Cationic Bitumen Emulsion
Cationic Bitumen Emulsion Description

Cationic Bitumen Emulsion is a stable dispersion of bitumen in water in the continuous phase. The bitumen globules are positively charged due to the NH3 + group cover which is formed around bitumen droplets and provides stability for emulsion by electrostatic repulsion. These bitumen droplets have an affinity with the negatively charged aggregate, which is usually available in India. Dispersion is obtained by processing bitumen & water-based solution under controlled conditions through a colloidal mill having a high-speed rotor in the presence of scientifically selected surfactants/emulsifiers. The selection of emulsifier & its quality is significant for emulsion stability, it’s breaking & curing when applied over aggregates. The Cationic Bitumen Emulsion is chocolate brown and free-flowing at normal temperature. Once it breaks the bitumen breaks out and color changes to black. An Emulsion is said to break when the organic and the aqueous phase separate into two distinct layers i.e. the dispersion ceases to exist. Emulsions are classified as Rapid Setting-1(RS-1), Rapid Setting-2(RS-2), Medium Setting (MS), Slow Setting-1 (SS-1), and Slow Setting-1 h (SS-1h). The breaking time varies according to the designation of Emulsion although being largely dependent upon the climatic condition i.e. temperature, humidity, wind velocity, etc.
The term cationic is derived from the migration of particles of bitumen under an electric field also. The droplets migrate toward the cathode (negative electrode), and hence the emulsion is called cationic. The cationic emulsifying agent functions similarly to the anionic; the negative portion of the head floats around in the water leaving a positively charged head. This imparts a positive charge to all the droplets. Since positives repel each other, all the droplets repel each other and remain as distinct bitumen drops in suspension. A typical cationic emulsifying agent is shown below showing the orientation of the agent at the bitumen-water interface and the positive charge imparted to each drop.
Cationic Emulsion Bitumen
CRS | CMS | CSS |
CRS-1 | CMS-2 | CSS-1 |
CRS-2 | CMS-2h | CSS-1h |
Cationic type: In which the bitumen particles are positively charged and the emulsifier used is a long chain amine. These are suitable for use with siliceous aggregates like quartzite, sandstone, granite, etc.
When the emulsion is being produced the cations are adsorbed by bitumen droplets, negative ions remain in the water. The undeniably most complete field of use is represented by the rapid setting emulsions.
The choice of bitumen emulsion (i.e. whether anionic or cationic) to be used depends upon the mineral composition of aggregate used for construction. In the case of silica-rich aggregates, the surface of the aggregates is electronegatively charged. Therefore a cationic bitumen emulsion should be used. This will help better the spreading and binding of bitumen with aggregates.
Anionic Bitumen Emulsion
Anionic Bitumen Emulsion Description
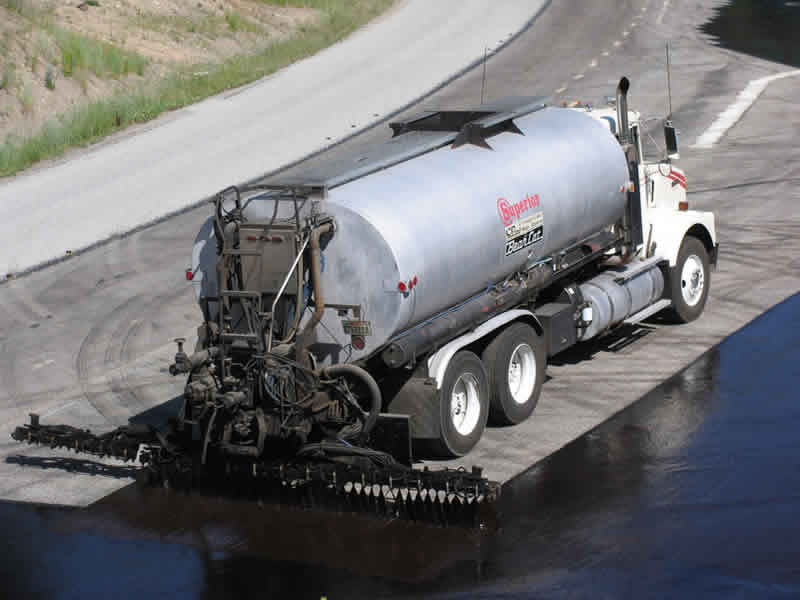
HJ Oil Group is a supplier of high-quality Anionic Bitumen Emulsion.
The preparation of bitumen emulsion is essentially the grinding of bitumen in water with a surfactant. Therefore, the emulsifier is one of the most important components of bitumen emulsions, which directly influences the quality and characteristics of the product. The emulsifier is a surfactant. By chemical nature, surfactants are divided into several types, depending on the charge of its particles. Since water bitumen emulsions are used intensively as binding and film-forming material in construction, two types of emulsifiers are used: anionic and cationic.
Chemical surface-active agents, which serve as emulsifiers, are classified by the electrochemical charge that is attained when they dissociate in a water solution. In the case of anionic emulsions, the chemical charge is negative. The chemical type and quantity of surface-active agent used in the manufacturing process govern the process in which the resulting asphalt emulsion can be used.
The term Anionic Bitumen Emulsion is derived from the migration of particles of bitumen under an electric field. The droplets migrate toward the anode (positive electrode), and hence the emulsion is called anionic. In an anionic emulsion, there are “billions and billions” of bitumen droplets with the emulsifying agent at the water bitumen interface. The tail portion of the emulsifying agent aligns itself in the bitumen while the positive portion of the head floats around in the water leaving the rest of the head negatively charged and at the surface of the droplet. This imparts a negative charge to all the droplets. Since negatives repel each other, all the droplets repel each other and remain as distinct bitumen drops in suspension. A typical anionic emulsifying agent is shown below along with a diagram showing the orientation of the agent at the bitumen-water interface and the negative charge imparted to each drop.
ANIONIC EMULSION
RS | MS | SS |
RS-1 RS-2 | MS-1 MS-2 MS-2h HFMS-1 HFMS-2 HFMS-2h HFMS-2s | SS-1 SS-1h |
The difference is that the anionic bitumen emulsion is negatively charged, while the cationic emulsions are positively charged. The choice of emulsifier used in the preparation of the emulsions determines the efficiency and reliability of the product.
For certain reasons, cationic systems have a significant advantage over anionic emulsions. Most of the fillers used in road construction have a limited amount of positively charged particles, which can attract the negatively charged particles of the anionic emulsion. Therefore, it is more difficult to create a uniform structure and ensure a high degree of adhesion with an anionic surfactant. When using anionic emulsion, bitumen should be modified by additives, while in the cationic emulsion, the emulsifier itself serves as an adhesion additive.
Unlike cationic emulsions, which readily interact with alkaline and acidic minerals, anionic emulsions are less versatile and work well only with alkaline minerals.
The amount of emulsifier applied influences emulsion breakdown rate, i.e. the time until the bitumen precipitating from the emulsion, returns to its original state.
Cutback Bitumen SC-3000
Cutback Bitumen SC-3000 Description
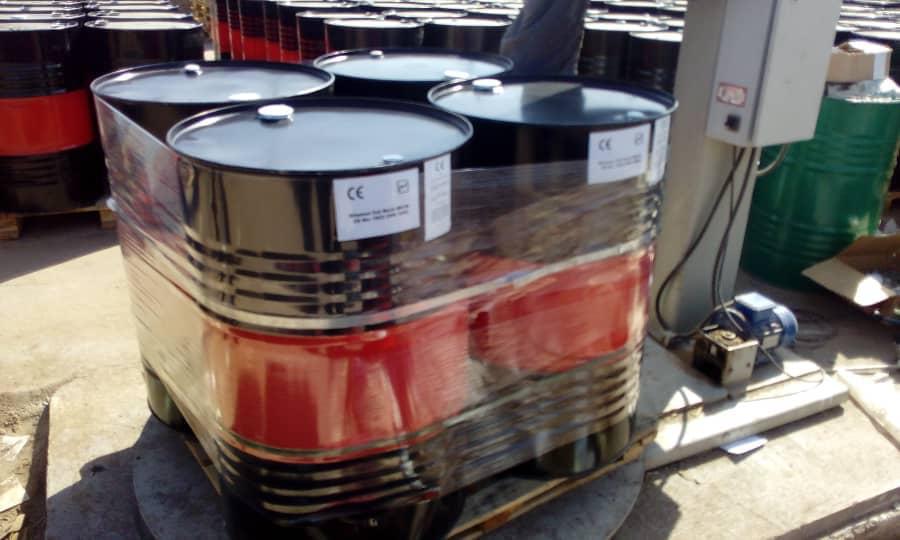
Cutback bitumen SC-3000 is an asphalt cement that has a solvent or distillate such as gasoline, diesel fuel, kerosene, or naphtha added to make the asphalt liquid at ambient temperatures and improve its ability to coat aggregates. Two letters followed by a numerical digit designate or name a cutback asphalt.
Cutback asphalt can contain between 12 and 40 percent distillate. The high demand for the distillates to be used in energy applications and ever-increasing air quality regulations have caused a steady decline in the use of cutback asphalt.
The SC liquid asphalt may be obtained by fluxing an asphalt cement with a less volatile distillate such as gas oil. The SC-70 and SC-250 grade cutback asphalts are very similar to residual refinery products that are used as heavy fuel oils such as bunker C or Number six fuel oils. These SC cutback materials, whether straight run or fluxed with a relatively non-volatile material such as gas oil, are also known as “road oils”.
Cutback Bitumen SC-3000 Applications
Current common uses are in penetrating prime coats and in producing patching or stockpile mixtures. Cutback asphalt used in mixing with aggregate will usually contain an adhesion agent to assist in the coating of the aggregate surface.
Cutback agents are used to lowering the viscosity of bitumen when it is applied as a primer to the surface of a road pavement aggregate base course or substrate. Kerosene is used as a bitumen cutback agent at different concentrations according to local conditions and requirements.
The cutback bitumen is ideal for prime coat and cold applied because of easy uses and no need for thinning and heating.
Cutback bitumen SC-3000 consist of initial incorporation of asphalt into the surface of non-asphalt based course preparatory to any superimposed treatment of construction.
The cutback asphalt SC-3000 applying to waterproof of surfaces plug capillary voids, coat, and bond loose mineral particles.
Packing of cutback bitumen SC-3000
Packing of cutback bitumen SC-3000 is in the new thick steel drum on the pallet to prevent any leak inside of container also bulk in bitutainers and tanker.
Safety of cutback Asphalt SC-3000
Refer to Safety Datasheets before use.
Transport, use, and store at the lowest temperature possible.
Eliminate all potential ignition sources during application.
Avoid breathing vapors. Avoid contact with skin.
Always wear appropriate PPE including heat protection when used hot.
DO NOT allow product or washings to enter stormwater or sewer systems.
Specification of Cutback Asphalt SC3000
We guaranty the quality of cutback SC-3000 with the arrangement of the international inspectors to check the quality and quantity of the bitumen on each shipment during the loading to vessel and controlling the production by the QC team via batch test report before shipping. RABIT guaranty the quality to meet with ASTM/EN 15322:2009.
property | specification limit | specification limit | Test method |
Min | Max | ||
Kinematic viscosity at 60°C [140°F], mm2/s | 3000 | 6000 | ASTM D2170 |
Flashpoint(Cleveland open cup), °C [°F] | 70 | — | ASTM D92 |
distillate test | |||
Total distillate to 360°C [680°F], volume % | — | 8 | ASTM D402 |
Solubility, % | 95 | — | ASTM D2024 |
Kinematic viscosity on distillation residue at 60°C [140°F], mm2/s | 2000 | 35000 | ASTM D2170 |
Asphalt residue: | |||
Residue of 100 penetration, % | 75 | — | ASTM D243 |
Ductility of 100 penetration residue at 25°C [77°F], cm | 50 | — | ASTM D113 |
Water, % | — | 0.5 | ASTM D95 |
Cutback Bitumen SC-800
Cutback Bitumen SC-800 Description

Cutback Bitumen SC-800 is an asphalt cement that has a solvent or distillate such as gasoline, diesel fuel, kerosene, or naphtha added to make the asphalt liquid at ambient temperatures and improve its ability to coat aggregates. Two letters followed by a numerical digit designate or name a cutback asphalt.
Cutback asphalt can contain between 12 and 40 percent distillate. The high demand for the distillates to be used in energy applications and ever-increasing air quality regulations have caused a steady decline in the use of cutback asphalt.
The SC liquid asphalt may be obtained by fluxing an asphalt cement with a less volatile distillate such as gas oil. The SC-70 and SC-250 grade cutback asphalts are very similar to residual refinery products that are used as heavy fuel oils such as bunker C or Number six fuel oils. These SC cutback materials, whether straight run or fluxed with a relatively non-volatile material such as gas oil, are also known as “road oils”.
Cutback Asphalt SC-800 Applications
Current common uses are in penetrating prime coats and in producing patching or stockpile mixtures. Cutback asphalt used in mixing with aggregate will usually contain an adhesion agent to assist in the coating of the aggregate surface.
Cutback agents are used to lowering the viscosity of bitumen when it is applied as a primer to the surface of a road pavement aggregate base course or substrate. Kerosene is used as a bitumen cutback agent at different concentrations according to local conditions and requirements.
The cutback bitumen is ideal for prime coat and cold applied because of easy uses and no need for thinning and heating.
Cutback bitumen SC-800 consist of initial incorporation of asphalt into the surface of non-asphalt based course preparatory to any superimposed treatment of construction.
The cutback bitumen SC-800 applying to waterproof of surfaces plug capillary voids, coat, and bond loose mineral particles.
Packing of Cutback Bitumen SC-800
This cutback bitumen bulk in the tanker and also in new steel and thick drum on the pallet to prevent all leak inside of the container.
Safety of Cutback Asphalt SC-800
Refer to Safety Datasheets before use.
Transport, use, and store at the lowest temperature possible.
Eliminate all potential ignition sources during application.
Avoid breathing vapors. Avoid contact with skin.
Always wear appropriate PPE including heat protection when used hot.
DO NOT allow product or washings to enter stormwater or sewer systems.
Specification of Cutback Asphalt SC800
We guaranty the quality of cutback SC-800 with the arrangement of the international inspectors to check the quality and quantity of the bitumen on each shipment during the loading to vessel and controlling the production by the QC team via batch test report before shipping. RABIT guaranty the quality to meet with ASTM/EN 15322:2009.
Property | Specification limit | Specification limit | Test Method |
Min | Max | ||
Kinematic viscosity at 60°C [140°F], mm2/s | 800 | 1600 | ASTM D2170 |
Flashpoint(Cleveland open cup), °C [°F] | 70 | — | ASTM D92 |
Distillate test | |||
Total distillate to 360°C [680°F], volume % | — | 15 | ASTM D402 |
Solubility, % | 95 | — | ASTM D2024 |
Kinematic viscosity on distillation residue at 60°C [140°F], mm2/s | 1000 | 16000 | ASTM D2170 |
Asphalt residue: | |||
Residue of 100 penetration, % | 60 | — | ASTM D243 |
Ductility of 100 penetration residue at 25°C [77°F], cm | 50 | — | ASTM D113 |
Water, % | — | 0.5 | ASTM D95 |
Cutback Bitumen SC-250
Cutback Bitumen SC-250 Description
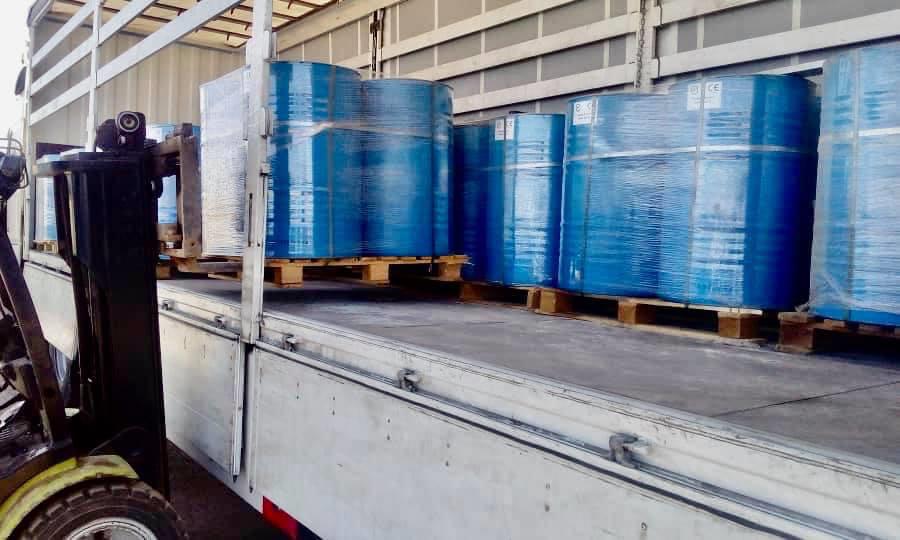
Cutback Bitumen SC-250 is an asphalt cement that has a solvent or distillate such as gasoline, diesel fuel, kerosene, or naphtha added to make the asphalt liquid at ambient temperatures and improve its ability to coat aggregates. Two letters followed by a numerical digit designate or name a cutback asphalt.
Cutback asphalt can contain between 12 and 40 percent distillate. The high demand for the distillates to be used in energy applications and ever-increasing air quality regulations have caused a steady decline in the use of cutback asphalt.
The SC liquid asphalt may be obtained by fluxing an asphalt cement with a less volatile distillate such as gas oil. The SC-70 and SC-250 grade cutback asphalts are very similar to residual refinery products that are used as heavy fuel oils such as bunker C or Number six fuel oils. These SC cutback materials, whether straight run or fluxed with a relatively non-volatile material such as gas oil, are also known as “road oils”.
Cutback Bitumen SC-250 Uses
Current common uses are in penetrating prime coats and in producing patching or stockpile mixtures. Cutback asphalt used in mixing with aggregate will usually contain an adhesion agent to assist in the coating of the aggregate surface.
Cutback agents are used to lowering the viscosity of bitumen when it is applied as a primer to the surface of a road pavement aggregate base course or substrate. Kerosene is used as a bitumen cutback agent at different concentrations according to local conditions and requirements.
The cutback bitumen is ideal for prime coat and cold applied because of easy uses and no need for thinning and heating.
Cutback bitumen SC-250 consist of initial incorporation of asphalt into the surface of non-asphalt based course preparatory to any superimposed treatment of construction.
The cutback asphalt SC-250 applying to waterproof of surfaces plug capillary voids, coat, and bond loose mineral particles.
Packing of Cutback Asphalt SC-250
Packing of cutback bitumen SC-250 is in the new thick steel drum on the pallet to prevent any leak inside of container also bulk in bitutainers and tanker.
Safety of Cutback Asphalt SC250
Refer to Safety Datasheets before use.
Transport, use, and store at the lowest temperature possible.
Eliminate all potential ignition sources during application.
Avoid breathing vapors. Avoid contact with skin.
Always wear appropriate PPE including heat protection when used hot.
DO NOT allow product or washings to enter stormwater or sewer systems.
Specification of Cutback Asphalt SC250
We guaranty the quality of cutback SC-250 with the arrangement of the international inspectors to check the quality and quantity of the bitumen on each shipment during the loading to vessel and controlling the production by the QC team via batch test report before shipping. RABIT guaranty the quality to meet with ASTM/EN 15322:2009.
property | specification limit | specification limit | Test method |
Min | Max | ||
Kinematic viscosity at 60°C [140°F], mm2/s | 250 | 500 | ASTM D2170 |
Flashpoint(Cleveland open cup), °C [°F] | 60 | — | ASTM D92 |
distillate test | |||
Total distillate to 360°C [680°F], volume % | — | 25 | ASTM D402 |
Solubility, % | 95 | — | ASTM D2024 |
Kinematic viscosity on distillation residue at 60°C [140°F], mm2/s | 400 | 10000 | ASTM D2170 |
Asphalt residue: | |||
Residue of 100 penetration, % | 50 | — | ASTM D243 |
Ductility of 100 penetration residue at 25°C [77°F], cm | 50 | — | ASTM D113 |
Water, % | — | 0.5 | ASTM D95 |
Cutback Bitumen SC-70
Cutback Bitumen SC-70 Description
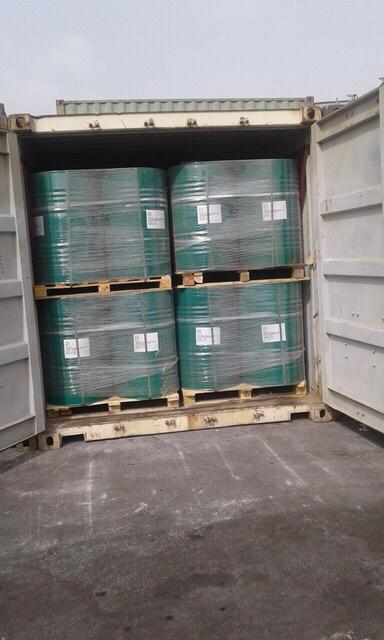
Cutback Bitumen SC-70 is an asphalt cement that has a solvent or distillate such as gasoline, diesel fuel, kerosene, or naphtha added to make the asphalt liquid at ambient temperatures and improve its ability to coat aggregates. Two letters followed by a numerical digit designate or name a cutback asphalt.
Cutback asphalt can contain between 12 and 40 percent distillate. The high demand for the distillates to be used in energy applications and ever-increasing air quality regulations have caused a steady decline in the use of cutback asphalt.
The SC liquid asphalt may be obtained by fluxing an asphalt cement with a less volatile distillate such as gas oil. The SC-70 and SC-250 grade cutback asphalts are very similar to residual refinery products that are used as heavy fuel oils such as bunker C or Number six fuel oils. These SC cutback materials, whether straight run or fluxed with a relatively non-volatile material such as gas oil, are also known as “road oils”.
Cutback Bitumen SC-70 Applications
Current common uses are in penetrating prime coats and in producing patching or stockpile mixtures. Cutback asphalt used in mixing with aggregate will usually contain an adhesion agent to assist in the coating of the aggregate surface.
Cutback agents are used to lowering the viscosity of bitumen when it is applied as a primer to the surface of a road pavement aggregate base course or substrate. Kerosene is used as a bitumen cutback agent at different concentrations according to local conditions and requirements.
The cutback bitumen is ideal for prime coat and cold applied because of easy uses and no need for thinning and heating.
Cutback bitumen SC-70 consist of initial incorporation of asphalt into the surface of non-asphalt based course preparatory to any superimposed treatment of construction.
The cutback asphalt SC-70 applying to waterproof of surfaces, plug capillary voids, coat, and bond loose mineral particles.
Packing of cutback bitumen SC-70
Packing of cutback bitumen SC-70 is in the new thick steel drum on the pallet to prevent any leak inside of container also bulk in bitutainers and tanker.
Safety of cutback asphalt SC70
Refer to Safety Datasheets before use.
Transport, use, and store at the lowest temperature possible.
Eliminate all potential ignition sources during application.
Avoid breathing vapors. Avoid contact with skin.
Always wear appropriate PPE including heat protection when used hot.
DO NOT allow product or washings to enter stormwater or sewer systems.
Specification of cutback asphalt SC70
We guaranty the quality of cutback SC-70 with the arrangement of the international inspectors to check the quality and quantity of the bitumen on each shipment during the loading to vessel and controlling the production by the QC team via batch test report before shipping. HJ Oil guaranty the quality to meet with ASTM/EN 15322:2009
property | Specification limit | Specification limit | Test method |
Min | Max | ||
Kinematic viscosity at 60°C [140°F], mm2/s | 70 | 140 | ASTM D2170 |
Flashpoint(Cleveland open cup), °C [°F] | 60 | — | ASTM D92 |
distillate test | |||
Total distillate to 360°C [680°F], volume % | — | 35 | ASTM D402 |
Solubility, % | 95 | — | ASTM D2024 |
Kinematic viscosity on distillation residue at 60°C [140°F], mm2/s | 200 | 7000 | ASTM D2170 |
Asphalt residue: | |||
Residue of 100 penetration, % | 40 | — | ASTM D243 |
Ductility of 100 penetration residue at 25°C [77°F], cm | 50 | — | ASTM D113 |
Water, % | — | 0.5 | ASTM D95 |
Cutback Bitumen MC3000
Cutback Bitumen MC3000 Description
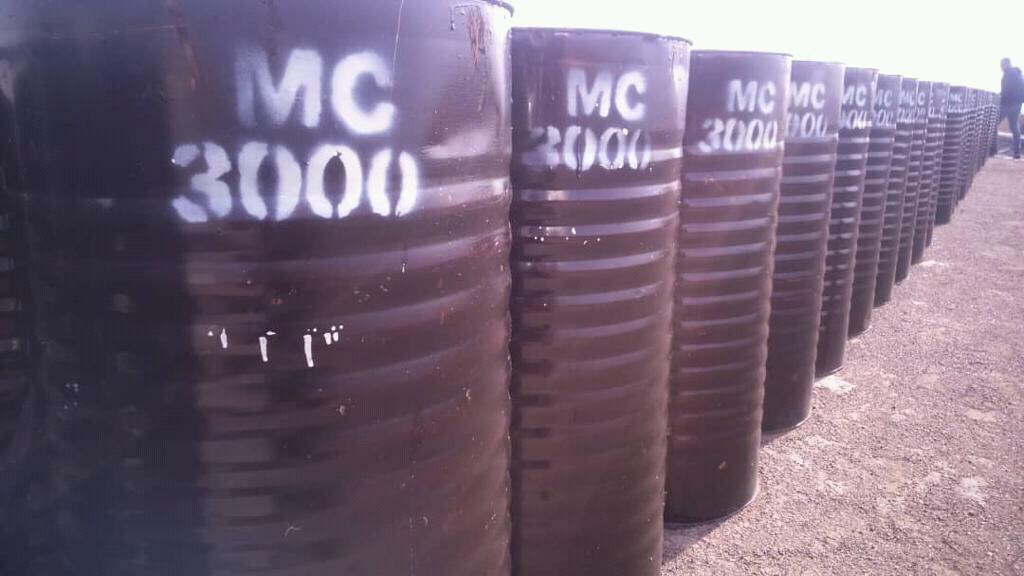
Cutback Bitumen MC3000 is a type of dissolved Bitumen. To produce this type, solvent oils such as kerosene are used in order to change bitumen into dissolved bitumen or liquid pitch, so that, during the consumption process, the solvent oil evaporates and bitumen residue to obtain the desired adhesion. In many countries, kerosene and other volatile petroleum-derived products are added as a cutter or cutback agent to bitumen to reduce (or cutback) the viscosity of the bitumen. The mixture obtained may be called cutback bitumen.
Medium curing is the most common category in cutback bitumen, among which, MC-3000 grade has the highest demand. MC-3000 is a medium curing cutback bitumen that contains 80% bitumen and has the lowest viscosity among all grades. It is black in color and is manufactured strictly as per the ASTM D 2027M-13 standard. After application, the diluent evaporates, leaving asphalt cement to perform its function. MC-3000 bitumen viscosity is between 3000-6000 CST.
Its commonly used as a Prime Coating. It is homogeneous and will not foam (as observed visually) when heated to application temperature.
MC-3000 is medium curing (MC) cut-back asphalt consisting of penetration grade asphalt cement and diluents or cutter of medium volatility. The diluents temporarily reduce the viscosity of the asphalt cement for ease of handling and application. Cutback MC-3000 use in the road maintenance industry where it is used as a prime coat of the base course prior to placing the bituminous surface course.
Cutback Bitumen MC3000 Applications
The reduction in viscosity of the bitumen aids the construction of seal coats in road pavements as the softened mixture wets the chips more easily. The cutback agent evaporates from the seal coat, the cutback agent becoming a negligible component of the seal coat a few months after application. If significant amounts of the cutback agent remain in the seal coat an unwanted long term softening effect may result
Bitumen-aggregate mixtures:
Cold-laid plant mix
- Pavement base and surfaces with dense-graded aggregate
- Patching, immediate use
Mixed-in-place (road mix):
- Pavement base and surfaces with dense-graded aggregate, sand, and sandy soil
- Patching, immediate use
Bitumen-aggregate applications:
Surface treatments
- Single surface treatment
- Multiple surface treatment
Cutback agents are used to lowering the viscosity of bitumen when it is applied as a primer to the surface of a road pavement aggregate base course or substrate. Kerosene is used as a bitumen cutback agent at different concentrations according to local conditions and requirements.
The cutback bitumen is ideal for prime coat and cold applied because of easy uses and no need for thinning and heating.
Cutback bitumen MC3000 consists of initial incorporation of asphalt into the surface of non-asphalt based course preparatory to any superimposed treatment of construction.
The cutback asphalt MC3000 applying to waterproof of surfaces plug capillary voids, coat, and bond loose mineral particles.
meanwhile, Cutback Bitumen MC3000 are used as components for road maintenance industry where it is used as a prime coat of the base course prior to placing of the bituminous surface course.
This type of Bitumen is most commonly used as an adhesive material between road foundation and asphalt coating, in the road construction industry which includes superstructure and foundation. Cutback Bitumen MC3000 is used Priming of all non-bituminous road buses, provision of temporary surfaces(deviations)
Also, Cutback Asphalt MC-3000 is suitable for primer sealing and can also be used in the manufacturing of asphalt pre-mix. Cutback bitumen is used extensively in sprayed sealing applications, particularly in colder weather where they proved improved initial stone retention due to their lower viscosity.
Other uses include roofing as a waterproofing membrane and as an adhesive to stick chippings onto a flat, horizontal roof to minimize the effects of weathering from the sun.
Recommended Spraying Temperature: 130°C – 135°C
Uses: Cutback MC 3000 containing 80% Bitumen, is commonly used for surface dressing and semi grouting (Penetration Macadam). The process of priming involves applying a low viscosity binder to a prepared but usually unbound aggregate base. It is intended to be absorbed by the top layers of the base and provide a surface that is more easily wetted by a following bituminous covering. This is applied to an underlying surface to aid with the adhesion of the following asphalt layer. Cutback Bitumen is suitable for primer sealing and can also be used in the manufacture of pre-mixed asphalt, used in patch repairs. Cutback Bitumen is used extensively in sprayed sealing applications, particularly in cooler weather where they provide improved initial stone retention due to the lower viscosity. Usually, a single application of cutback bitumen is sprayed on the primed pavement onto which aggregate is laid.
Flammable: Contains petroleum distillate. Avoid heat, flames and sources of ignition.
Prime and Tack Coating
The process of priming involves applying a low viscosity binder to a prepared but usually unbound aggregate base. It is intended to be absorbed by the top layers of the base and provide a surface more easily ‘wetted’ by a subsequent bituminous covering. The primer will be able to carry traffic for a short time (although this practice is uncommon) and help control dust. Generally, primers are applied at rates between 0.5 and 1.4 L/m2. Cutback bitumens suitable for priming are also used for tack coats, which are applied to an underlying surface to help with the adhesion of the subsequent asphalt layer. A typical application rate is between 0.2 and 0.4 L/m2.
Prime Sealing
Where temperatures are too cool for an effective priming operation, or where traffic is likely to upset a primed surface before the final seal can be sprayed, a primer seal can be used to give adequate protection of the pavement for periods of up to 6 to 12 months. Cutback bitumens suitable for primer sealing can also be used in the manufacture of pre-mix asphalt, which is used in patch repairs.
Spray Sealing
Cutback bitumens are used extensively in sprayed sealing applications, particularly in cooler weather where they provide improved initial stone retention due to their lower viscosity. Typically, a single application of the appropriate cutback bitumen is sprayed onto the primed pavement onto which aggregate is laid.
Properties of Cutback Bitumen MC3000
MC3000 is blended to a low viscosity to ensure that it penetrates the top 10mm of the base with the aid of the cutter, whilst depositing a thin film of bitumen on the surface to provide adhesion between the base coarse and the new surfacing.
Guaranty and Safety of Bitumen MC-3000
RAHA Group guarantees the quality of cutback MC3000 with the arrangement of the international inspector. By checking the quality and quantity of the bitumen on each shipment during the loading to the vessel. Also controlling the production by the QC team via batch test report before shipping.
Packing of Cutback Asphalt MC-3000
- Bulk as IBC Tank, Flexi Tank
- Reconditioned steel drums 203 lit., Net Weight: 185 ± 5 Kg
- New steel drums 203 lit., Net Weight: 185 ± 5 Kg
Specification of Bitumen MC-3000
property | Specification Limit | Specification Limit | Test method |
Min | Max | ||
Kinematic viscosity at 60°c, (cSt) | 3000 | 6000 | ASTM D2170 |
Flashpoint(tag open cup), °c | 66 | — | ASTM D3143 |
Distillation test Distillate, volume percent of total Distillate to 680°f(360°c) | |||
to 437°f(225°c) | — | — | ASTM D402 |
To 500°f(260°c) | — | 15 | |
to 600°f(316°c) | 15 | 75 | |
Residue from distillation to 680°f(360°c), percent volume by the difference | 80 | — | |
Test on Residue from distillation test | |||
Penetration 77°f(25°c) dmm | 120 | 250 | ASTM D5 |
Ductility 77°f(25°c) 5cm/min cm | 100 | — | ASTM D113 |
Solubility in trichloroethylene % | 99 | — | ASTM D2042 |
Water, percent volume | — | 0.2 | ASTM D95 |
Cutback Bitumen MC800
Cutback Bitumen MC800 Description
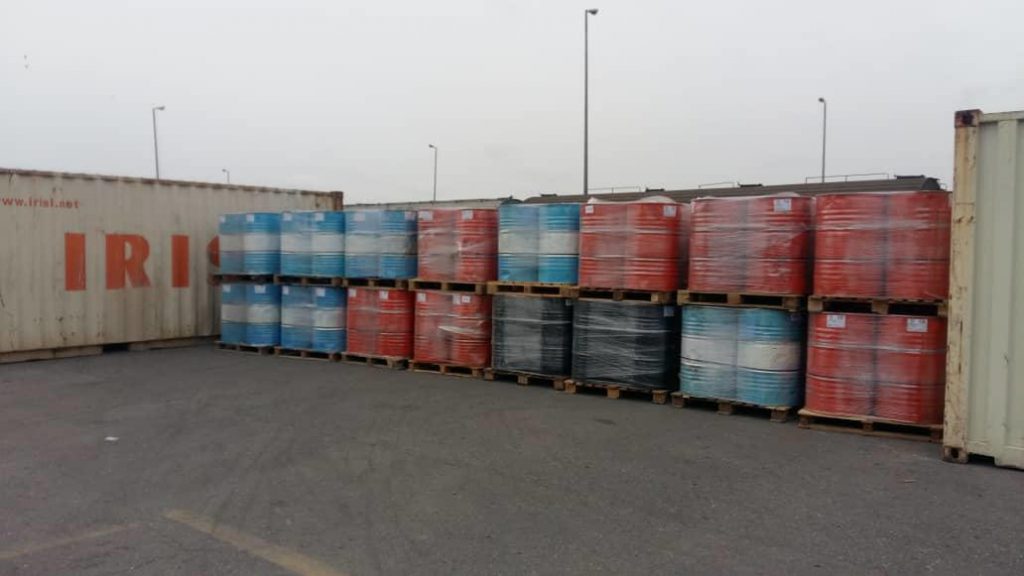
Cutback Bitumen MC800 is a type of dissolved Bitumen. To produce this type, solvent oils such as kerosene are used in order to change bitumen into dissolved bitumen or liquid pitch, so that, during the consumption process, the solvent oil evaporates and bitumen residue to obtain the desired adhesion. In many countries, kerosene and other volatile petroleum-derived products are added as a cutter or cutback agent to bitumen to reduce (or cutback) the viscosity of the bitumen. The mixture obtained may be called cutback bitumen.
Medium curing is the most common category in cutback bitumen, among which, MC-800 grade has the highest demand. MC-800 is a medium curing cutback bitumen that contains 75% bitumen and has the lowest viscosity among all grades. It is black in color and is manufactured strictly as per the ASTM D 2027M-13 standard. After application, the diluent evaporates, leaving asphalt cement to perform its function. MC–800 bitumen viscosity is between 800-1600 CST.
Its commonly used as a Prime Coating. It is homogeneous and will not foam (as observed visually) when heated to application temperature.
MC-800 is medium curing (MC) cut-back asphalt consisting of penetration grade asphalt cement and diluents or cutter of medium volatility. The diluents temporarily reduce the viscosity of the asphalt cement for ease of handling and application. Cutback MC-800use in the road maintenance industry where it is used as a prime coat of the base course prior to placing the bituminous surface course.
Cutback Bitumen MC800 Applications
The reduction in viscosity of the bitumen aids the construction of seal coats in road pavements as the softened mixture wets the chips more easily. The cutback agent evaporates from the seal coat, the cutback agent becoming a negligible component of the seal coat a few months after application. If significant amounts of the cutback agent remain in the seal coat an unwanted long term softening effect may result
Bitumen-aggregate mixtures:
Cold-laid plant mix
- Pavement base and surfaces with an open-graded aggregate
- Pavement base and surfaces with dense-graded aggregate
- Patching, immediate use
- Patching, stockpile
Mixed-in-place (road mix):
- Pavement base and surfaces with dense-graded aggregate, sand, and sandy soil
- Patching, immediate use
- Patching, stockpile
Bitumen-aggregate applications:
Surface treatments
- Single surface treatment
- Sand seal
Cutback agents are used to lowering the viscosity of bitumen when it is applied as a primer to the surface of a road pavement aggregate base course or substrate. Kerosene is used as a bitumen cutback agent at different concentrations according to local conditions and requirements.
The cutback bitumen is ideal for prime coat and cold applied because of easy uses and no need for thinning and heating.
Cutback bitumen MC800 consists of initial incorporation of asphalt into the surface of non-asphalt based course preparatory to any superimposed treatment of construction.
The cutback asphalt MC800 applying to waterproof of surfaces plug capillary voids, coat, and bond loose mineral particles.
meanwhile, Cutback Bitumen MC800 are used as components for road maintenance industry where it is used as a prime coat of the base course prior to placing of the bituminous surface course.
This type of Bitumen is most commonly used as an adhesive material between road foundation and asphalt coating, in the road construction industry which includes superstructure and foundation. Cutback Bitumen MC800 is used Priming of all non-bituminous road buses, provision of temporary surfaces(deviations)
Also, Cutback Asphalt MC-800 is suitable for primer sealing and can also be used in the manufacturing of asphalt pre-mix. Cutback bitumen is used extensively in sprayed sealing applications, particularly in colder weather where they proved improved initial stone retention due to their lower viscosity.
Other uses include roofing as a waterproofing membrane and as an adhesive to stick chippings onto a flat, horizontal roof to minimize the effects of weathering from the sun.
Application of Cutback Asphalt MC-800
Prime and Tack Coating
The process of priming involves applying a low viscosity binder to a prepared but usually unbound aggregate base. It is intended to be absorbed by the top layers of the base and provide a surface more easily ‘wetted’ by a subsequent bituminous covering. The primer will be able to carry traffic for a short time (although this practice is uncommon) and help control dust. Generally, primers are applied at rates between 0.5 and 1.4 L/m2. Cutback bitumens suitable for priming are also used for tack coats, which are applied to an underlying surface to help with the adhesion of the subsequent asphalt layer. A typical application rate is between 0.2 and 0.4 L/m2.
Prime Sealing
Where temperatures are too cool for an effective priming operation, or where traffic is likely to upset a primed surface before the final seal can be sprayed, a primer seal can be used to give adequate protection of the pavement for periods of up to 6 to 12 months. Cutback bitumens suitable for primer sealing can also be used in the manufacture of pre-mix asphalt, which is used in patch repairs.
Spray Sealing
Cutback bitumens are used extensively in sprayed sealing applications, particularly in cooler weather where they provide improved initial stone retention due to their lower viscosity. Typically, a single application of the appropriate cutback bitumen is sprayed onto the primed pavement onto which aggregate is laid.
Properties of Cutback Bitumen MC800
MC800 is blended to a low viscosity to ensure that it penetrates the top 10mm of the base with the aid of the cutter, whilst depositing a thin film of bitumen on the surface to provide adhesion between the base coarse and the new surfacing.
Guaranty and Safety of Bitumen MC-800
RAHA Group guarantees the quality of cutback MC800 with the arrangement of the international inspector. By checking the quality and quantity of the bitumen on each shipment during the loading to the vessel. Also controlling the production by the QC team via batch test report before shipping.
Packing of Cutback Asphalt MC800
- Bulk as IBC Tank, Flexi Tank
- Reconditioned steel drums 203 lit., Net Weight: 185 ± 5 Kg
- New steel drums 203 lit., Net Weight: 185 ± 5 Kg
Bitumen MC800 Specifications
Property | Specification Limit | Specification Limit | Test method |
Min | Max | ||
Kinematic viscosity at 60°c, (cSt) | 800 | 1600 | ASTM D2170 |
Flashpoint(tag open cup), °c | 66 | — | ASTM D3143 |
Distillation test Distillate, volume percent of total Distillate to 680°f(360°c) | |||
to 437°f(225°c) Residue from distillation to 680°f(360°c), percent volume by the difference | — | — | ASTM D402 |
To 500°f(260°c) | — | 40 | |
to 600°f(316°c) | 45 | 80 | |
Residue from distillation to 680°f(360°c), percent volume by the difference | 75 | — | |
Test on Residue from distillation test | |||
Penetration 77°f(25°c) dmm | 120 | 250 | ASTM D5 |
Ductility 77°f(25°c) 5cm/min cm | 100 | — | ASTM D113 |
Solubility in trichloroethylene % | 99 | — | ASTM D2042 |
Water, percent volume | — | 0.2 | ASTM D95 |
Cutback Bitumen MC250
Cutback Bitumen MC250 Description

Cutback Bitumen MC250 is a type of dissolved Bitumen. To produce this type, solvent oils such as kerosene are used in order to change bitumen into dissolved bitumen or liquid pitch, so that, during the consumption process, the solvent oil evaporates and bitumen residue to obtain the desired adhesion. In many countries, kerosene and other volatile petroleum-derived products are added as a cutter or cutback agent to bitumen to reduce (or cutback) the viscosity of the bitumen. The mixture obtained may be called cutback bitumen.
Medium curing is the most common category in cutback bitumen, among which, MC-250 grade has the highest demand. MC-250 is a medium curing cutback bitumen that contains 67% bitumen and has the lowest viscosity among all grades. It is black in color and is manufactured strictly as per the ASTM D 2027M-13 standard. After application, the diluent evaporates, leaving asphalt cement to perform its function. MC–250 bitumen viscosity is between 250-500 CST.
Its commonly used as a Prime Coating. It is homogeneous and will not foam (as observed visually) when heated to application temperature.
MC-250 is medium curing (MC) cut-back asphalt consisting of penetration grade asphalt cement and diluents or cutter of medium volatility. The diluents temporarily reduce the viscosity of the asphalt cement for ease of handling and application. Cutback MC-250 use in the road maintenance industry where it is used as a prime coat of the base course prior to placing the bituminous surface course.
Cutback Bitumen MC250 Applications
The reduction in viscosity of the bitumen aids the construction of seal coats in road pavements as the softened mixture wets the chips more easily. The cutback agent evaporates from the seal coat, the cutback agent becoming a negligible component of the seal coat a few months after application. If significant amounts of the cutback agent remain in the seal coat an unwanted long term softening effect may result
Bitumen-aggregate mixtures:
Cold-laid plant mix
- Pavement base and surfaces with dense-graded aggregate
- Patching, immediate use
- Patching, stockpile
Mixed-in-place (road mix):
- Pavement base and surfaces with dense-graded aggregate, sand, and sandy soil
- Patching, immediate use
- Patching, stockpile
Bitumen-aggregate applications:
Surface treatments
- Sand seal
Bitumen applications
Surface treatment
- Prime coat on open surface
Cutback agents are used to lowering the viscosity of bitumen when it is applied as a primer to the surface of a road pavement aggregate base course or substrate. Kerosene is used as a bitumen cutback agent at different concentrations according to local conditions and requirements.
The cutback bitumen is ideal for prime coat and cold applied because of easy uses and no need to thinning and heating.
Cutback bitumen MC250 consists of initial incorporation of asphalt into the surface of non-asphalt based course preparatory to any superimposed treatment of construction.
The cutback asphalt MC250 applying to waterproof of surfaces plug capillary voids, coat, and bond loose mineral particles.
meanwhile, Cutback Bitumen MC250 are used as components for road maintenance industry where it is used as a prime coat of the base course prior to placing of the bituminous surface course.
This type of Bitumen is most commonly used as an adhesive material between road foundation and asphalt coating, in the road construction industry which includes superstructure and foundation. Cutback Bitumen MC250 is used Priming of all non-bituminous road buses, provision of temporary surfaces(deviations)
Also, Cutback Asphalt MC-250 is suitable for primer sealing and can also be used in the manufacturing of asphalt pre-mix. Cutback bitumen is used extensively in sprayed sealing applications, particularly in colder weather where they proved improved initial stone retention due to their lower viscosity.
Other uses include roofing as a waterproofing membrane and as an adhesive to stick chippings onto a flat, horizontal roof to minimize the effects of weathering from the sun.
Prime and Tack Coating
The process of priming involves applying a low viscosity binder to a prepared but usually unbound aggregate base. It is intended to be absorbed by the top layers of the base and provide a surface more easily ‘wetted’ by a subsequent bituminous covering. The primer will be able to carry traffic for a short time (although this practice is uncommon) and help control dust. Generally, primers are applied at rates between 0.5 and 1.4 L/m2. Cutback bitumens suitable for priming are also used for tack coats, which are applied to an underlying surface to help with the adhesion of the subsequent asphalt layer. A typical application rate is between 0.2 and 0.4 L/m2.
Prime Sealing
Where temperatures are too cool for an effective priming operation, or where traffic is likely to upset a primed surface before the final seal can be sprayed, a primer seal can be used to give adequate protection of the pavement for periods of up to 6 to 12 months. Cutback bitumens suitable for primer sealing can also be used in the manufacture of pre-mix asphalt, which is used in patch repairs.
Spray Sealing
Cutback bitumens are used extensively in sprayed sealing applications, particularly in cooler weather where they provide improved initial stone retention due to their lower viscosity. Typically, a single application of the appropriate cutback bitumen is sprayed onto the primed pavement onto which aggregate is laid.
MC250 is blended to a low viscosity to ensure that it penetrates the top 10mm of the base with the aid of the cutter, whilst depositing a thin film of bitumen on the surface to provide adhesion between the base coarse and the new surfacing.
Guaranty and Safety of Bitumen MC-250
We guarantee the quality of the cutback MC250 with the arrangement of the international inspector. By checking the quality and quantity of the bitumen on each shipment during the loading to the vessel. Also controlling the production by the QC team via batch test report before shipping.
Packing of Cutback Asphalt MC-250
- Bulk as IBC Tank, Flexi Tank
- Reconditioned steel drums 203 lit., Net Weight: 185 ± 5 Kg
- New steel drums 203 lit., Net Weight: 185 ± 5 Kg
Specification of Bitumen MC-250
Property | Specification Limit | Specification Limit | Test method |
Min | Max | ||
Kinematic viscosity at 60°c, (cSt) | 250 | 500 | ASTM D2170 |
Flashpoint(tag open cup), °c | 66 | — | ASTM D3143 |
Distillation test Distillate, volume percent of total Distillate to 680°f(360°c) | |||
to 437°f(225°c) | — | 10 | ASTM D402 |
To 500°f(260°c) | 15 | 55 | |
to 600°f(316°c) | 60 | 87 | |
Residue from distillation to 680°f(360°c), percent volume by difference | 67 | — | |
Test on Residue from distillation test | |||
Penetration 77°f(25°c) dmm | 120 | 250 | ASTM D5 |
Ductility 77°f(25°c) 5cm/min cm | 100 | — | ASTM D113 |
Solubility in trichloroethylene % | 99 | — | ASTM D2042 |
Water, percent volume | — | 0.2 | ASTM D95 |
Cutback Bitumen MC-70
Cutback Bitumen MC-70 Description

Cutback Bitumen MC70 is a type of dissolved Bitumen. To produce this type, solvent oils such as kerosene are used in order to change bitumen into dissolved bitumen or liquid pitch, so that, during the consumption process, the solvent oil evaporates and bitumen residue to obtain the desired adhesion. In many countries, kerosene and other volatile petroleum-derived products are added as a cutter or cutback agent to bitumen to reduce (or cutback) the viscosity of the bitumen. The mixture obtained may be called cutback bitumen.
Medium curing is the most common category in cutback bitumen, among which, MC-70 grade has the highest demand. MC-70 is a medium curing cutback bitumen that contains 55% bitumen and has the lowest viscosity among all grades. It is black in color and is manufactured strictly as per the ASTM D 2027M-13 standard.
Its commonly used as a Prime Coating. It is homogeneous and will not foam (as observed visually) when heated to application temperature.
MC-70 is medium curing (MC) cut-back asphalt consisting of penetration grade asphalt cement and diluents or cutter of medium volatility. The diluents temporarily reduce the viscosity of the asphalt cement for ease of handling and application. Cutback MC-70 use in the road maintenance industry where it is used as a prime coat of the base course prior to placing the bituminous surface course.
The reduction in viscosity of the bitumen aids the construction of seal coats in road pavements as the softened mixture wets the chips more easily. The cutback agent evaporates from the seal coat, the cutback agent becoming a negligible component of the seal coat a few months after application. If significant amounts of the cutback agent remain in the seal coat an unwanted long term softening effect may result
Mixed-in-place (road mix)
- Pavement base and surfaces with sand
Bitumen applications
- Prime coat on open surfaces
- Prime coat on tight surfaces
- Dust binder
Cutback agents are used to lowering the viscosity of bitumen when it is applied as a primer to the surface of a road pavement aggregate base course or substrate. Kerosene is used as a bitumen cutback agent at different concentrations according to local conditions and requirements.
The cutback bitumen is ideal for prime coat and cold applied because of easy uses and no need to thinning and heating.
Cutback bitumen MC70 consists of initial incorporation of asphalt into the surface of non-asphalt based course preparatory to any superimposed treatment of construction.
The cutback asphalt MC70 applying to waterproof of surfaces, plug capillary voids, coat, and bond loose mineral particles.
meanwhile, Cutback Bitumen MC70 are used as components for road maintenance industry where it is used as a prime coat of the base course prior to placing of the bituminous surface course.
Cutback Asphalt MC-70 Applications
This type of Bitumen is most commonly used as an adhesive material between road foundation and asphalt coating, in the road construction industry which includes superstructure and foundation. Cutback Bitumen MC70 is used Priming of all non-bituminous road buses, provision of temporary surfaces(deviations)
Also, Cutback Asphalt MC-70 is suitable for primer sealing and can also be used in the manufacturing of asphalt pre-mix. Cutback bitumen is used extensively in sprayed sealing applications, particularly in colder weather where they proved improved initial stone retention due to their lower viscosity.
Other uses include roofing as a waterproofing membrane and as an adhesive to stick chippings onto a flat, horizontal roof to minimize the effects of weathering from the sun.
- Although MC 30 is pump-able at ambient temperature, heating of the binder is recommended prior to spray applications.
- Special care must be taken whilst heating, as MC 30 contains flammable cutters that have a flashpoint of >40°C.
- Before priming, the surface of the base course should be well swept.
- The moisture content of the base course should be less than 50% of the Optimum Moisture Content.
- If the base is very dry, dampen slightly with water to prevent the formation of “fish eyes”.
- Apply with a calibrated distributor at a binder spray temperature of 55°C and a minimum road surface temperature of 10°C and rising.
- Drying time is dependent on the porosity of the base course as well as on the prevailing weather conditions. The prime must be allowed to dry before opening to traffic or proceeding with the construction of the surfacing
Properties of Cutback Bitumen MC70
MC70 is blended to a low viscosity to ensure that it penetrates the top 10mm of the base with the aid of the cutter, whilst depositing a thin film of bitumen on the surface to provide adhesion between the base coarse and the new surfacing.
Guaranty and Safety of Bitumen MC-70
we guarantee the quality of cutback MC70 with the arrangement of the international inspector. By checking the quality and quantity of the bitumen on each shipment during the loading to the vessel. Also controlling the production by QC team via batch test report before shipping.
Packing of Cutback Asphalt MC70
- Bulk as IBC Tank, Flexi Tank
- Reconditioned steel drums 203 lit., Net Weight: 185 ± 5 Kg
- New steel drums 203 lit., Net Weight: 185 ± 5 Kg
Specification of Bitumen MC70
property | Specification Limit | Specification Limit | Test method |
Min | Max | ||
Kinematic viscosity at 60°c, (cSt) | 70 | 140 | ASTM D2170 |
Flashpoint(tag open cup), °c | 38 | — | ASTM D3143 |
Distillation test Distillate, volume percent of total Distillate to 680°f(360°c) | |||
to 437°f(225°c) | — | 25 | ASTM D402 |
To 500°f(260°c) | 10 | 70 | |
to 600°f(316°c) | 65 | 93 | |
Residue from distillation to 680°f(360°c), percent volume by difference | 55 | — | |
Test on Residue from distillation test | |||
Penetration 77°f(25°c) dmm | 120 | 300 | ASTM D5 |
Ductility 77°f(25°c) 5cm/min cm | 100 | — | ASTM D113 |
Solubility in trichloroethylene % | 99 | — | ASTM D2042 |
Water, percent volume | — | 0.2 | ASTM D95 |