Polyethylene Wax
Description of Polyethylene Wax
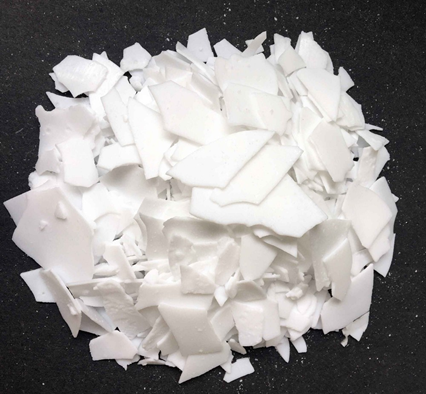
Polyethylene wax is derived from ethylene through a process called polymerization. Manufacturers alter the polymerization process to get a product with desired qualities. However, certain basic properties of the material are common for all PE wax.
Polyethylene Wax, also known as PE Wax, is an ultra-low molecular weight PE. PE wax helps granule produce by decrease the softening point of the system. PE wax is a very good external lubricant for PVC. When PE wax use in PVC application, the final produce face has been shine. Polyethylene wax using decreases the friction so increase the extrusion capacity. PE wax using doesn’t change the product color because PE wax has got
good oxidation resistance.
Uses of Polyethylene Wax
The wax finds application in a wide range of industries because of its desirable physical and chemical properties. As the material can have a broad range of melt points, densities and other properties, it is understandable why it is used so extensively.
Polyethylene waxes have very unique polymer properties that make them useful in many applications. The major functions of PE wax in many formulations are to either provide lubrication and/or provide physical modification of a formula by changing viscosity and / or melt point. Polyethylene wax increase inorganic and organic pigment dispersion in
matrix polymer during masterbatch processing. Also, PE wax helps granule produce by decrease softening point of system. Polyethylene wax is very good external lubricant for PVC. When PE wax use in PVC application, final produce face has been shine.
Polyethylene wax using decrease the friction so increase the extrusion capacity. PE wax using doesn’t change the product color because PE wax has got good oxidation resistance. PE wax doesn’t bad effect product’s heat and light stability because pe wax doesn’t include catalizors remnant.
Polyethylene wax increase last product’s light stability. PE wax hasn’t got toxic materials so PE wax can be use food packaging applications. PE wax use hot melt application.
- High softening point
- High melting point
- Excellent thermal stability
- High chemical resistance
- Highly compatible with wax varieties
- Perfect lubrication
- Perfect head resistance
Packing of PE Wax
PE Wax packed in 25 KG PP bag, 1mt Jumbo bag. Each 20-foot container takes 20 Jumbo Bags.
Specification of PE-Wax
Test | Results |
Drop Melting Point | 90 – 95℃ |
Melting Point | 100 – 110℃ |
Flash Point | 135℃ |
Density@ 20℃ | 0.9 ± 0.02 KG/m3 |
Oil Content | 0.5 – 1 % |
Viscosity@ 140℃ | 28.5 – 33.4 c.st |
Moisture | 1.1 % |
Penetration@ 25℃ | 0.02 – 0.05 mm |
Appearance | White Flake (Super Dry) |
White Spirit
Description of White Spirit

White spirit also known as: solvent naphtha, mineral spirit, varsol, mineral turpentine.
White spirit is a specialty refined product in the naphtha boiling range. It has a variety of uses including as an extraction solvent, a cleaner (paint thinner), or a degreaser. It is a common solvent in paints, lacquers, varnishes, aerosols, and asphalts.
The word “mineral” in “mineral spirits” or “mineral turpentine” is meant to distinguish it from distilled spirit (distilled directly from fermented grains and fruit) or from true turpentine (distilled tree resin).
Application of White Spirit
- Mineral spirits is a very powerful degreasing and cleansing agent for automobile and machinery part cleaning. The spirit eats away at oil and chemical grease and washes the part clean.
- Such spirits are even used to wash away dirt and grime from metallic objects and tools. Even dried paint, which accumulates on metal and thickens, can be dissolved and then washed off, on applying mineral spirits. This helps preserve the look and quality of the object, as opposed to scratching off the paint.
- They can be used as a solvent to erase mistakes made while painting.
- Wooden furniture which has been coated with a layer of lacquer, shellac or varnish, can be cleaned and polished with a small amount of mineral spirits. But first a small area of the furniture should be tested before complete use.
- It can be used to clean paint brushes, especially those used in heavy oils and paints.
- If sticky tape and price tags on glassware need to be removed, then dip a small ball of cotton in some mineral spirit and wipe off the sticker. Then rinse away the spirit.
- You can use mineral spirits on linoleum tiles to get rid of skid marks and scratches.
- Use mineral spirits to dissolve gum and other sticky resins, that are stuck to carpets or clothing.
- When combined with cutting oil, they are used as a lubricant for cutting threads.
Packing
White spirit packed in new or used 210 kg drums, iso tank, and IBC tank. Each 20-foot container takes 80 drums.
Specification
CHARACTERISTICS | UNITS | RESULT | TEST METHOD |
Density | Kg/m³ | 0.740 min | ASTM D1298 |
I.B.P | °C | Min 60 | ASTM D86 |
F.B.P | °C | Max 200 | ASTM D86 |
Pour Point | °C | -30 | ASTM D93A |
Color Say Bolt | — | 30 | ASTM D156 |
Flash Point | °C | 42 min | ASTM D56 |
Sulphur Total | ppm | 0.2 max | ASTM D4294 |
Neutrality | — | Pass | ASTM BS.245 |
Acidity of Residue | — | Pass | ASTM D1093 |
Rubber Process Oil
Rubber Process Oil Description
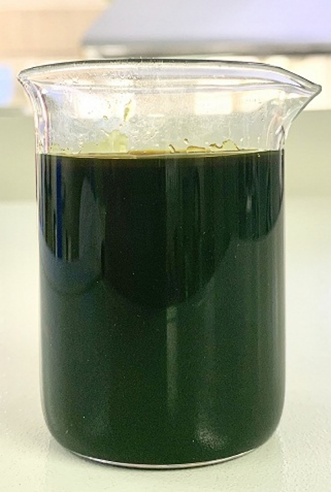
Rubber Process oil is produced by Crude oil distillation process obtained from the composition and chemical interactions and isolation material extracted called Raffinate.
The primary characteristics is the presence of the double bonded mix ring carbon structure. Aromatic extracts procured from refineries are suitably blended to meet stringent specifications with different Viscosity.
Heavy RPO is also an aromatic process oil with higher viscosity and is specifically developed for use as an extender oil in the manufacture of polystyrene butadiene rubber. This aromatic type of rubber process oil is dark in color and has good solvency. It is compatible with most rubber polymers.
Rubber process oil, both synthetic and natural is commercially used to produce products from rubber bands to a toy to the giant tires for various vehicles including aircraft. Rubber Process Oils are used during the mixing of rubber compounds.
Rubber process oil is an oil composition which has a kinematic viscosity at 100 °C of from 32 to 50 CST and which contains less than 3%. Polynuclear aromatic compounds are employed as a process oil for rubber compounds, especially aromatic rubbers.
Light Rubber Process Oil
light / Low viscosity Aromatic process oil product Is fully rich aromatic RPO By-Product from Solvent Extracting Process to Modify Physical Properties of the Vulcanization and to reduce the Cost of the Finished Product. This Product Has Good Elastomeric Compatibility And Low Volatility. Light Aromatic Process Oil Well-Known According To Its Viscosity Which Meet ASTM standards and ISO 3104 (American Society For Testing And Materials) Standard Test Method For Kinematic Viscosity Of Transparent And Opaque Liquids (Calculation Of Dynamic Viscosity) .
Heavy Rubber Process Oil
heavy / high Aromatic Process Oil Product Is Fully Rich Aromatic RPO By-Product From Solvent Extracting Process To Modify Physical Properties Of The Vulcanization And To Reduce The Cost Of The Finished Product. This Product Has Good Elastomeric Compatibility And Low Volatility. heavy Aromatic Process Oil Well-Known According To Its Viscosity Which Meet ASTM standards and ISO 3104 (American Society For Testing And Materials) Standard Test Method For Kinematic Viscosity Of Transparent And Opaque Liquids (Calculation Of Dynamic Viscosity).
Uses of RPO
It is compatible with most rubber polymers and suitable for use in the manufacture of automobile rubber tires, belting, battery case etc. where color is not an important parameter. Heavy RPO was specially developed for use in SBS rubber.
Automobile Tires
Rubber shock absorbers
Footwear
Industrial Hoses
Wire and cable coverings,
Flooring materials and carrier fluid
The solvent in the manufacture of adhesives
Sealants
Polishes and carbon black
Advantages of RPO
Good abrasion resistance
Good low temperature flexibility
Low amounts of waste tires in the process
Good resistance to reversion
According to with international standards (EU 2005/69/EC)
Save fuel and energy consumption
Extend tires life time
It is used by tire manufacturers who make tires for exporting to European Union.
Packing of RPO
packed in new or used 210 kg drums, iso tank, flexitanks, and IBC tank. Each 20-foot container takes 80 drums.
Specification
Heavy RPO
NO | Characteristic | Value | Test method |
1 | Flash point | 230 | ASTM D-92 |
2 | Kinematic viscosity @ 100 °C | 30-40 | ASTM D-7042 |
3 | Aniline point, ˚C | Max 45 | ASTM D-611 |
4 | Pour point, ˚C | Max +36 | ASTM D-97 |
5 | VGC (typical) | 0.96 | ASTM D-2501 |
6 | Density at 15.6 °C Kg/m3 | 1010 | ASTM D-4052 |
Light RPO
NO | Characteristic | Value | Test method |
1 | Flash point | 200-230 | ASTM D-93 |
2 | Kinematic viscosity @ 100 °C | 20-35 | ASTM D-445 |
3 | Aniline point, ˚C | ASTM D-611 | |
4 | Density@15°C | 1.01 | ASTM D-1298 |
5 | Refractive Index | 1.55 | ASTM D-1218 |
6 | Oil Type | Aromatic |
Caustic Soda
Caustic Soda Definition

Sodium hydroxide, also known as lye and Caustic Soda is an inorganic compound with the formula NaOH. It is a white solid ionic compound consisting of sodium cations Na+ and hydroxide anions OH−. Sodium hydroxide is a highly caustic base and alkali that decomposes proteins at ordinary ambient temperatures and may cause severe chemical burns. It is highly soluble in water, and readily absorbs moisture and carbon dioxide from the air. It forms a series of hydrates NaOH·nH2O. The monohydrate NaOH·H2O crystallizes from water solutions between 12.3 and 61.8 °C. The commercially available “sodium hydroxide” is often this monohydrate, and published data may refer to it instead of the anhydrous compound. As one of the simplest hydroxides, it is frequently utilized alongside neutral water and acidic hydrochloric acid to demonstrate the pH scale to chemistry students.
NaOH or Sodium Hydroxide or Caustic Soda Or lye are thin white sheets that are moisture absorbent and soluble in water. It is derived from the evaporation of liquid caustic soda, which is itself produced through membrane technology.
Sodium hydroxide or Caustic Soda with NaOH chemical formula, a solid white solid with a melting temperature of 2°C and a density of 0.5 Perk profits can easily absorb moisture from the air and, therefore, have to be protected during transportation.
Chemical formula: NaOH
Analysis: 98±1 %
Scientific name: Sodium hydroxide
Industrial Name: caustic soda, lye
Caustic Soda Application
1. Used in the manufacture of pulp and paper, textiles, drinking water, soaps and detergents.
2. Used in as a drain cleaner.
3. Used in the paper industry.
4. Used in the manufacture of sodium salts and detergents.
5. Used for pH regulation.
6. Used in the Bayer process of Aluminum production.
7. Used in many scenarios where it is desirable to increase the alkalinity of a mixture, or to neutralize acids.
8. Used as an additive in drilling mud to increase alkalinity in bentonite mud systems.
9. Poor quality crude oil can be treated with sodium hydroxide to remove sulfurous impurities in a process known as caustic washing.
10. Widely used in pulping of wood for making paper or regenerated fibers.
11. Used to digest tissues, as in a process that was used with farm animals at one time.
12. Acts as an agent to make the solution alkaline, which aluminum can dissolve in.
13. Traditionally used in soap making.
14. Used as a catalyst for the transesterification of methanol and triglycerides.
15. washing or chemical peeling of fruits and vegetables, chocolate and cocoa processing, caramel coloring production, poultry scalding, soft drink processing, and thickening ice cream.
Characteristics
1. It is a white solid which has a melting point of 591K
2. It is a stable compound.
3. NaOH is bitter in taste and has a soapy feel to it.
4. It is highly soluble in water and moderately soluble in alcohol.
5. Sodium hydroxide is strongly alkaline in nature.
6. Boiling Point : 1388°C.
7. Melting Point : 318°C.
8. Easily soluble in cold water, hot water.
9. Density : 2.1 g/cm³ @ 25°C.
10. Vapor Pressure : 0 mmHg (approx)
Specification
Product name | Caustic Soda Flakes 98% | |
CAS | 1310-73-2 | |
Standard | Result | |
NaOH | 98% min | 98.15% |
Na2CO3 | 0.90% max | 0.60% |
NaCl | 0.15% max | 0.06% |
Fe2O3 | 0.007% max | 0.006% |
Packing Of Caustic Soda
Packing: | 25Kg Bags, 24MT Per 20′ FCL |
Payment: | Negotiable |
Minimum Order: | 1 x 20′ FCL |
Chemical Information
Chemical Formula | NaOH |
CAS number | 1310-73-2 |
EC number | 215-185-5 |
UN number | 1823 |
Molar Mass | 40.0 g/mol |
Color | White |
Appearance | White Flakes |
Melting point | 323 °C |
Boiling point | 1390 °C |
Solubility in Water | 111 g /100 ml at 20 °C |
Synonyms: Sodium hydroxide, lye |
Gilsonite In Foundry & Construction
Gilsonite Usage In Foundry & Construction
Gilsonite is combined with coal and other ingredients as an additive in foundry sands to ensure the quality of the molded part. In sand case, by adding Gilsonite and asphalts at approximately one-third the level of sea coal the pitch had the same 900°F (482.2°C) volatiles. At this level, loss on ignition with asphalt, and Gilsonite was less than 50% of that obtained with seacoal and pitch while the Gilsonite and asphalts evolved less total gas when compared to seacoal and pitch Gilsonite had the least visible smoke generated in the laboratory tests. The lower gas evolution should reduce ventilation load on the pouring floor. The physical property relationships developed in new sand mixes were confirmed by sand using Gilsonite as an additive. Casting finish off a Gilsonite mix has been equal to Seacoal.
For High-Value Iron Castings, Gilsonite Performs Like No Other.
Foundries around the world have known for decades that – when put to the fire of molten iron – Gilsonite brings high performance to your foundry sand.
For your complex, high-value iron castings, Natural Bitumen performs like no other carbon additive. Gilsonite naturally superior properties mean high-quality castings with better finish and fewer imperfections.
Asphalt has been the subject of exhaustive study to improve characteristics for use in paving. Various properties of asphalt are manipulated to produce a product that has the appropriate wear properties, rut resistance, fatigue and low temperature cracking resistance, adhesion strength, viscosity and pour point. Rut resistance is resistance to longitudinal surface depressions in the wheel paths. Adhesion strength is the maximum adhesion strength of the joint sealant and the joint reservoir, including but not limited to, between the aggregate and the binder.
Shove resistance is resistance to permanent, longitudinal displacement of a localized area of the pavement surface caused by traffic pushing against the pavement. Heavy hydrocarbon that can be derived from, without limitation, natural asphalt (Gilsonite), shale asphalt, bottoms from a solvent deasphalting process, hard asphalt, blown asphalt, stiff refined asphalt, a flux. Asphalt is usually the base ingredient for the primer and the binder.
A primer can be asphalt, fibers (including but not limited to, mineral or cellulose), processing agent (including but not limited to, oligomeric wax, carboxilated, derivative of oligiomeric wax, or low molecular weight polyolefin), polymeric or elastomeric additive, or asphalt-derived. A primer melts to the aggregate. Asphalt binders without polymers are referred to as “neat”.
Advantages
Gilsonite Usage in Foundry & Construction
- Reduce imperfections due to the rapid reactions
- Improve sand peel from casting at shake out
- Produce smoother, cleaner casting surface
- Minimize imperfections, casting losses, scrap
- Three times as much gas generated as sea coal for better mold release
- High lustrous carbon for better finish
- Reductive atmosphere for less reaction between mold and casting for fewer imperfections
Gilsonite In Coating
Gilsonite Usage In Coating
There are few prior art coating compositions which combine the highly desired characteristics of economy, low raw material cost and compatibility with most of the raw materials used in the paint, varnish and enamel industry, and at the same time are also highly resistant to acid and alkali materials, non-corrosive toward the surface upon which they are applied, weather-resistant and of high electrical insulating value. There is, however, one composition which possesses all of these properties. This composition is one containing gilsonite as a principal constituent. For example, a Gilsonite and drying oil composition possesses all of these desirable qualities to a considerable extent.
Gilsonite is one of the purest natural bitumens available and is used in the manufacture of black varnishes, coach varnishes, black baking enamels, japaris, insulating compositions and water-proofing compositions. Two counties in the State of Utah are the sole source of commercial quantities of gilsonite in this country. Gilsonite as mined in these counties varies in its properties from one deposit to another and its properties often vary. Within a given deposit. In addition, many of the more accesssible deposits are being depleted. Consequently, the industry is faced with the problem of providing a suitable replacement material for Gilsonite in such compositions.
Gilsonite is used as insulated coating for pipes. This material is a non-toxic gum with excellent adhesiveness. Anti-corrosion coatings which are chemically inert can be produced from Gilsonite. In the wood and carpentry industry, Gilsonite is used as a solidifying agent (glue). This material is waterproof and corrosion resistant. Since Gilsonite is a very hard resin, it produces very hard products.
Gilsonite In Chemicals
Gilsonite Usage In Chemical Products
Gilsonite combines with many chemicals and materials that take advantage of its unique physical and chemical properties. Binder and coating applications in metallurgical, wood product, refractory, and other industries further demonstrate the versatility and usefulness of this remarkable material. This material is a non-toxic, non-carcinogenic and cost-effective replacement for natural rubber. Gilsonite is used as a solidifying agent in metal alloys. This material has a high carbon percentage which creates a reductive environment when added to melted steel. In shaping metals, natural bitumen is again used as a solidifying agent. Moreover, compared to other polymers, natural bitumen produces less smoke in high temperatures. Gilsonite as a solidifying and mixing material is used in steel desulfurization process.
This material has volatile ingredients which facilitate the mixing of desulfurization chemical materials such as magnesium and hydrated lime. Moreover, it increases the percentage of the carbon added to steel and as soon as oxidation happens in high temperature, it creates a reductive environment. In the manufacturing of products such as clutch plates and brake parts is used using natural bitumen which is basically as a solidifying agent. This material is also used as an additive for increasing paints shade and in some cases for reducing friction. Furthermore, natural bitumen is used as insulated coatings for pipes.
This material is a non-toxic gum with excellent adhesiveness. Anti-corrosion coatings which are chemically inert can be produced from Gilsonite. In the wood and carpentry industry, natural bitumen is used as a solidifying agent (glue). This material is waterproof and corrosion resistant. Since Gilsonite is a very hard resin, it produces very hard products. This material is also used in making paints and because of its chemical properties; it penetrates the surface of the objects which should be glued together. Moreover, a sticky material is produced from Gilsonite which is resistant against the destructing effects of ultraviolet light.
Advantages Of Using Gilsonite In Chemicals

- non-toxic
- non-carcinogenic
- cost-effective replacement for natural rubber
- high carbon percentage
- produces less smoke in high temperatures
- volatile ingredients
Gilsonite In Isolation
Gilsonite Usage In Isolation & waterproofing
By mixing Gilsonite, calcium carbonate, and bitumen with stretch enhancer oil , it is produced by an isogamy that creates composite and increases the thermal resistance of the rubble and creates a stable and homogeneous coating.
Gilsonite is extremely hydrophobe and resistant to acid and alkali and as it contains polymer hydrocarbons is considered an excellent additive to bitumen and reduces its high-temperature sensitivity and permeability, and increases its softening point and high-temperature performance as a direct consequence of increase of its brookfield viscosity, resulting in a higher quality and integrated asphalt, and is a cheap substitute of SBS modification polymers. Furthermore, gilsonite is far more easily mixed comparing with other asphalt modification polymers, increases performance grading (PG), load bearing, stability and resistance of asphalt as it contains sulfur and sulfur compounds which omits some of contractorship operations and makes it very economical. It is also used in isolation of bridges and channels due to its solubility, high isolation properties, stability, and resistance against weather conditions.
Advantages
Gilsonite Usage In Isolation Causes

- Increased shear strength
- Increased resistance to movement of layers
- Low temperature flexibility is maintained
- Reduced the tendency of the isogamy to move and use on sloping surfaces.
- Reduced fluctuations at high temperatures
- The combination of low temperature flexibility and high temperature shear strength and resistance to motion
Gilsonite In Asphalt
Gilsonite Usage In Asphalt
Gilsonite (Natural Asphalt) are natural occurring hydrocarbon substances characterized by a high softening point (above 110° C) in the class known as asphaltite. They are mined much like other minerals and sold essentially in their native state. They are fully compatible with asphalt and have long been known as asphalt hardeners and reinforcing agents. Gilsonite is currently sold all over the world as a road bitumen modifier in the form of a dry bulk solid granular powder.
Gilsonite modified road asphalt (GMA) have been particularly successful in highly stressed traffic areas. Natural bitumen, as the majority constituent, has been combined with virgin polymers such as Styrene Butadiene Styrene (SBS) and Ethylene Vinyl Acetate (EVA). GMA binders generally do not increase asphalt binder content requirement in pavement mixtures. It’s modified binders significantly extend the useful life of asphalt pavement.
Gilsonite increases the viscosity of asphalt so roadways resist deformation and fatigue, even under temperature extremes – unlike other modifications or high modulus asphalt based on RAP.
It is generally regarded that Gilsonite reduces pavements’ low temperature properties making them susceptible to thermal cracking. Gilsonite melted into hot asphalt will reduce penetration and increase viscosity of the asphalt binder. Gilsonite may also be mixed with aggregate prior to combining with the asphalt binder.
Advantages

- Improved resistance to deformation
- Further durability
- prosper economic performance of the road
- retriever for poor aggregates
- Improved resistance to stripping and fatigue
- Compensation for poor mixes design
- Tensile strength – The addition of Gilsonite significantly increased both the unconditioned and moisture-conditioned tensile strength.
Compressive strength – Gilsonite-modified binders showed significant improvement in compressive strength.
Rutting strength – Gilsonite-modified binders significantly increased projected pavement life. In all but one case, adding Gilsonite yielded a ten-fold increase.
Fatigue resistance – The projected pavement life is 1.5 to 5 times longer with the Gilsonite-modified binders.
Gilsonite In Inks
Gilsonite Usage in Inks & Paints
Inks

ER resins are “engineered resins”; the term “ER resin” or “Gilsonite ER resin”, as used herein, means a purified fraction of uintaite. These fractions are substantially enriched in maltenes or asphalteness relative to natural uintaite. Merely dissolving uintaite in a solvent in which it is soluble (i.e., a solvent that dissolves greater than about 90% of the uintaite) and filtering this solution does not produce a purified fraction of uintaite as defined herein. Such a simple filtration process does not substantially change the asphaltene to maltene ratio from that of natural uintaite.
Therefore it does not produce the asphaltene-enriched and maltene-enriched purified fraction of uintaite useful in this invention. The term “maltene”, as used herein, refers to the fraction of uintaite that is dissolved when finely ground uintaite is contacted with 20 volumes of hot heptane at 80 solution is filtered through a 0.8 micron filter. Maltene-enriched fractions of uintaite, such as ER-140 and ER-115, have a weight ratio of maltenes to asphaltenes of greater than about 6; preferably greater than about 15; most preferably these resins are substantially free of asphaltenes, i.e., less than 2 wt. % asphaltenes. Moreover these resins are also substantially free of ash. Maltene-enriched ER resins as defined herein have softening points below about 140 relative to natural uintaite; they have at least 50% fewer asphalteness than natural uintaite, preferably at least 75% fewer, and more preferably at least 90% fewer.
These maltene-enriched ER resins also have reduced mineral-derived insolubles, i.e., ash. These insolubles are below 0.1% by weight, preferably below 0.05%. The maltene-enriched fractions of uintaite useful in this invention comprise at least 60% maltenes, preferably at least 80% maltenes and most preferably at least 90% maltenes. Maltene-enriched ER resins have lower softening points than those of natural uintaite. Solution viscosity, viscosity stability and melt viscosity are also substantially improved over available grades of natural uintaite. The less soluble, high melting, asphaltene-enriched fractions are also called ER resins.
Paints

There are few prior art coating compositions which combine the highly desired characteristics of economy, low raw material cost and compatibility with most of the raw materials used in the paint, varnish and enamel in dustry, and at the same time are also highly resistant to acid and alkali materials, non-corrosive toward the surface upon which they are applied, weather-resistant and of high electrical insulating value. There is, however, one composition which possesses all of these properties. This composition is one containing gilsonite as a principal constituent. For example, a Gilsonite and drying oil composition possesses all of these desirable qualities to a considerable extent.