Gilsonite In Industry
Gilsonite Usage In Industry

Industry Usage of Gilsonite consists of inks & Paints, Asphalt, Isolation, Chemical, Coating, Foundry, and construction.
Gilsonite Usage in Inks & Paints
Because of the unique properties of Gilsonite, it gives the paint an excellent bond to almost any material that needs to be protected from the elements. It is a critical high-performance, low-cost paint additive for anticorrosive paints, underbody paints, and pipe coatings.
The superior performance of Gilsonite means you can find it in the majority of wood stains produced in the U.S. In this application, the unique properties of Gilsonite make it both a binder to protect the wood, and a pigment that gives a deep, rich color that won’t fade over time. Gilsonite paint additive is Naturally Better and you just can’t get this performance with any other material—natural or synthetic.
A paint consisting essentially of 20 gallons of petroleum solvent, 10 gallons of linseed oil, 10 gallons turpentine, pounds ofGilsonite pigment, 4 gallons varnish mixture consisting of 17.8% pentaerythritol rosin ester, 30.8% dehydrated castor oil, 1.4% of a mixture of lead, cobalt and manganese naphthenates, 1-gallon wetting agent consisting essentially of salts of petroleum sulfonic acids, 2 quarts of drier, and 1 pint of a hydrocarbon silicon penetrating oil, obtained by heating a mixture of finely ground silicon dioxide under pressure to a temperature of about 300 F. with a distillate product obtained by subjectingGilsonite to fractional distillation, said distillate product being that fraction which distills at a temperature range of about 430 F. to 438 F.
Gilsonite is widely used as the primary carbon black wetting agent for black news inks and headset and toner inks. PUB Gilsonite Resin competes advantageously with hydrocarbon resins, phenolic resins.
Advantages of Using Gilsonite In Inks & Paints
- Superior binding properties for many materials
- UV light stability
- Fade-resistant transparent pigment gives a deep, rich color to wood stains
Gilsonite Usage In Asphalt
Gilsonite makes roads stronger to last longer.
As an asphalt binder modifier, the unique properties of Gilsonite make a road that is less susceptible to high-temperature and deformation performance issues. When these modified binders are used in recycled asphalt pavements, Gilsonite adds back what time has taken from the old asphalt, making it easier to use more of this recycled material. The Gilsonite-modified asphalt binder will produce a stronger road that can be thinner by nearly 20 percent compared with other pavements. For more information about this application, please contact us.
As an aggregate modifier, Gilsonite can be added directly at the hot mix plant with no additional equipment. The excellent bonding properties of Gilsonite will produce a high-strength, high-performance pavement that also resists water stripping.
Advantages of Using Gilsonite In Asphalt
- High strength and durability
- Superior deformation performance
- Reduced pavement thickness
- Reduced temperature susceptibility
- Increased resistance to water stripping
Gilsonite Usage In Isolation
Gilsonite in isolation is most used to the production of isogamy.
By mixing Gilsonite, calcium carbonate, and bitumen with stretch enhancer oil, it is produced by isogamy that creates composite and increases the thermal resistance of the rubble and creates a stable and homogeneous coating.
Advantages of Using Gilsonite In Isolation
- Increased shear strength
- Increased resistance to the movement of layers
- Low-temperature flexibility is maintained
- Reduced the tendency of the isogamy to move and use on sloping surfaces.
- Reduced fluctuations at high temperatures
- The combination of low-temperature flexibility and high-temperature shear strength and resistance to motion
Gilsonite Usage In Chemical Industry
Gilsonite is widely Used in the production of glue and sealant. This material is a good lubricant and in combination with other chemicals, various products can be obtained. Some uses of Gilsonite in chemicals is in Ceramic production, Rubber industry, Wood industry, Steel product.
Gilsonite Usage In Coating Industry
Gilsonite is used for preventing the pipes from corrosion and it acts as an additive in pipe isolator, which increases the pipe life significantly. Gilsonite is used in different industries as a resin for waterproofing purposes, for example in the Automobile industry it is used as an additive in the coating car’s underbody.
Gilsonite Usage In Foundry & Construction
For your complex, high-value iron castings, Gilsonite performs like no other carbon additive. Gilsonite’s naturally superior properties mean high-quality castings with better finish and fewer imperfections. Gilsonite Can combine with coal and other ingredients as an additive in foundry sands to ensure the quality of the molded part. The lower gas evolution should reduce the ventilation load on the pouring floor. The physical property relationships developed in new mixes were confirmed by sand using Gilsonite as an additive. Gilsonite is a carbonate additive too and can be added to sands of foundry and play the role of a strong adhesive for them.
Advantages of Using Gilsonite In Foundry & Construction
- Three times as much gas generated vs. sea-coal for better mold release
- High lustrous carbon for a better finish
- The reductive atmosphere for less reaction between mold and casting for fewer imperfections
Oil & Gas
Gilsonite In Oil & Gas

In the oil and gas industry, drilling fluids or liquids perform a diversity of operations that influence the drilling rapidity, efficiency, safety, and the cost of drilling operators. An important characteristic of gilsonite that makes it noteworthy for drilling fluid usages is its softening-point temperature. There are many types of drilling fluid systems available such as water-base muds, oil-base muds, stable foam muds, air, or gas base muds from which the right system may be chosen. In water-based muds, it is used as a shale-stabilizing additive and is difficult to evaluate unless tested at or above its softening point. In oil-based muds, it is used as a fluid-loss control agent.
With unmatched benefits in cementing and drilling fluids, Gilsonite is proven under pressure.
With a unique blend of strength, flexibility, bonding, and high-temperature capability, Gilsonite adds properties that increase performance in cementing and drilling fluids in a way no other single additive can.
Gilsonite is used in drilling mud fluids and oil well cementing. Gilsonite, in a range of softening points and particle sizes, is a standard ingredient in oil-based drilling muds used in shales and other difficult geological formations. The addition of specially-treated Gilsonite to water-based drilling fluids helps minimize hole washout by stabilizing troublesome shales and seals off highly permeable sands while reducing torque and drag. The addition of Gilsonite to oil well cement reduces slurry weight without loss of compressive strength and acts as an effective bridging and plugging agent to seal fractures in weak formations while cementing. Also, Gilsonite use in Mud drilling according to FLC ” Filtrate Loss Control ” or ” Fluid Loss Control ” in oil-base mud.
Drilling fluids features of Gilsonite in Oil & Gas
- Provides superior shale stabilization
- Prevents differential sticking
- Reduces or eliminates lost circulation
- Provides wellbore strengthening matrix
Cementing features
- Strengthens cement bonds to shales and sands
- Reduces cement slurry density
- Prevents lost circulation
- Supports compressive strength development
Gilsonite
Gilsonite Description

Gilsonite is a naturally occurring glossy black asphaltic, solid hydrocarbon resin with low specific gravity. It occurs in its very pure natural state in a mineral called Uintaite. Gilsonite or Natural Asphalt is a natural, resinous hydrocarbon found in northeastern Utah. Natural Asphalt is a unique natural hydrocarbon high in asphaltenes and nitrogen compounds so it is a granular solid that is fully compatible with bitumen. It can be melted into hot bitumen, added during the hot-mix manufacturing process, or blended into a preservation treatment.
This natural asphalt is similar to a hard petroleum asphalt so it’s other names are natural asphalt, asphaltite, uintaite, or asphaltum. Gilsonite is soluble in aromatic and aliphatic solvents, as well as petroleum asphalt. Due to its unique compatibility, natural asphalt is frequently used to harden softer petroleum products. natural asphalt in mass is a shiny, black substance similar in appearance to the mineral obsidian. It is brittle and it can easily crush into a dark brown powder.
Gilsonite is below the earth’s surface in vertical veins or seams that are generally between two and six feet in width but also can be as wide as 28 feet. The veins are nearly parallel to each other and they are in orient-shape in a northwest to southeast direction. They extend many miles in length and as deep as 1500 feet. The vein will show up on the surface as a thin outcropping and gradually widen as it goes deeper. Due to the narrow mining face, natural asphalt is mined today, much like it was 50 or 100 years ago. The primary difference is that modern miners use pneumatic chipping hammers and mechanical hoists.
Gilsonite Applications
1- In Oil & Gas
- Drilling Fluid Loss Control
- Cementing
2- In industry
- Inks & Paints
- Asphalt
- Isolation
- Chemical Products
- Coating
- Foundry & Construction
Different Grades Of Gilsonite:
Gilsonite
1- with ash content up to 5%, moisture up to 1%, and meshes 30, 40, 100, and 300.
2- with ash content up to 10%, moisture up to 1%, and meshes 30, 40, 100, and 300.
3- with ash content up to 15%, moisture up to 1%, and meshes 30, 40, 100, and 300.
4- with ash content up to 20%, moisture up to 1%, and meshes 30, 40, 100, and 300.
5- with ash content up to 25%, moisture up to 1%, and meshes 30, 40, 100, and 300.
Bitumen Coating
Bitumen Coating

Bitumen coating compositions having substantially improved application and drying properties and producing coatings of improved properties including resistance to ultraviolet rays and alligatoring resulting therefrom said coating compositions comprising volatile solvent solutions of a bitumen coating material having softening point between 110 F To 250 F. The bitumen coating are also characteristically non-viscous materials which are not thixotropic and are therefore ordinarily applied as thin films. The bitumen coating compositions may also contain filler materials which tend to settle from the non-thixotropic compositions after storage for only a short time. It has been proposed in the past to add inert colloidal fillers such as silica to obtain thixotropic properties and thicker films on the application of the compositions. However, even such inert fillers tend to affect only solution properties and generally exist in the finished coating as an expensive additive that does not benefit other properties of the coating.
Bitumen Pipe Coating
Bitumen pipe coat can be used both externally and internally on carbon steel pipes. It is usually black, and when applied properly, this coating offers outstanding cathodic protection needed for almost all structural steel pipes situated underground. It is regarded as one of the least expensive ways to provide cathodic protection to pipes. It is also the least complex coating process, making it suitable for casing pipes like in road bore.
Bitumen Paint
Asphalt paint is produced with asphalt as the main material and gasoline as the solvent and through the processes of material selection, dissolving, and sealing in the container. It is in a flowing or semi-flowing state and has a high viscosity and good durability, and its use needs no fire melting. The said asphalt paint is used in sealing roofing, sandwiched layer, etc. In various building engineering.
Bitumen Adhesive, Bitumen Glue
Bituminous adhesive glue is used in cold gluing of construction material in particular for its watertight properties. The known glue is thixotropic, which means that it becomes fluid when shaken, stirred, or otherwise agitated and sets again to a gel when allowed to stand. The thixotropic properties of the known glue are obtained by the presence of both the polymerized oil in combination with the ethyl-vinyl-acetate copolymer resin (EVA) and the non-polymerized oil in combination with oil-absorbing fillers. The use of the combination of these compounds has the advantage that it provides the thixotropic properties without having to use some organic solvents.
Bitumen Felt
An asphalt felt belongs to the field of the building materials. The utility model is characterized in that a solid bitumen thin layer is attached on one surface of the asphalt felt; when the utility model is used, the liquefied bitumen can be first brushed on the top of the storied building using a brush and then one surface of the asphalt felt which the solid bitumen thin layer is attached on the top of the storied building, and the solid bitumen thin layer is syncretized with the liquefied bitumen on the top of the storied building by using a burner to deliver heat with resulting in that the asphalt felt is uniformly covered without causing waste, thus not only enhancing the effect of preventing the seepage of the rainwater but also correspondingly reducing the workload due to that the amount of the used bitumen is reduced. The utility model has a reasonable design and can be used conveniently.
Bitumen Tape
The bitumen tape of the invention is suitable for sanitary and building applications for sealing against water and in vehicles for sealing or for sound insulation especially for the construction or repair of roofs, covering joints, or for the tight connection between masonry or concrete and installing parts like the window frame or sheet metal. The width of the bitumen tape preferably from 24 to 105 mm.
Bitumen Sheet
The bitumen sheet material is transported to a construction or use site, and the sheet material is cut to the desired lengths. The releasable casting film material is removed to expose the tackified surface, and the tacky surface then placed, i.e. Pressed, against the masonry or other surfaces it is designed to protect, and held in place by the tacky nature of the exposed surface of the bitumen layer.
Bitumen Joint Sealer
Bitumen joint sealer dispersion as the sealant to male and/or female sections, even. Of the water and assembly of the joint under sufficient axial pressure to force out some of the sealants on both inside and outside of the joint. Used for sealing of drinking and wastewater pipes, telephone conduits, expansion joints, cracks in masonry, etc. Good adhesion to pipe surfaces of all types is obtd. No displacement of adhesive during assembly of joint occurs, and there is no deformation or embrittlement during long periods of use. Efficient sealing over large contact areas is also obtd.
Bitumen Sealant
Bitumen sealant is a single component, neutral curing, high modulus, fast curing speed. And good adhesive capacity on many base material, having excellent weather ability, And resistance to the bitumen sealant can be applied in any season and easy to apply. There is high bonding strength, non-corrosive, have a strong seal with the majority of Construction materials.
Bitumen Crack Sealer
Crack sealer is deep enough, a grout material, such as a mortar or cement, is used to assist in filling these cracks. In these instances, the grout material is placed in the crack and allowed to harden. Thereafter, the asphalt sealer is placed in the crack over top of the grout material to completely fill the crack and level out the paved surface. This can also create durability issues in that existing grout fillers that are used in crack repair applications often have significant shrinkage issues. Thus, while an asphalt sealer used to help fill a crack may initially be level with the surface being repaired when the grout material shrinks, the asphalt sealer will drop into the crack as the level of the grout material recedes. The asphalt sealer thus is no longer flush with the upper paved surface and often falls into the crack itself.
Bitumen Metal Surface
Bitumen metal surface coat, preparation of the surface is of great importance and will influence the degree of adhesion obtained along with the life of the coating. All surfaces must be sound, stable, and thoroughly cleaned. Anti-corrosive bitumen may be applied on slightly damp but not wet surfaces. For excellent results apply on the dry surface only.
Bitumen Packing
Bitumen in 1MT Jumbo Bag and 300kg BituBag Packing

Bitumen Packing like Bitubags and Jumbo Bags can be a cost-efficient solution to alternate for Bitumen drums. Bitubags can be in two types: 1000 kg and 300kg.
The 300kg Bitubags contain a two-layer cover, which the first tears up and the second burns and melt in the destination tanker (reservoir) Transportation and stuffing: each 20 feet container can hold 18 Jumbo bags (1 MT) or 70 Bitubag (300 kg) so the 300kg bags result in more cost-effective land and ocean freight costs.
Polybags: packing specification: Packed in 3-PLY Poly Bags of 32 Kg (+/-3) Net Weight (Not Available at the moment).
The Bitubag Packing System is a comprehensive cold bitumen logistic/supply chain solution from A to Z for the bitumen industry. It addresses all aspects of the bitumen producer, the logistics, the distributor, and the end-user.
The core element is the Bitumen Bag packing system, a light-weight, durable and flexible bag optimized for container transport that enables several economic and logistic advantages for the entire supply chain. With its unparalleled features, Bitubag packing can increase the producer’s margins, reduce transport costs, and reach markets that could not be supplied economical so far.
Furthermore, with the Bitubag packing system, Bitumen can be stored at virtually no cost. Huge investments in terminals and storage infrastructure become obsolete.
Advantages of Use Bitumen Bag Packing for end-Users

Total flexibility for the bitumen operation
- Availability of bitumen at the site to be used whenever it is needed
Independent of hot bitumen sources - Every conventional means of transport can be used (standard trucks,
20 ft. containers, train, ship) for regional or international transport - Long-term storage up to 12 months without any energy consumption
- Independence of seasonal fluctuations of supply and/or demand
- Expand your bitumen sales market
- Melt and supply just-in-time on-demand
- Balancing seasonal fluctuations
- Substantial energy saving – no heating required during transport and storage
- Significant cost savings over the entire supply chain compared to conventional bulk transport, bitutainers or drums
- Reduce environmental foot-print
- Reliable and efficient equipment (CPU and high-performance melters)
- More independence and flexibility for your supply chain
Bitumen in 1MT Jumbo Bag
To transport bitumen anywhere, a reliable and efficient logistic system is needed – using the fewest special infrastructures, lowest possible total energy consumption, as well as safe and easy storage and handling. For this purpose, the Bitumen Bag Packing System was created.
It allows you to produce, pack, store, transport and sells bitumen independently of seasonal demand, fluctuation, or logistical issues.
It enables the producer to store and use bitumen at any time, cost-effectively, and in any quantity that will meet your requirements.
1. cooling & packing unit
- The Cooling & Packing Unit (CPU) cools the bitumen down to the packing temperature. The process ensures a stable filling temperature.
- and is designed for the safe, continuous filling of the Bitumen Bag with paving bitumen.
- An electronic control system provides for the exact weighing and the complete monitoring and registration of the product as well as the weight of each individual bag.
2- bitumen bag
- The bag is designed as a self-stabilizing container made of plastic material, consisting of a multi-layer outer bag (flexible recyclable fabric) and an inner liner (special-purpose film).
- The Bitumen Bag can carry over 1,000 kg of paving bitumen. Its shape and volume is optimized for maximum loading.
- The bag can be transported by any common transport system (truck, standard container, rail, ship).
- The bag is UV-protected and suitable for every climate. It and can be stored for up to 12 months.
Logistic of Bitumen Bag Packing

The Bitumen Bag Packing System is equipped to supply large volumes of bitumen. the bitumen processing system and ensures the safe filling of bags where quantities and qualities undergo strict control.
The design of the Bitumen Bag is characterized by economic production costs, greater volume, and high stability. Leading industrial partners produce these standardized bags with a constant high level of quality.
Therefore, bitumen in cold conditions can be transported by conventional trucks or sea containers over distances of many thousand miles from continent to continent.
Bitumen in the jumbo bag is the safest and easy handling from loading to destination. Jumbo bag should be designed for bitumen and if you buy from the market and fill bitumen will become fat or collapse. Normally design of bitumen in the jumbo bag is in the bottom the size is bigger than the top and should have the angle to become stable.
Bitumen Classification
Bitumen Classification
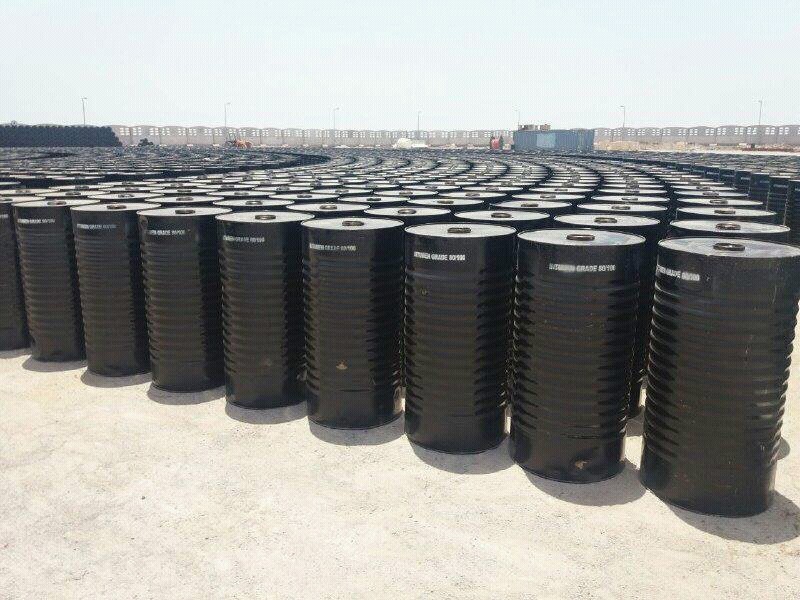
Bitumen classification is according to viscosity (degree of fluidity) gradings. The higher the grade, the stiffer the bitumen. Most high performing roads in Australia are built and maintained using bitumen because it is durable and has exceptional waterproofing and adhesive properties. Bitumens used in road construction and maintenance are refined and blended to meet strict road engineering requirements and industry specifications.
Paving Grade Bitumen Class 170
Class 170 bitumen is widely used in sprayed sealing and light asphalt applications to provide durability and fatigue resistance. It is also used to manufacture cutback bitumens, bitumen emulsions, and modified bitumens.
Paving Grade Bitumen Class 240
Class 240 bitumen is for use in sprayed sealing applications where the local road agency has a preference for a slightly more viscous bitumen than Class 170.
Paving Grade Bitumen Class 320
Class 320 bitumen is most commonly used to manufacture asphalt mixes. Due to its higher viscosity, stiffer asphalt mixes can be produced to improve resistance to shoving and other problems associated with higher temperatures and traffic loads.
Paving Grade Bitumen Class 450
Class 450 bitumen is for use in the manufacture of asphalt mixes where the local road agency has a preference for a slightly more viscous bitumen than Class 320.
Bitumen Class 600
Class 600 bitumen is primarily used to manufacture extra heavy-duty asphalt pavements that need to endure substantial traffic loadings.
Applications
The table below shows typical applications for paving grade bitumens:

Application Temperature Recommendations
Type | C170 | C240 | C320 | C450 | C600 |
Asphalt Mixing | 150 – 160°C | 155 – 165°C | 155 – 165°C | 160 – 170°C | 165 – 175°C |
Asphalt Compaction | 135 – 150°C | 140 – 155°C | 140 – 155°C | 145 – 160°C | 150 – 165°C |
Sprayed Sealing | 175 – 185°C | 180 – 190°C | 180 – 190°C | N/A | N/A |
Typical Characteristics
Type | C170 | C240 | C320 | C450 | C600 |
Viscosity at 60°C, Pa.s | 170 | 240 | 320 | 450 | 600 |
Viscosity at 135°C, Pa.s | 0.4 | 0.45 | 0.53 | 0.66 | 0.8 |
Viscosity at 60°C, after RTFO, Pa.s | 300 | 470 | 640 | 920 | 1300 |
Penetration at 25°C, dmm | 70 | 58 | 46 | 36 | 27 |
Flashpoint, 60°C | 360 | 360 | 360 | 360 | 360 |
Viscosity of residue at 60°C, % of original | 180 | 190 | 200 | 205 | 215 |
Density at 15°C, kg/m3 | 1.04 | 1.04 | 1.04 | 1.04 | 1.04 |
Storage & Handling
The storage of bitumens for prolonged periods at elevated temperatures should be avoided as quality may be adversely affected. As a general rule, bitumen should be stored at the lowest temperature that enables practical use. For normal operations, such as blending and transferring liquid bitumen, temperatures of 10°C to 40°C above the minimum pumping temperature are recommended.

Health & Safety
To ensure hot bitumen is used safely and efficiently the following safety precautions must be followed:
– Wear suitable personal protective equipment (PPE) at all times. Full skin protection is required to avoid accidental burns when transferring or handling hot bitumen.
– Always prevent contact between water and hot bitumen by checking the contents of the previous load before loading bituminous products into tankers and by following procedures to avoid violent boil-over of tanks.
– Avoid exposure to fumes by standing back on the gantry or upwind until the vapors have dispersed.
– Minimize bitumen fume by heating bitumen and asphalt products to the recommended temperatures.
– Minimize the use of diesel when cleaning equipment as this contributes to the bitumen fume.
Polymer Modified Bitumen
Polymer Modified Bitumen Description

Bitumen has been used for thousands of years and its importance as a valued engineering material continues to increase. The interest in the modification of bitumen using polymers, whether virgin, scrap, or polymer blends, is intense. The last two decades, in particular, have seen an increase in the number of academic groups studying polymer-modified bitumen, and correspondingly the peer-reviewed literature in the field has increased. Initially, studies on polymer modified bitumen (PMB) focused more on engineering and empirical measurements, e.g. aging and softening points. However, in recent years a plethora of techniques have been employed in the study of the effect of the addition of polymers on a range of bitumen properties, polymer—bitumen morphology, and polymer—bitumen interactions.
When a polymer is added to regular bitumen, it becomes more elastomeric, which provides it with additional elasticity. The polymer that is added is styrene butadiene styrene (SBS), which acts as a binder modification agent. The primary objective of SBS polymer modified bitumen is to provide extra life to the pavement, roads, and construction designs. Some of the qualities exhibited by PMB are:
- Higher rigidity
- Increased resistance to deformation
- Increased resistance to cracks and stripping
- Better water resistance properties
- High durability
Advantage of using polymer modified bitumen
- stronger road with increased marshall stability value and greater Rigidity.
- better resistance towards rainwater and water stagnation.
- no stripping and no potholes.
- Better resistance to permanent deformation
- reduction in pores in aggregate and hence less rutting and raveling.
- Much higher durability
Common types of Polymer Modified Bitumen
The following table lists some common asphalt cement and HMA modifiers and their general purpose/use.
Type | General Purpose or Use | Generic Examples |
filler | Fill voids and therefore reduce optimum asphalt content Meet aggregate gradation specifications Increase stability Improve the asphalt cement-aggregate bond | Mineral filler crusher fines lime Portland cement fly ash Carbon black |
extender | Substituted for a portion of asphalt cement (typically between 20–35 % by weight of total asphalt binder) to decrease the amount of asphalt cement required | Sulfur Lignin |
rubber | Increase HMA stiffness at high service temperatures Increase HMA elasticity at medium service temperatures to resist fatigue cracking Decrease HMA stiffness at low temperatures to resist thermal cracking (see Figure 2) | Natural Latex Synthetic latex (e.g., Polychloroprene latex) Block copolymer (e.g., Styrene-butadiene-styrene (SBS)) Reclaimed rubber (e.g., crumb rubber from old tires) |
plastic | Polyethylene/polypropylene Ethylene acrylate copolymer Ethyl-vinyl-acetate (EVA) Polyvinyl chloride (PVC) Ethylene propylene or EPDM Polyolefin | |
Rubber-Plastic Combinations | Blends of rubber and plastic | |
Fiber | Improving tensile strength of HMA Mixtures Improving cohesion of HMA Mixtures Permit higher asphalt content without the significant increase in the drain down | Natural: Asbestos Rock wool Manufactured: Polypropylene Polyester Fiberglass Mineral Cellulose |
Oxidant | Increase HMA stiffness after the HMA is placed | Manganese salts |
Antioxidant | Increase the durability of HMA mixtures by retarding their oxidation | Lead compounds Carbon Calcium salts |
Hydrocarbon | Restore aged asphalt cement to current specifications Increase HMA stiffness in general | Recycling and rejuvenating oils Hard and natural asphalts |
Antistripping Agents | Minimize stripping of asphalt cement from aggregates | Amines Lime |
Waste Materials | Replace aggregate or asphalt volume with a cheaper waste product | Roofing shingles Recycled Tires Glass |
Use as needed
While the benefits of using modified asphalts are widely acknowledged, not all asphalt mixes or treatments need to be modified. Each application should be evaluated to determine if the traffic loading, anticipated service life, environmental conditions, and desired performance justify the use of modifiers. Modified asphalts can be a good investment.
The rheological properties of conventional binders may be modified by the introduction of:
Elastomers;
Plastomers;
Crumb rubber;
The modification is costly and is normally justified when bituminous surfacing are subjected to severe conditions such as:
Steep gradients;
Very high road surface temperature;
High traffic loading; or
Heavily trafficked intersections.
Modification may also be advantageous for surfacing on highly flexible and cracked pavements, where an improvement in the rheological properties of the bitumen is required.
Use in such applications should be guided by expert opinion.
In addition to the primary aims above, the range of properties improved include
Durability;
Aggregate retention;
Resistance to permanent deformation;
Resistance to fatigue cracking;
Cohesion (internal strength);
Elasticity;
Viscosity less susceptible to temperature changes.
Modification agents
The primary aim of the modification of bitumen for use in structural layers is to increase the resistance of these layers to permanent deformation at high road temperatures without compromising the properties of these layers over the rest of the prevailing temperature range.
The use of polymer modified bitumen to obtain improved performance is rising as a result of increases in tire pressures, axle loads, and higher traffic volumes.
Improved performance can be achieved in two ways, both of which are aimed at reducing the permanent strain:
An increase in the elastic component with an associated reduction in the viscous component; and
Stiffening of the bitumen to reduce the total viscoelastic response of the layer.
The modification is achieved by the introduction of polymers (including crumb rubber), aliphatic synthetic wax, or naturally occurring hydrocarbons. Polymers can be broadly categorized as “elastomers” (sometimes referred to as thermoplastic elastomers) for improving the strength and elastic properties of a binder, and “customers” (sometimes referred to as thermoplastic polymers) for increasing the viscosity of the bitumen.
Performance Grade Bitumen
Performance Grade Bitumen Description

The performance grade bitumen is based on the evaluation of the material performance when in use, unlike being rational as in the viscosity grading system. The viscosity grading system is more into the experience-based method of grading. And this has proved to have excellent performance for over 20 years in US pavement construction.
The Superpave grading was developed as a part of a 5year strategic highway research planning (SHRP) from 1987 to 1992, to have a performance-based grading system for bitumen. These were developed based on the engineering features that will help in solving many of the engineering problems.
Penetration grading and viscosity grading are somewhat limited in their ability to fully characterize asphalt binders for use in HMA pavement. Therefore, as part of the Superpave research effort, new binder tests and specifications were developed to more accurately and fully characterize asphalt binders for use in HMA pavements. These tests and specifications are specifically designed to address HMA pavement performance parameters such as rutting, fatigue cracking, and thermal cracking.
Superpave Performance Grade Bitumen is based on the idea that an HMA asphalt binder’s properties should be related to the conditions under which it is used. For asphalt binders, this involves expected climatic conditions as well as aging considerations. Therefore, the PG system uses a common battery of tests (as the older penetration and viscosity grading systems do) but specifies that a particular asphalt binder must pass these tests at specific temperatures that are dependant upon the specific climatic conditions in the area of use. Therefore, a binder used in the Sonoran Desert of California/Arizona/Mexico would have different properties than one used in the Alaskan tundra. This concept is not new – the selection of penetration or viscosity graded asphalt binders follows the same logic – but the relationships between asphalt binder properties and conditions of use are more complete and more precise with the Superpave PG system. Information on how to select a PG asphalt binder for a specific condition is contained in the Superpave mix design method. Table 1 shows how the Superpave PG system addresses specific penetration, AC, and AR grading system general limitations.
Performance Grade (PG) bitumen is bitumen which is graded based on its performance at different temperatures. The Long-Term Pavement Performance(LTPP) has given certain algorithm to calculate the temperature of the pavement based on the temperature of the air above. From this, the highest and the lowest temperatures of the pavement is calculated and the bitumen that performs well in that temperature range is selected.
Limitations of Penetration, AC and AR Grading Systems | Superpave Binder Testing and Specification Features that Address Prior Limitations |
---|---|
Penetration and ductility tests are empirical and not directly related to HMA pavement performance. | The physical properties measured are directly related to field performance by engineering principles. |
Tests are conducted at one standard temperature without regard to the climate in which the asphalt binder will be used. | Test criteria remain constant, however, the temperature at which the criteria must be met changes in consideration of the binder grade selected for the prevalent climatic conditions. |
The range of pavement temperatures at any one site is not adequately covered. For example, there is no test method for asphalt binder stiffness at low temperatures to control thermal cracking. | The entire range of pavement temperatures experienced at a particular site is covered. |
Test methods only consider short-term asphalt binder aging (thin film oven test) although long-term aging is a significant factor in fatigue cracking and low temperature cracking. | Three critical binder ages are simulated and tested:Original asphalt binder prior to mixingwith aggregate.Aged asphalt binder after HMAproduction and construction.Long-term aged binder. |
Asphalt binders can have significantly different characteristics within the same grading category. | Grading is more precise and there is less overlap between grades. |
Modified asphalt binders are not suited for these grading systems. | Tests and specifications are intended for asphalt “binders” to include both modified and unmodified asphalt cements. |
How to read a Performance Grade?
The PG grading system is based on climate, so the grade notation consists of two portions: high and low pavement service temperature. The major concern for high-temperature performance is rutting, which typically takes time to cumulate, therefore an average of 7-day maximum pavement temperature is used for describing the high-temperature climate. On the low-temperature side, thermal cracking can happen during the one really cold night; therefore the minimum pavement temperature is used for describing the low-temperature climate. For both high and low-temperature grades, PG grades are graded in a 6°C increment. The average 7-day maximum pavement temperature typically ranged from 46 to 82°C, and minimum pavement temperature typically ranged from −46°C to −10°C.
A binder identified as PG 64-10 must meet performance criteria at an average 7-day maximum pavement temperature of 64°C and also at a minimum pavement temperature of −10°C. Please note that maximum pavement temperature is typically higher than the air temperature by about 20°C since the dark color pavement absorbs the heat and retains it. The maximum pavement temperature is typically measured at about 1 inch below the pavement surface. However, the minimum pavement temperature occurs on the surface of the pavement and is equal to the air temperature.
The common minimum reliability used is 98%, so that means when the PG 64-10 binder is selected, the asphalt binder in the AC pavement should perform satisfactorily under normal traffic condition at the location where the extreme pavement temperature is within the range of −10°C and 64°C throughout its service life with a minimum 98% confidence level. Where the traffic condition is not typical, such as the really heavy traffic like an interstate highway, or slow traffic such as bus stop or intersection area, one or two grades stiffer asphalt binder may be used to help prevent the rutting problem.
Polymer modified binders are used wherever extra performance and durability are desired. Improvement in resistance to rutting, thermal cracking, fatigue damage, stripping, and temperature susceptibility have led polymer modified binders to be substituted for asphalt in many paving and maintenance applications. Especially when good rutting resistance for high temperature and good thermal cracking resistance for low temperatures are concurrently required in the same application, the polymer modification is generally required.
rule of thumb to differentiate the polymer modified binder from unmodified binder is to add both low and high-temperature grades together, if the sum is greater than 90, it is likely to be a polymer modified binder. For example, a Performance Grade bitumen 76-22 is likely to be a polymer modified binder since the sum is 98, while a Performance Grade Bitumen 64-10 is likely to be unmodified since the sum is 74.
PG Bitumen – Unmodified CHARACTERISTICS
PG 46-34 | PG 46-28 | PG 52-28 | PG 58-28 | PG 58-22 | PG 64-22 | AASHTO Method | |
---|---|---|---|---|---|---|---|
Original Binder | |||||||
Flash Point, COC,°C | 230 | T 48 | |||||
Flash Point, P-M, °C | NS | ≥ 204 | ASTM D93 | ||||
Rotational Viscosity @ 135°C, Pa·s | 3.00 | T 316 | |||||
Dynamic Shear @ Grade Temperature,°C | 46 | 46 | 52 | 58 | 58 | 64 | T 315 |
G*/sin @ 10 rad/sec, kPa | ≥ 1.00 | ||||||
RTFOT Residue | |||||||
Mass Loss, % | ≤ 1.00 | T 240 | |||||
Dynamic Shear @ Grade Temperature,°C | 46 | 46 | 52 | 58 | 58 | 64 | T 315 |
G*/sin @ 10 rad/sec, kPa | 2.20 | ||||||
PAV Residue (Aging Temperature, °C) | 90 | 100 | R 28 | ||||
Dynamic Shear @ Grade Temperature,°C | 10 | 13 | 16 | 19 | 22 | 25 | T 315 |
G*/sin @ 10 rad/sec, kPa | 5000 | ||||||
Creep Stiffness | -24 | -18 | -18 | -18 | -12 | -12 | |
S, Mpa | ≤ 300 | T 313 | |||||
m-value | ≥ 0.30 | T 313 |
Viscosity Grade Bitumen
Viscosity Grade Bitumen Description
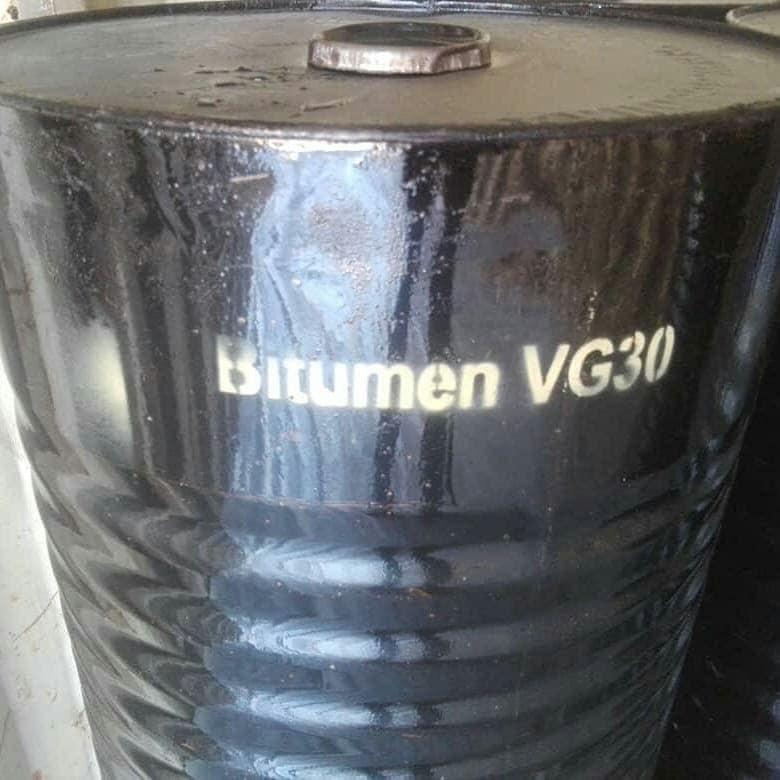
Traditionally, paving bitumen have been specified in terms of their penetration, but the measurement of viscosity provides a more accurate method of specifying binder consistency and a more effective method of determining the temperature susceptibility of the bitumen. American Association of State Highway Officials (AASHTO) has two series of viscosity grade bitumen. One is denoted AC (asphalt cement), followed by a number indicating the viscosity in hundreds of poises at 60 C. The second series is denoted AR (aged residue) followed by a number indicating the viscosity in poises (not hundreds of poises) at 60 C after the bitumen has been aged.
In the early 1960s, an improved asphalt grading system was developed that incorporated a rational scientific viscosity test. This scientific test replaced the empirical penetration test as the key asphalt binder characterization. The viscosity grading system gave excellent performance results in the US for over twenty years. The viscosity grading system is more rational than the penetration grading system. Viscosity is defined as the inverse of fluidity. Viscosity thus defines the fluid property of the bituminous material. Viscosity is the general term for consistency and it is a measure of resistance to flow. Many researchers believe that grading of bitumen should be by an absolute viscosity in instead of the conventional penetration units. Viscosity grading is based on a fundamental, scientific viscosity test, which is conducted at 60˚C (near the maximum pavement temperature during summer) and its measurement unit is poise. The test equipment for measuring viscosity both at 60˚C and 135˚C.
Viscosity grading can be done on original (as-supplied) asphalt binder samples (called AC grading) or aged residue samples (called AR grading). The AC grading is based on absolute viscosity at 60 °C in units of 100 poises. Six asphalt cement viscosity grades were established as AC-2.5 (softest), AC-5, AC-10, AC-20, AC-30, AC-40 (hardest). AC-2.5 means asphalt cement with a target viscosity of 250 poises at 60˚C (250 has been abbreviated to 2.5). Similarly, AC-5, AC-10, AC-20, AC-30, and AC-40 mean asphalt cement with target viscosity of 500, 1000, 2000, 3000, and 4000 poises, respectively. Low viscosity grades AC-2.5 and AC-5 are used in cold climate while high viscosity grades AC-10 to AC-40 are generally suitable for the hot climate.
With AC grading, the asphalt binder is characterized by the properties it possesses before it undergoes the HMA manufacturing process. The AR grading system is an attempt to simulate asphalt binder properties after it undergoes a typical HMA manufacturing process and thus, it should be more representative of how asphalt binder behaves in HMA pavements. Table 1 lists key advantages and disadvantages of the viscosity grading system.
Viscosity grade bitumen have a thermoplastic property which causes the material to soften at high temperatures and to harden at lower temperatures. This unique temperature/ viscosity relationship is important when determining the performance parameters such as the adhesion, rheology, durability and application temperatures of bitumen. In the Viscosity Graded Bitumen specifications, further special emphasizes is placed on the Bitumen ductility.
Viscosity grading can be done on original (as-supplied) asphalt binder samples (called AC grading) or aged residue samples (called AR grading). The AR viscosity test is based on the viscosity of aged residue from the rolling thin film oven test. With AC grading, the asphalt binder is characterized by the properties it possesses before it undergoes the HMA manufacturing process. The AR grading system is an attempt to simulate asphalt binder properties after it undergoes a typical HMA manufacturing process and thus, it should be more representative of how asphalt binder behaves in HMA pavements. Table 1 lists key advantages and disadvantages of the viscosity grading system.
Advantages and Disadvantages of Viscosity Grading as stated below
Advantages | Disadvantages |
---|---|
Unlike penetration depth, viscosity is a fundamental engineering parameter. | The principal grading (done at 25°C (77°F)) may not accurately reflect low-temperature asphalt binder rheology. |
Test temperatures correlate well with:25°C (77°F) – average pavement temp.60°C (140°F) – high pavement temp.135°C (275°F) – HMA mixing temp. | When using the AC grading system, thin film oven test residue viscosities can vary greatly with the same AC grade. Therefore, although asphalt binders are of the same AC grade they may behave differently after construction. |
Temperature susceptibility (the change in asphalt binder rheology with temperature) can be somewhat determined because viscosity is measured at three different temperatures (penetration only is measured at 25°C (77°F)). | The testing is more expensive and takes longer than the penetration test |
Testing equipment and standards are widely available. |
Standard | Grades Minimum of Absolute | Viscosity, Poise@ 600°C | Approximate penetration grade |
---|---|---|---|
IS73:2013 | VG 10 | 800 | 80-100 |
IS73:2013 | VG 20 | 1600 | – |
IS73:2013 | VG 30 | 2400 | 60-70 |
IS73:2013 | VG 40 | 3200 | 30-40/40-50 |
Viscosity Grade Bitumen Specification (ASTM D3381-09)
Property | Units | AC-10 | AC-20 | AC-30 | AC-40 | Test Methods |
---|---|---|---|---|---|---|
Viscosity, 140°F (60°C) | P | 1000±200 | 2000±400 | 3000±600 | 4000±800 | ASTM D-2171 |
Viscosity, 275°F (135°C), Min | cSt | 150 | 210 | 250 | 300 | ASTM D-2171 |
Penetration, 77°F (25°C), 100g, 5sec, Min | 0.1MM | 70 | 40 | 30 | 20 | ASTM D-5 |
Flash point, Cleveland open cup, Min | °C | 219 | 232 | 232 | 232 | ASTM D-92 |
Solubility in trichloroethylene, Min | %Wt | 99 | 99 | 99 | 99 | ASTM D-2042 |
Tests on residue from thin-film oven test: | ||||||
– Viscosity, 140°F (60°C), Max | P | 5,000 | 10,000 | 15,000 | 20,000 | ASTM D-2171 |
– Ductility, 77°F (25°C), 5cm/min, Min | CM | 50 | 20 | 15 | 10 | ASTM D-113 |
Viscosity Grade Bitumen Specification (IS 73:2013)
Property | Units | VG-10 | VG-20 | VG-30 | VG-40 | Test Methods |
---|---|---|---|---|---|---|
Penetration at 25°C, 100g, 5sec, Min | 0.1MM | 80 | 60 | 45 | 35 | IS 1203 |
Absolute viscosity at 60°C | P | 800-1200 | 1600-2400 | 2400-3600 | 3200-4800 | IS 1206 (Part 2) |
Kinematic viscosity at 135°C, Min | cSt | 250 | 300 | 350 | 400 | IS 1206 (Part 3) |
Flash point (Cleveland open cup), Min | °C | 220 | 220 | 220 | 220 | IS 1448 [P : 69] |
Solubility in trichloroethylene, Min | %Wt | 99 | 99 | 99 | 99 | IS 1216 |
Softening point (R&B), Min | °C | 40 | 45 | 47 | 50 | IS 1205 |
Tests on residue from thin film oven test: | ||||||
– Viscosity ratio at 60°C, Max | 4 | 4 | 4 | 4 | IS 1206 (Part 2) | |
– Ductility at 25°C, Min | CM | 75 | 50 | 40 | 25 | IS 1208 |
Penetration Grade Bitumen
Penetration Grade Bitumen Description
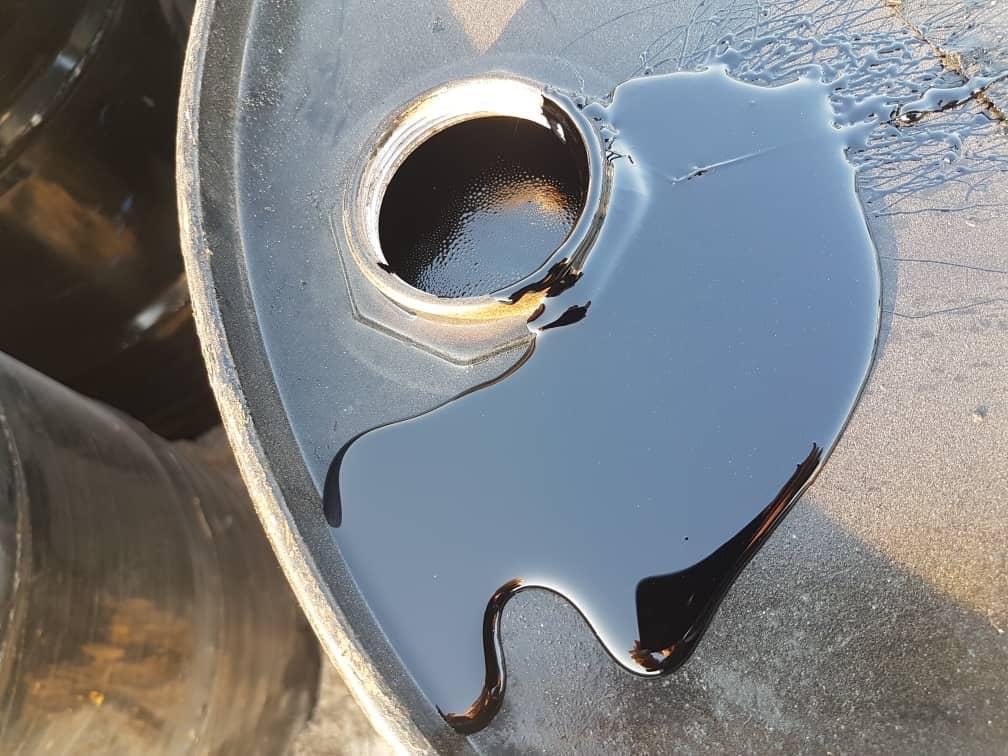
Pentration / Paving Grade Bitumen is Bitumen classified using the penetration property. Penetration grading’s basic assumption is that the less viscous the asphalt, the deeper the needle will penetrate. Bitumen which is produced during the process of oxidation of vacuum bottom (the Bitumen production feedstock that derives from distillation tower residue in vacuum oil refineries) at bitumen production unit in a manner that its penetration point (kind of test to indicate the hardness of bitumen) in specified group is classified in different grade of Bitumen.
The penetration grading system was developed in the early 1900s to characterize the consistency of semi-solid asphalts. Penetration grading quantifies the following asphalt concrete characteristics:
Penetration Grade Bitumen or Paving Bitumen is commonly used in road surfacing, and some industrial applications. Additional processing yields other grades of bitumen products and their application.
Advantages of Penetration / Paving Grade bitumen
The test is done at 25° C (77° F), which is reasonably close to a typical pavement average temperature.
May also provide a better correlation with low-temperature asphalt binder properties than the viscosity test, which is performed at 60° C (140° F).
Temperature susceptibility (the change in asphalt binder rheology with temperature) can be determined by conducting the test at temperatures other than 25° C (77° F).
The test is quick and inexpensive. Therefore, it can easily be used in the field.
Advantages | Disadvantages |
---|---|
The test is done at 25° C (77° F), which is reasonably close to a typical pavement average temperature. | The test is empirical and does not measure any fundamental engineering parameter such as viscosity. |
May also provide a better correlation with low-temperature asphalt binder properties than the viscosity test, which is performed at 60° C (140° F). | Shear rate is variable and high during the test. Since asphalt binders typically behave as a non-Newtonian fluid at 25° C (77° F), this will affect test results. |
Temperature susceptibility (the change in asphalt binder rheology with temperature) can be determined by conducting the test at temperatures other than 25° C (77° F). | Temperature susceptibility (the change in asphalt binder rheology with temperature) cannot be determined by a single test at 25° C (77° F). |
The test is quick and inexpensive. Therefore, it can easily be used in the field. | The test does not provide information with which to establish mixing and compaction temperatures. |
Penetration Grade Bitumen Specification (AASHTO M 20 and ASTM D 946)
Units | 40/50 | 60/70 | 80/100 | 100/120 | Test Methods | |
---|---|---|---|---|---|---|
Specific Gravity @25°C | – | 1.01-1.06 | 1.01-1.06 | 1.01-1.05 | 1.01-1.04 | ASTM D-70 |
Penetration @25°C, 100gm, 5sec | 0.1MM | 40-50 | 60-70 | 80-100 | 100-120 | ASTM D-5 |
Softening Point, Ring & Ball | °C | 52-60 | 49-56 | 45-52 | 42-49 | ASTM D-36 |
Ductility @25°C, after TFOT, Min | CM | 100 | 100 | 100 | 100 | ASTM D-113 |
Loss on Heating, Max | %Wt | 0.2 | 0.2 | 0.5 | 0.5 | ASTM D-6 |
Drop in Penetration after Heating, Max | % | 20.0 | 20.0 | 20.0 | 20.0 | ASTM D-6 & D-5 |
Flash Point Cleveland open cup, Min | °C | 250.0 | 250.0 | 232.0 | 250.0 | ASTM D-92 |
Solubility in CS2, Min | %Wt | 99.5 | 99.5 | 99.5 | 99.5 | ASTM D-4 |
Organic Matter Insoluble in CS2, Max | %Wt | 0.5 | 0.5 | 0.5 | 0.5 | ASTM D-4 |
Sport Test | – | Negative | Negative | Negative | Negative | *A.A.S.H.O.T.102 |
Bitumen Specification European Standard (BS EN 12591)
Units | 35-50 | 40-60 | 50-70 | 70-100 | 100-150 | Test Methods | |
---|---|---|---|---|---|---|---|
Penetration @25°C, 100gm, 5sec | 0.1MM | 35-50 | 40-60 | 50-70 | 70-100 | 100-150 | EN 1426 |
Softening Point, Ring & Ball | °C | 50-58 | 48-56 | 46-54 | 43-51 | 39-47 | EN 1427 |
Resistace to Hardening@163°C | |||||||
– Change in mass, Max | %Wt | 0.5 | 0.5 | 0.5 | 0.8 | 0.8 | EN 12607-1 |
– Retained Penetration, Min | 0.1MM | 53 | 50 | 50 | 46 | 43 | |
– Softening point after hardinging, Min | °C | 52 | 49 | 48 | 45 | 41 | |
Other Properties | |||||||
Flash Point Cleveland open cup, Min | °C | 240 | 230 | 230 | 230 | 230 | EN ISO 2592 |
Solubility in CS2, Min | %Wt | 99.0 | 99.0 | 99.0 | 99.0 | 99.0 | EN 12592 |
Kinematic Viscocity @135°C, Min | mm2/S | 370 | 325 | 295 | 230 | 175 | EN 12595 |
Safety information
Bitumen have been usually flammable and may be kept away from fire or flame.
Carbon dioxide should be used as a fire suppressant.
Engineers or workers who work with bitumen ought to use leather gloves, safety eyeglasses and proper clothes and boots when they are operating with hot bitumen.
The temperature of hot bitumen is around 300 F and it’ll result in severe skin burns and eye injury.
HJ Oil Group supplies all Penetration Graded Bitumen Grades in correspondence to ASTM D946-09 and EN 12591-2009.
ASTM D946-09 Grades:
Bitumen 10/20
Bitumen 30/40
Bitumen 40/50
Bitumen 60/70
Bitumen 85/100
Bitumen 120/150
Bitumen 200/300
EN 12591-2009 Grades:
Bitumen 20/30
Bitumen Penetration Grade 30/45
Bitumen Penetration Grade 35/50
Bitumen Penetration Grade 40/60
Bitumen Penetration Grade 50/70
Bitumen Penetration Grade 70/100
Bitumen Penetration Grade 100/150
Bitumen Penetration Grade 160/220