (25 kg± 5%) multi-layer paper bags.
3– (25 kg± 5%) multi-layer Sacks.
4– (25 kg± 5%) gunny bag.
Gilsonite Powder Specification
Data Sheet of Gilsonite 5-10%
Color in Mass | Black |
Color in streak or powder | Brown-Black |
Softening point | 160-220 |
Moisture content | <3 |
Specific gravity@ 77℉ | 1.02-1.2 |
Hardness (mohr’s scale) | 2 |
Penetration | 0 |
Flash point,°C, C.O.C | >290 |
Trace elements | <1 |
Solubility in T.C.E Wt% | 70-85 |
Solubility in CS2,Wt% | 70-90 |
Ash | 5-10 |
Fixed carbon | 25-35 |
Data Sheet of Gilsonite 10-15%
Color in mass | Black |
Color in streak or powder | Black |
softenin point | 200- 240˚C |
Moisture content | <3 |
Specific gravity @77˚F | 1.04-1.06 |
Hardness (Mohr҆ s scale) | 2 |
Penetration | 0 |
Flash point,˚C,C.O.C | 280< |
Trace elements | <1 |
Volatile matter | 55-70 |
Ash | 10-15 |
Fixed carbon | 20-35 |
Data Sheet of Gilsonite 15-20%
Color in mass | Black |
Color in streak or powder | Black |
Softening point | 220-260˚C |
Moisture content | <3 |
Specific gravity @77˚F | 1.04-1.2 |
Hardness (Mohr҆ s scale) | 2 |
Penetration | 0 |
Flash point,˚C,C.O.C | 300< |
Trace elements | <1 |
Solubility in T.C.E., Wt% | 70-85 |
Volatile matter | 60-75 |
Ash | 15-20 |
Fixed Carbone | 20-35 |
Data sheet of Gilsonite 20-25%
Color in mass | Black |
Color in streak or powder | Black |
Black softening point | 220-260˚C |
Moisture content | <3 |
Specific gravity @77˚F | 1.04 -1.2 |
Hardness (Mohr҆ s scale) | 2 |
Penetration | 0 |
Flash point,˚C,C.O.C | 300< |
Trace elements | <1 |
Solubility in T.C.E., Wt% | 60-70 |
Solubility in CS2,Wt% | 70-80 |
Volatile matter | 60-75 |
Ash | 20-25 |
Fixed Carbone | 20-35 |
Granul Gilsonite
Granul Gilsonite Description

HJ Oil Group Supplies Granul Gilsonite with a diameter of 30 to 40 meshes and ashes from 0% to 25%.
Gilsonite mines are respectively the largest reserves in the United States, Canada, Iraq, Russia, Venezuela, China, Australia, Mexico, Albania, and the Philippines (USGS, 2007; USGS, 2016a). The largest Gilsonite reserves in the world are located in Utah and Colorado states that have been estimated to contain the reserve of 45 million tons, according to the US Geological Survey (Pruitt, 1961; USGS, 2016a,b). Overall, about 65 percent of Gilsonite reserves are located in the North American continent consist of the United States and Canada, and Iran accounts for about 15 percent of these reserves as the third largest natural bitumen reserve globally (USGS, 2007; USGS, 2016a).
Packing of Granul Gilsonite
(25 kg± 5%) multi-layer laminate bags.
(25 kg± 5%) multi-layer paper bags.
(25 kg± 5%) multi-layer Sacks.
(25 kg± 5%) gunny bag.
It also can be palletized, shrank, and wrapped based on the customer’s request.
Granul Gilsonite Specification
Data Sheet of Gilsonite 5-10%
Color in Mass | Black |
Color in streak or powder | Brown-Black |
Softening point | 160-220 |
Moisture content | <3 |
Specific gravity@ 77℉ | 1.02-1.2 |
Hardness (mohr’s scale) | 2 |
Penetration | 0 |
Flash point,°C, C.O.C | >290 |
Trace elements | <1 |
Solubility in T.C.E Wt% | 70-85 |
Solubility in CS2,Wt% | 70-90 |
Ash | 5-10 |
Fixed carbon | 25-35 |
Data Sheet of Gilsonite 10-15%
Color in mass | Black |
Color in streak or powder | Black |
softenin point | 200- 240˚C |
Moisture content | <3 |
Specific gravity @77˚F | 1.04-1.06 |
Hardness (Mohr҆ s scale) | 2 |
Penetration | 0 |
Flash point,˚C,C.O.C | 280< |
Trace elements | <1 |
Volatile matter | 55-70 |
Ash | 10-15 |
Fixed carbon | 20-35 |
Data Sheet of Gilsonite 15-20%
Color in mass | Black |
Color in streak or powder | Black |
Softening point | 220-260˚C |
Moisture content | <3 |
Specific gravity @77˚F | 1.04-1.2 |
Hardness (Mohr҆ s scale) | 2 |
Penetration | 0 |
Flash point,˚C,C.O.C | 300< |
Trace elements | <1 |
Solubility in T.C.E., Wt% | 70-85 |
Volatile matter | 60-75 |
Ash | 15-20 |
Fixed Carbone | 20-35 |
Data sheet of Gilsonite 20-25%
Color in mass | Black |
Color in streak or powder | Black |
Black softening point | 220-260˚C |
Moisture content | <3 |
Specific gravity @77˚F | 1.04 -1.2 |
Hardness (Mohr҆ s scale) | 2 |
Penetration | 0 |
Flash point,˚C,C.O.C | 300< |
Trace elements | <1 |
Solubility in T.C.E., Wt% | 60-70 |
Solubility in CS2,Wt% | 70-80 |
Volatile matter | 60-75 |
Ash | 20-25 |
Fixed Carbone | 20-35 |
Lump Gilsonite
Lump Gilsonite Description

Lump Gilsonite, or Natural Asphalt, Natural Bitumen is a natural, resinous hydrocarbon This natural asphalt is similar to a hard petroleum asphalt and is often called a natural asphalt, asphaltite, uintaite, or asphaltum. Natural asphalt is derived from the natural mutation of petroleum. This mutation happened a million years again under the influence of bacteria. This bacterial decomposition of petroleum resulted in reducing the content of saturated hydrocarbons, mainly n-alkalenes and light oil which became heavier and more viscous, taking the form of asphalt. It is a natural product a bituminous limestone in which carbonate of lime and pure natural asphalt are most intimately combined by a neutral agency. It is as bitumen created in the process of crude oil processing. It is native substances of variable color, hardness, and volatility, composed principally of the elements carbon and hydrogen and sometimes associated with mineral matter and essentially free of gas. Gilsonite is soluble in aromatic and aliphatic solvents, as well as petroleum asphalt. Due to its unique compatibility, gilsonite is frequently used to harden softer petroleum products. Gilsonite in mass is a shiny, black substance similar in appearance to the mineral obsidian. It is brittle and can be easily crushed into a dark brown powder. Gilsonite is found below the earth’s surface in vertical veins or seams that are generally between two and six feet in width but can be as wide as 28 feet.
Due to the narrow mining face, Gilsonite is mined today, much like it was
50 or 100 years ago. The primary difference is that modern miners use pneumatic chipping hammers and mechanical hoists.
Packaging of Lump Gilsonite
One metric ton new jumbo bags.
These Products can be palletized, shrank, and wrapped according to customer’s request.
Lump Gilsonite Specification
Data Sheet of Gilsonite 5-10%
Color in Mass | Black |
Color in streak or powder | Brown-Black |
Softening point | 160-220 |
Moisture content | <3 |
Specific gravity@ 77℉ | 1.02-1.2 |
Hardness (mohr’s scale) | 2 |
Penetration | 0 |
Flash point,°C, C.O.C | >290 |
Trace elements | <1 |
Solubility in T.C.E Wt% | 70-85 |
Solubility in CS2,Wt% | 70-90 |
Ash | 5-10 |
Fixed carbon | 25-35 |
Data Sheet of Gilsonite 10-15%
Color in mass | Black |
Color in streak or powder | Black |
softenin point | 200- 240˚C |
Moisture content | <3 |
Specific gravity @77˚F | 1.04-1.06 |
Hardness (Mohr҆ s scale) | 2 |
Penetration | 0 |
Flash point,˚C,C.O.C | 280< |
Trace elements | <1 |
Volatile matter | 55-70 |
Ash | 10-15 |
Fixed carbon | 20-35 |
Data Sheet of Gilsonite 15-20%
Color in mass | Black |
Color in streak or powder | Black |
Softening point | 220-260˚C |
Moisture content | <3 |
Specific gravity @77˚F | 1.04-1.2 |
Hardness (Mohr҆ s scale) | 2 |
Penetration | 0 |
Flash point,˚C,C.O.C | 300< |
Trace elements | <1 |
Solubility in T.C.E., Wt% | 70-85 |
Volatile matter | 60-75 |
Ash | 15-20 |
Fixed Carbone | 20-35 |
Data sheet of Gilsonite 20-25%
Color in mass | Black |
Color in streak or powder | Black |
Black softening point | 220-260˚C |
Moisture content | <3 |
Specific gravity @77˚F | 1.04 -1.2 |
Hardness (Mohr҆ s scale) | 2 |
Penetration | 0 |
Flash point,˚C,C.O.C | 300< |
Trace elements | <1 |
Solubility in T.C.E., Wt% | 60-70 |
Solubility in CS2,Wt% | 70-80 |
Volatile matter | 60-75 |
Ash | 20-25 |
Fixed Carbone | 20-35 |