Oxidized Bitumen 95/25
Oxidized Bitumen 95/25 Description

Oxidized Bitumen 95/25 is Semi Solid grade of pure petroleum bitumen manufactured by air-blowing through an asphalt flux. Special physical properties of its grade can be used in different applications in the construction business. Oxidized bitumen95/25 is based on petroleum bitumen which is made by oxidized bitumen 60/70 by very hot air. The numbers relate to the midpoint of the material’s softening point and penetration respectively. The softening point value is the degrees Centigrade measured by the Ring and Ball method as determined by ASTM D36. The penetration value is in 1/10 mm as determined by IP49 or ASTM- D5.
oxidized Bitumen is industrial bitumen which is dark, petroleum residue modified by the oxidation process. Oxidized Bitumen is produced by passing air through bitumen under controlled temperature conditions. Its consistency ranges from highly viscous to solid. Blown bitumen grade has technical advantages such as durability, flexibility, water-resistant and chemical stability. There is a different grade of blown bitumen.
Oxidized Bitumen 95/25 Applications
Oxidized Bitumen 95/25 is widely used as an anti-slip layer compound in the piling industry, for the manufacture of roofing felts, the roofing and waterproofing industries, for sound dampening felts and undercarriage sealant in the automotive industry, electric cable joint protection, joint filling compound, carpet-backing, corrosion protection, acoustic panels, chemical, fuel, Manufacture of paints, sealant compound, and many others. Also used in sealing saw cuts and joints where expected movements are minimum. It is also used in the manufacturing of bituminous marine mastic for the oil & gas pipeline joints. Further, Oxidized Bitumen is used in the manufacture of bituminous marine mastic, which is required for the oil and gas pipeline joints.
- Oxidized bitumen is used as a sealing of expansion joints.
- Oxidized bitumen is used as a repair of joints or cracks.
- Oxidized bitumen is used as a fixation of parquet floors.
- Oxidized bitumen is used as an adhesive to be used in thermal insulation.
- Oxidized bitumen is used as a repair of unexposed cracks.
- Oxidized bitumen is used as bonding of wet briquettes
- Oxidized bitumen is used in various industries like roofing, isolation, insulation flooring, mastics, pipe coatings, electrical applications.
Technical Advantages of Oxidized Bitumen 95/25
- Durability
- Flexibility
- Water-Resistant
- Chemical Stability
Compared to paving grade bitumen:
- Reduced temperature susceptibility
- Exhibits a more ‘solid’ nature at ambient temperatures
- High penetration index
Storage/handling of oxidized bitumen 95/25
bitumen 95/25 has 10 years validity with multi-time heating and cooling, please refer to MSDS.
Packing of Blown Asphalt 95/25
Various pickings are available for customer’s purpose and conveniences. oxidized bitumen 95/25 in various packing including Kraft bag, meltable plastic bag, drum, and bulk bitumen 95/25 from penetration grade bitumen, which is blown by hot air in a controlled process until the desired specification is reached. oxidized bitumen 95/25 can be supplied in any grade and are designated by two numbers to indicate the softening point and penetration ranges. The bitumen grade 95/25 means the softening point is 95°c and penetration is 15 desi millimeter is produced in compliance and conformity with ASTM standard and meets the following specification.
Specification of Blown Asphalt 95/25
Analysis of bitumen 95/25
Bitumen 95/25 | Test method | Unit | Specification |
Specific gravity @25/25 C | ASTM D70 | (Kg/m3) | 1.05 approx. |
Penetration @ 25°c | ASTM D5 | mm/10 | 20/30 |
Softening point °c | ASTM D36 | °C | 90/100 |
Loss on heating(wt) % | ASTM D6 | Wt. % | 0.2 max |
Flashpoint °c | ASTM D92 | °C | 250 min |
Solubility is CS2(wt) % | ASTM D4 | Wt. % | 99.5 max |
Spot test | A.A.S.H.O.T102 | — | Negative |
Oxidized Bitumen 115/15
Oxidized Bitumen 115/15 Description
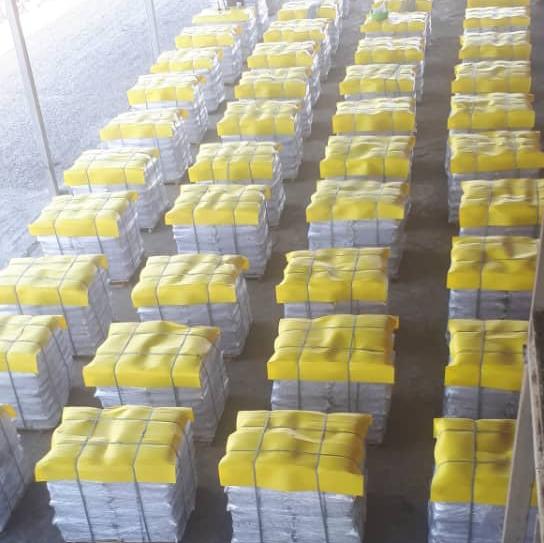
Oxidized bitumen 115/15 is based on petroleum bitumen which is made by blowing bitumen 60/70 by hot air. The most oxidized bitumen usable grade is bitumen 115/15 and 70% of our capacity is dedicated to this grade. bitumen 115/15 is a semi-solid oxidized grade of pure petroleum bitumen categorized in polycyclic aromatic hydrocarbons and oxidized bitumen normally used for different purposes in the construction business. Bitumen 115/115 has a high softening point, high flash point and it is highly stable during melting.
Oxidized Bitumen 115/15 Applications
Blown Asphalt 115/15 is widely used as an anti-slip layer compound in the piling industry, for the manufacture of roofing felts, for sound dampening felts and under carriage sealant in the automobile industry, electric cable joint protection, joint filling compound, sealant compound and many others.
Bitumen 115/15 is widely used as an anti-slip layer compound in the piling industry, for the manufacture of roofing felts, for sound dampening felts and undercarriage sealant in the automobile industry, electric cable joint protection, joint filling compound, sealant compound, and many others.
It’s using as raw material for bitumen coat, roofing, insulation also in Isolation bitumen membrane sheet. Also, Bitumen 115/15 uses in chemical, fuel, paints, lacquers, varnishes, paper-pulp-board, textile processing. In road construction, pavement, crack seal and repairmen, civil works, roofing also construction. Besides, it uses for sealing and insulating buildings, adhesive, construction materials additive, dust-binding, coating. With the wide range uses in the insulating and impregnating agent, make rubber and plastic products.
Bitumen 115/15 products are for paving, roofing. Also used in asphalt-based paints for corrosion protection of metals, inlining public works structures, adhesives in electrical laminates, a base for synthetic turf. Typical uses for Bitumen 115/15 also include roofing, pipe coating, Portland cement pavement, hydraulic applications, paint manufacturing.
Besides, it uses in asphalt-based paints for corrosion protection of metals. Also in lining public works structures, adhesives, electrical laminates, a base for synthetic turf. Furthermore, typical uses for Blown Asphalt 115/15 include roofing, pipe coating, Portland cement pavement, hydraulic applications, paint manufacturing.
Technical Advantages of Blown Asphalt 115/15
- Durability
- Flexibility
- Water-Resistant
- Chemical Stability
Compared to paving grade bitumen:
- Reduced temperature susceptibility
- Exhibits a more ‘solid’ nature at ambient temperatures
- High penetration index
Blown Asphalt 115/15 Storage/handling
Oxidized bitumen 115/15 has 10 years of validity with multi-time heating and cooling, please refer to MSDS. It is better to keep the bitumen 115/15 under shelter and out of the rain, sun. By mopping or by the pour and roll method. Should be heated to a temperature between 180 to 200.
Blown Asphalt 115/15 Packing
The bitumen 115/15 is available in bulk, drum, meltable, and craft bag. This bitumen 115/15 is generally shipped as a solid and heated in a kettle at the worksite.
Blown Asphalt 115/15 CHARACTERISTICS
CHARACTERISTIC | Test method | Unit | Specification |
Specific gravity @25/25 C | ASTM D70 | (Kg/m3) | 1.05 approx. |
Penetration @ 25°c | ASTM D5 | mm/10 | 10/20 |
Softening point °c | ASTM D36 | °C | 110/120 |
Ductility @25 °c | ASTM D113 | Cm | 1.5min |
Loss on heating(wt) % | ASTM D6 | Wt. % | 0.2 max |
Flashpoint c | ASTM D92 | °C | 250 min |
Solubility is CS2(wt) % | ASTM D4 | Wt. % | 99.5 max |
Spot test | A.A.S.H.O.T102 | — | Negative |
Oxidized Bitumen 105/35
Oxidized Bitumen 105/35 Description

Oxidized bitumen 105/35 is a good grade of oxidized asphalt to use as bonding compounds as hot melt adhesive at an application rate of approximately 1 Kg/m3 to bond the preformed sheets together and to structure which is made by Oxidized bitumen 60/70 by hot air. Blown bitumen 105/35 is a semi-solid oxidized grade of pure petroleum bitumen manufactured by air-blowing through an asphalt flux. Special physical properties of its grade can be used in different applications in the construction business.
Oxidized Bitumen 105/35 Applications
Oxidized bitumen 105/35 uses in the chemical, fuel, lacquers, varnishes, paper-pulp-board, textile processing, road construction, pavement, paint, crack seal and repairmen, civil works, roofing, construction business; sealing and insulating buildings, adhesive, construction materials additive, dust-binding, insulating and impregnating agent, make rubber and plastic products. The bitumen 105/35 products are for paving. also used in asphalt-based paints for corrosion protection of metals, inlining public works structures, adhesives in electrical laminates, the base for synthetic turf; typical uses for bitumen 105/35 used also for water-proof application and corrosion resistance for pipe coating, Portland cement pavement, hydraulic applications, paint manufacturing. Blown bitumen 105/35 is using the insulation and isolation bitumen membrane sheet. The car undercoating Automobile industry is especially required for blown bitumen. Vehicle undercoating material is based on Bitumen. Bitumen provides excellent waterproof, dustproof, and noise proof for automobile undercoating.
Blown Asphalt 105/35 should be heated double temperature against the softening point to be able to have flow and viscosity. To use blown bitumen 105/35, surfaces must be dry, clean, and free of loose particles, formwork, curing products, irregularities, slurry, etc.
Storage/handling of blown bitumen 105/35
bitumen 105/35 has 10 years validity with multi-time heating and cooling, please refer to MSDS.
Packing of blown bitumen 105/35
Different packing is available for the customer’s purpose and convenience. bitumen 105/35 in different packing including Kraft bag, meltable plastic bag, drum, and bulk. Blown asphalt 105/35 from penetration grade bitumen, which is blown by hot air in a controlled process until the desired specification is reached. bitumen 105/35 can be supplied in any grade and are designated by two numbers to show the softening point and penetration ranges. The bitumen grade 105/35 means the softening point is 105 and penetration is 35 desi millimeters is produced in compliance and conformity with ASTM standard and meets the following specification.
Specification of blown bitumen 105/35
Analysis bitumen 105/35
Bitumen 105/35 | Test method | Unit | Specification |
Specific gravity @25/25 C | ASTM D70 | (Kg/m3) | 1.05 approx. |
Penetration @ 25°c | ASTM D5 | mm/10 | 30/40 |
Softening point °c | ASTM D36 | °C | 100/110 |
Loss on heating(wt) % | ASTM D6 | Wt. % | 0.2 max |
Flashpoint c | ASTM D92 | °C | 250 min |
Solubility is CS2(wt) % | ASTM D4 | Wt. % | 99.5 max |
Specific gravity @25/25 C | ASTM D70 | (Kg/m3) | 1.05 approx. |
Oxidized Bitumen 105/15
Oxidized Bitumen 105/15 Description

Oxidized asphalt 105/15 (another word, blown asphalt 105/15, oxidized bitumen 105/15) is Semi Solid grade of pure petroleum bitumen manufactured by air-blowing through an asphalt flux. Special physical properties of its grade can be used in different applications in the construction business. Oxidized asphalt 105/15 is based on petroleum bitumen which is made by blowing bitumen 60/70 by very hot air. The numbers relate to the midpoint of the material’s softening point and penetration respectively. The softening point value is the degrees Centigrade measured by the Ring and Ball method as determined by ASTM D36. The penetration value is in 1/10 mm as determined by IP49 or ASTM- D5.
Oxidized Bitumen 105/15 Applications
Oxidized asphalt 105/15 uses in the chemical, fuel, paints, lacquers, varnishes, paper-pulp-board, textile processing, road construction, pavement, crack seal and repairmen, civil works, roofing, construction industries; sealing and insulating buildings, adhesive, construction materials additive, dust-binding, insulating and impregnating agent, make rubber and plastic products. The oxidized asphalt 105/15 products are for paving. also used in asphalt-based paints for corrosion protection of metals, inlining public works structures, adhesives in electrical laminates, a base for synthetic turf; typical uses for asphalt 105/15 used also for water-proof application and corrosion resistance for pipe coating, Portland cement pavement, hydraulic applications, paint manufacturing, caulking, mastics, and damp proofing. Asphalt 105/15 is using the insulation and isolation bitumen membrane sheet. The car undercoating Automobile industry is especially required for Blown Asphalt. Vehicle undercoating material is based on Bitumen. Bitumen provides excellent waterproof, dustproof, and noise proof for automobile undercoating. The oxidized asphalt 105/15 should be heated double temperature against the softening point to support have flow and viscosity. To use asphalt 105/15, surfaces must be dry, clean and after loose particles, formwork, curing products, irregularities, slurry, etc.
Technical Advantages of Blown Bitumen 105/15
- Durability
- Flexibility
- Water-Resistant
- Chemical Stability
Storage and Handling
The heating of packaged bitumen is a critical phase in most of the final uses. Typically, the packaged material is heated and melted in boilers out on site.
However, control at the heating phase is very important in terms of health and safety as well as in maintaining the quality of the product.
The note must be taken of the maximum safe handling temperature of 230 C and this should not be abused. Bitumen is a poor conductor of heat, consequently, control of the heating phase is of paramount importance.
The Blown Bitumen material should be broken up before placement in the boiler. This exposes a larger surface area to the heat and encourages a more even heating regime. Without the larger exposed surface area, aggressive heating at the base and sides of the boiler may well result in localized overheating, altering the characteristics of the modified bitumen and potentially causing thermal cracking of the bitumen, creating the release of low lash vapors. The flashpoint of the oxidized bitumen then becomes irrelevant; as these low flash vapors determine the fire risk.
Melted bitumen should not be left in the boiler and reheated from cold, as there is then a high potential for localized overheating around the heating area (lack of convection means poor heat transfer) and potential development of a pressurized pocket of low flash vapors.
Be aware of the placement of any temperature monitoring or control devices. As a result of the poor thermal conductivity of the bitumen, a thermometer in the bitumen some distance from the heat source could read significantly different (even hundreds of degrees) from the true temperature of the bitumen near the heat source.
For Health and Safety information, please make reference to the relevant MSDS.
Health & Safety
Workers should wear protective masks, gloves, and goggles during application. The asphalt can be removed from equipment and tools with kerosene or gasoline. Care should be taken when heating Blown Bitumen 105/15 to avoid overheating.
Blown Asphalt 105/15 CHARACTERISTICS
CHARACTERISTIC | Test method | Unit | Specification |
Specific gravity @25/25 C | ASTM D70 | (Kg/m3) | 1.05 approx. |
Penetration @ 25°c | ASTM D5 | mm/10 | 10/20 |
Softening point °c | ASTM D36 | °C | 100/110 |
Loss on heating(wt) % | ASTM D6 | Wt. % | 0.2 max |
Flashpoint c | ASTM D92 | °C | 250 min |
Solubility is CS2(wt) % | ASTM D4 | Wt. % | 99.5 max |
Spot test | A.A.S.H.O.T102 | — | Negative |
Blown asphalt 105/15 Packing
Various packings are available for customer’s purpose and conveniences. TAVOIL CO is the manufacturer of asphalt 105/15 in various packing including Kraft bag, meltable plastic bag, drum, and bulk oxidized asphalt 105/15 from penetration grade bitumen.
TAVOIL asphalt 105/15 perchance is supplied in any grade and is designated by two numbers to indicate the softening point and penetration ranges. The oxidized asphalt grade 105/15 means the softening point is 105 and penetration are 15 desi millimeters is produced in compliance and conformity with ASTM standard and meets the following specification.
Oxidized Bitumen 150/5
Oxidized Bitumen 150/5 Description
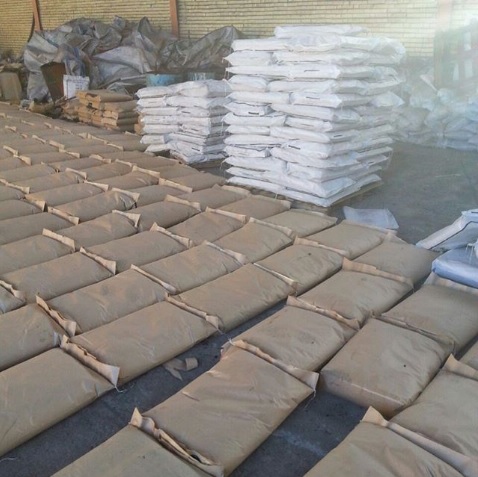
Oxidized bitumen 150/5 is based on petroleum bitumen which is made by blowing bitumen 60/70 by hot air. This type of bitumen is hard and breakable. Oxidized bitumen 150/5 is the semi-solid oxidized grade of petroleum bitumen categorized in polycyclic aromatic hydrocarbons is normally used for different purposes in the construction industries. bitumen 150/5 should be heated double temperature (200ᵒ-300ᵒC) against the softening point to be able to have flow and viscosity. Normally heating of such hard oxidized bitumen should be arranged via hot oil by circulation inside of the isolated jacket. Bitumen oxide 150/5 from penetration grade bitumen, which is blown by hot air in a controlled process until the desired specification is reached. HJ Oil oxidized bitumen 150/5 can be supplied in any grade and are designated by two numbers to indicate the softening point and penetration ranges. The oxidized bitumen 150/5 means the softening point is 150°c and penetration is 15 desi millimeter is produced in compliance and conformity with ASTM standard.
Oxidized Bitumen 150/5 Applications
This Grade of Oxidized uses in the chemical, raw material for bitumen coat, lacquers, varnishes, paper-pulp-board, textile processing, pavement, crack seal and repairmen, civil works, bitumen coat for piping, roofing, construction industries; sealing and insulating buildings, adhesive, construction materials additive, road construction, dust-binding, insulating and impregnating agent, isolation bitumen membrane sheet, make rubber and plastic products. bitumen 150/5 products are for paving, roofing; also used in asphalt-based paints for corrosion protection of metals, inlining public works structures, adhesives in electrical laminates, the base for synthetic turf; typical uses for bitumen 150/5 include roofing, pipe coating, hydraulic applications, 150/5 is mainly using in paint manufacturing and coating in the hot area.
Before using bitumen 150/5 surfaces must be dry, clean, and free of loose particles, curing products, irregularities, and slurry. If you use this type of bitumen without cleaning the area the bitumen 150/5 will easily remove.
Blown Asphalt 150/5 Storage/handling
blown asphalt 150/5 has 10 years validity with multi-time heating and cold, please refer to MSDS. It is better to keep the bitumen 150/5 under shelter and out of the rain, the sun.
Blown Asphalt 150/5 Packing
bitumen 150/5 is available in 25 kg meltable and craft bag, drum, and bulk. Normally oxidized bitumen packing on the pallet and 40 bags can stack on the pallet. 20 pallets can load to the 20ft container.
Specification of Oxidized Bitumen 150/5
Analysis of Blown Asphalt 150/5
Bitumen 150/5 | Test method | Unit | Specification |
Specific gravity @25/25 C | ASTM D70 | (Kg/m3) | 1.05 approx. |
Penetration @ 25°c | ASTM D5 | mm/10 | 4/6 |
Softening point °c | ASTM D36 | °C | 145/155 |
Ductility @25 °c | ASTM D113 | Cm | 1.5min |
Loss on heating(wt) % | ASTM D6 | Wt. % | 0.2 max |
Flashpoint c | ASTM D92 | °C | 250 min |
Solubility is CS2(wt) % | ASTM D4 | Wt. % | 99.5 max |
Spot test | A.A.S.H.O.T102 | — | Negative |
Health & Safety of Blown Asphalt 150/5
Workers should wear protective masks, gloves, and goggles during application. The asphalt can be removed from equipment and tools with kerosene or gasoline. Care should be taken when heating oxidized Bitumen 150/5 to avoid overheating.
Bitumen Coating
Bitumen Coating

Bitumen coating compositions having substantially improved application and drying properties and producing coatings of improved properties including resistance to ultraviolet rays and alligatoring resulting therefrom said coating compositions comprising volatile solvent solutions of a bitumen coating material having softening point between 110 F To 250 F. The bitumen coating are also characteristically non-viscous materials which are not thixotropic and are therefore ordinarily applied as thin films. The bitumen coating compositions may also contain filler materials which tend to settle from the non-thixotropic compositions after storage for only a short time. It has been proposed in the past to add inert colloidal fillers such as silica to obtain thixotropic properties and thicker films on the application of the compositions. However, even such inert fillers tend to affect only solution properties and generally exist in the finished coating as an expensive additive that does not benefit other properties of the coating.
Bitumen Pipe Coating
Bitumen pipe coat can be used both externally and internally on carbon steel pipes. It is usually black, and when applied properly, this coating offers outstanding cathodic protection needed for almost all structural steel pipes situated underground. It is regarded as one of the least expensive ways to provide cathodic protection to pipes. It is also the least complex coating process, making it suitable for casing pipes like in road bore.
Bitumen Paint
Asphalt paint is produced with asphalt as the main material and gasoline as the solvent and through the processes of material selection, dissolving, and sealing in the container. It is in a flowing or semi-flowing state and has a high viscosity and good durability, and its use needs no fire melting. The said asphalt paint is used in sealing roofing, sandwiched layer, etc. In various building engineering.
Bitumen Adhesive, Bitumen Glue
Bituminous adhesive glue is used in cold gluing of construction material in particular for its watertight properties. The known glue is thixotropic, which means that it becomes fluid when shaken, stirred, or otherwise agitated and sets again to a gel when allowed to stand. The thixotropic properties of the known glue are obtained by the presence of both the polymerized oil in combination with the ethyl-vinyl-acetate copolymer resin (EVA) and the non-polymerized oil in combination with oil-absorbing fillers. The use of the combination of these compounds has the advantage that it provides the thixotropic properties without having to use some organic solvents.
Bitumen Felt
An asphalt felt belongs to the field of the building materials. The utility model is characterized in that a solid bitumen thin layer is attached on one surface of the asphalt felt; when the utility model is used, the liquefied bitumen can be first brushed on the top of the storied building using a brush and then one surface of the asphalt felt which the solid bitumen thin layer is attached on the top of the storied building, and the solid bitumen thin layer is syncretized with the liquefied bitumen on the top of the storied building by using a burner to deliver heat with resulting in that the asphalt felt is uniformly covered without causing waste, thus not only enhancing the effect of preventing the seepage of the rainwater but also correspondingly reducing the workload due to that the amount of the used bitumen is reduced. The utility model has a reasonable design and can be used conveniently.
Bitumen Tape
The bitumen tape of the invention is suitable for sanitary and building applications for sealing against water and in vehicles for sealing or for sound insulation especially for the construction or repair of roofs, covering joints, or for the tight connection between masonry or concrete and installing parts like the window frame or sheet metal. The width of the bitumen tape preferably from 24 to 105 mm.
Bitumen Sheet
The bitumen sheet material is transported to a construction or use site, and the sheet material is cut to the desired lengths. The releasable casting film material is removed to expose the tackified surface, and the tacky surface then placed, i.e. Pressed, against the masonry or other surfaces it is designed to protect, and held in place by the tacky nature of the exposed surface of the bitumen layer.
Bitumen Joint Sealer
Bitumen joint sealer dispersion as the sealant to male and/or female sections, even. Of the water and assembly of the joint under sufficient axial pressure to force out some of the sealants on both inside and outside of the joint. Used for sealing of drinking and wastewater pipes, telephone conduits, expansion joints, cracks in masonry, etc. Good adhesion to pipe surfaces of all types is obtd. No displacement of adhesive during assembly of joint occurs, and there is no deformation or embrittlement during long periods of use. Efficient sealing over large contact areas is also obtd.
Bitumen Sealant
Bitumen sealant is a single component, neutral curing, high modulus, fast curing speed. And good adhesive capacity on many base material, having excellent weather ability, And resistance to the bitumen sealant can be applied in any season and easy to apply. There is high bonding strength, non-corrosive, have a strong seal with the majority of Construction materials.
Bitumen Crack Sealer
Crack sealer is deep enough, a grout material, such as a mortar or cement, is used to assist in filling these cracks. In these instances, the grout material is placed in the crack and allowed to harden. Thereafter, the asphalt sealer is placed in the crack over top of the grout material to completely fill the crack and level out the paved surface. This can also create durability issues in that existing grout fillers that are used in crack repair applications often have significant shrinkage issues. Thus, while an asphalt sealer used to help fill a crack may initially be level with the surface being repaired when the grout material shrinks, the asphalt sealer will drop into the crack as the level of the grout material recedes. The asphalt sealer thus is no longer flush with the upper paved surface and often falls into the crack itself.
Bitumen Metal Surface
Bitumen metal surface coat, preparation of the surface is of great importance and will influence the degree of adhesion obtained along with the life of the coating. All surfaces must be sound, stable, and thoroughly cleaned. Anti-corrosive bitumen may be applied on slightly damp but not wet surfaces. For excellent results apply on the dry surface only.
Bitumen Packing
Bitumen in 1MT Jumbo Bag and 300kg BituBag Packing

Bitumen Packing like Bitubags and Jumbo Bags can be a cost-efficient solution to alternate for Bitumen drums. Bitubags can be in two types: 1000 kg and 300kg.
The 300kg Bitubags contain a two-layer cover, which the first tears up and the second burns and melt in the destination tanker (reservoir) Transportation and stuffing: each 20 feet container can hold 18 Jumbo bags (1 MT) or 70 Bitubag (300 kg) so the 300kg bags result in more cost-effective land and ocean freight costs.
Polybags: packing specification: Packed in 3-PLY Poly Bags of 32 Kg (+/-3) Net Weight (Not Available at the moment).
The Bitubag Packing System is a comprehensive cold bitumen logistic/supply chain solution from A to Z for the bitumen industry. It addresses all aspects of the bitumen producer, the logistics, the distributor, and the end-user.
The core element is the Bitumen Bag packing system, a light-weight, durable and flexible bag optimized for container transport that enables several economic and logistic advantages for the entire supply chain. With its unparalleled features, Bitubag packing can increase the producer’s margins, reduce transport costs, and reach markets that could not be supplied economical so far.
Furthermore, with the Bitubag packing system, Bitumen can be stored at virtually no cost. Huge investments in terminals and storage infrastructure become obsolete.
Advantages of Use Bitumen Bag Packing for end-Users

Total flexibility for the bitumen operation
- Availability of bitumen at the site to be used whenever it is needed
Independent of hot bitumen sources - Every conventional means of transport can be used (standard trucks,
20 ft. containers, train, ship) for regional or international transport - Long-term storage up to 12 months without any energy consumption
- Independence of seasonal fluctuations of supply and/or demand
- Expand your bitumen sales market
- Melt and supply just-in-time on-demand
- Balancing seasonal fluctuations
- Substantial energy saving – no heating required during transport and storage
- Significant cost savings over the entire supply chain compared to conventional bulk transport, bitutainers or drums
- Reduce environmental foot-print
- Reliable and efficient equipment (CPU and high-performance melters)
- More independence and flexibility for your supply chain
Bitumen in 1MT Jumbo Bag
To transport bitumen anywhere, a reliable and efficient logistic system is needed – using the fewest special infrastructures, lowest possible total energy consumption, as well as safe and easy storage and handling. For this purpose, the Bitumen Bag Packing System was created.
It allows you to produce, pack, store, transport and sells bitumen independently of seasonal demand, fluctuation, or logistical issues.
It enables the producer to store and use bitumen at any time, cost-effectively, and in any quantity that will meet your requirements.
1. cooling & packing unit
- The Cooling & Packing Unit (CPU) cools the bitumen down to the packing temperature. The process ensures a stable filling temperature.
- and is designed for the safe, continuous filling of the Bitumen Bag with paving bitumen.
- An electronic control system provides for the exact weighing and the complete monitoring and registration of the product as well as the weight of each individual bag.
2- bitumen bag
- The bag is designed as a self-stabilizing container made of plastic material, consisting of a multi-layer outer bag (flexible recyclable fabric) and an inner liner (special-purpose film).
- The Bitumen Bag can carry over 1,000 kg of paving bitumen. Its shape and volume is optimized for maximum loading.
- The bag can be transported by any common transport system (truck, standard container, rail, ship).
- The bag is UV-protected and suitable for every climate. It and can be stored for up to 12 months.
Logistic of Bitumen Bag Packing

The Bitumen Bag Packing System is equipped to supply large volumes of bitumen. the bitumen processing system and ensures the safe filling of bags where quantities and qualities undergo strict control.
The design of the Bitumen Bag is characterized by economic production costs, greater volume, and high stability. Leading industrial partners produce these standardized bags with a constant high level of quality.
Therefore, bitumen in cold conditions can be transported by conventional trucks or sea containers over distances of many thousand miles from continent to continent.
Bitumen in the jumbo bag is the safest and easy handling from loading to destination. Jumbo bag should be designed for bitumen and if you buy from the market and fill bitumen will become fat or collapse. Normally design of bitumen in the jumbo bag is in the bottom the size is bigger than the top and should have the angle to become stable.
Bitumen Classification
Bitumen Classification
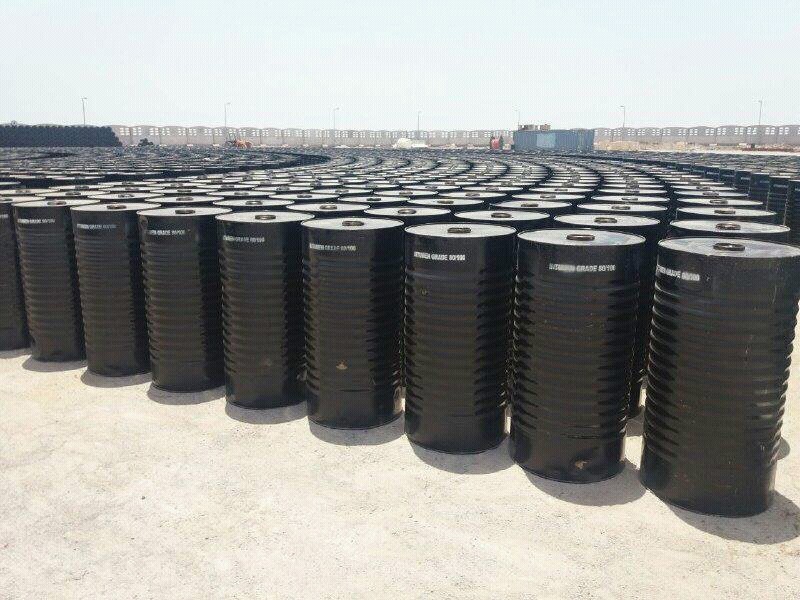
Bitumen classification is according to viscosity (degree of fluidity) gradings. The higher the grade, the stiffer the bitumen. Most high performing roads in Australia are built and maintained using bitumen because it is durable and has exceptional waterproofing and adhesive properties. Bitumens used in road construction and maintenance are refined and blended to meet strict road engineering requirements and industry specifications.
Paving Grade Bitumen Class 170
Class 170 bitumen is widely used in sprayed sealing and light asphalt applications to provide durability and fatigue resistance. It is also used to manufacture cutback bitumens, bitumen emulsions, and modified bitumens.
Paving Grade Bitumen Class 240
Class 240 bitumen is for use in sprayed sealing applications where the local road agency has a preference for a slightly more viscous bitumen than Class 170.
Paving Grade Bitumen Class 320
Class 320 bitumen is most commonly used to manufacture asphalt mixes. Due to its higher viscosity, stiffer asphalt mixes can be produced to improve resistance to shoving and other problems associated with higher temperatures and traffic loads.
Paving Grade Bitumen Class 450
Class 450 bitumen is for use in the manufacture of asphalt mixes where the local road agency has a preference for a slightly more viscous bitumen than Class 320.
Bitumen Class 600
Class 600 bitumen is primarily used to manufacture extra heavy-duty asphalt pavements that need to endure substantial traffic loadings.
Applications
The table below shows typical applications for paving grade bitumens:

Application Temperature Recommendations
Type | C170 | C240 | C320 | C450 | C600 |
Asphalt Mixing | 150 – 160°C | 155 – 165°C | 155 – 165°C | 160 – 170°C | 165 – 175°C |
Asphalt Compaction | 135 – 150°C | 140 – 155°C | 140 – 155°C | 145 – 160°C | 150 – 165°C |
Sprayed Sealing | 175 – 185°C | 180 – 190°C | 180 – 190°C | N/A | N/A |
Typical Characteristics
Type | C170 | C240 | C320 | C450 | C600 |
Viscosity at 60°C, Pa.s | 170 | 240 | 320 | 450 | 600 |
Viscosity at 135°C, Pa.s | 0.4 | 0.45 | 0.53 | 0.66 | 0.8 |
Viscosity at 60°C, after RTFO, Pa.s | 300 | 470 | 640 | 920 | 1300 |
Penetration at 25°C, dmm | 70 | 58 | 46 | 36 | 27 |
Flashpoint, 60°C | 360 | 360 | 360 | 360 | 360 |
Viscosity of residue at 60°C, % of original | 180 | 190 | 200 | 205 | 215 |
Density at 15°C, kg/m3 | 1.04 | 1.04 | 1.04 | 1.04 | 1.04 |
Storage & Handling
The storage of bitumens for prolonged periods at elevated temperatures should be avoided as quality may be adversely affected. As a general rule, bitumen should be stored at the lowest temperature that enables practical use. For normal operations, such as blending and transferring liquid bitumen, temperatures of 10°C to 40°C above the minimum pumping temperature are recommended.

Health & Safety
To ensure hot bitumen is used safely and efficiently the following safety precautions must be followed:
– Wear suitable personal protective equipment (PPE) at all times. Full skin protection is required to avoid accidental burns when transferring or handling hot bitumen.
– Always prevent contact between water and hot bitumen by checking the contents of the previous load before loading bituminous products into tankers and by following procedures to avoid violent boil-over of tanks.
– Avoid exposure to fumes by standing back on the gantry or upwind until the vapors have dispersed.
– Minimize bitumen fume by heating bitumen and asphalt products to the recommended temperatures.
– Minimize the use of diesel when cleaning equipment as this contributes to the bitumen fume.
Polymer Modified Bitumen
Polymer Modified Bitumen Description

Bitumen has been used for thousands of years and its importance as a valued engineering material continues to increase. The interest in the modification of bitumen using polymers, whether virgin, scrap, or polymer blends, is intense. The last two decades, in particular, have seen an increase in the number of academic groups studying polymer-modified bitumen, and correspondingly the peer-reviewed literature in the field has increased. Initially, studies on polymer modified bitumen (PMB) focused more on engineering and empirical measurements, e.g. aging and softening points. However, in recent years a plethora of techniques have been employed in the study of the effect of the addition of polymers on a range of bitumen properties, polymer—bitumen morphology, and polymer—bitumen interactions.
When a polymer is added to regular bitumen, it becomes more elastomeric, which provides it with additional elasticity. The polymer that is added is styrene butadiene styrene (SBS), which acts as a binder modification agent. The primary objective of SBS polymer modified bitumen is to provide extra life to the pavement, roads, and construction designs. Some of the qualities exhibited by PMB are:
- Higher rigidity
- Increased resistance to deformation
- Increased resistance to cracks and stripping
- Better water resistance properties
- High durability
Advantage of using polymer modified bitumen
- stronger road with increased marshall stability value and greater Rigidity.
- better resistance towards rainwater and water stagnation.
- no stripping and no potholes.
- Better resistance to permanent deformation
- reduction in pores in aggregate and hence less rutting and raveling.
- Much higher durability
Common types of Polymer Modified Bitumen
The following table lists some common asphalt cement and HMA modifiers and their general purpose/use.
Type | General Purpose or Use | Generic Examples |
filler | Fill voids and therefore reduce optimum asphalt content Meet aggregate gradation specifications Increase stability Improve the asphalt cement-aggregate bond | Mineral filler crusher fines lime Portland cement fly ash Carbon black |
extender | Substituted for a portion of asphalt cement (typically between 20–35 % by weight of total asphalt binder) to decrease the amount of asphalt cement required | Sulfur Lignin |
rubber | Increase HMA stiffness at high service temperatures Increase HMA elasticity at medium service temperatures to resist fatigue cracking Decrease HMA stiffness at low temperatures to resist thermal cracking (see Figure 2) | Natural Latex Synthetic latex (e.g., Polychloroprene latex) Block copolymer (e.g., Styrene-butadiene-styrene (SBS)) Reclaimed rubber (e.g., crumb rubber from old tires) |
plastic | Polyethylene/polypropylene Ethylene acrylate copolymer Ethyl-vinyl-acetate (EVA) Polyvinyl chloride (PVC) Ethylene propylene or EPDM Polyolefin | |
Rubber-Plastic Combinations | Blends of rubber and plastic | |
Fiber | Improving tensile strength of HMA Mixtures Improving cohesion of HMA Mixtures Permit higher asphalt content without the significant increase in the drain down | Natural: Asbestos Rock wool Manufactured: Polypropylene Polyester Fiberglass Mineral Cellulose |
Oxidant | Increase HMA stiffness after the HMA is placed | Manganese salts |
Antioxidant | Increase the durability of HMA mixtures by retarding their oxidation | Lead compounds Carbon Calcium salts |
Hydrocarbon | Restore aged asphalt cement to current specifications Increase HMA stiffness in general | Recycling and rejuvenating oils Hard and natural asphalts |
Antistripping Agents | Minimize stripping of asphalt cement from aggregates | Amines Lime |
Waste Materials | Replace aggregate or asphalt volume with a cheaper waste product | Roofing shingles Recycled Tires Glass |
Use as needed
While the benefits of using modified asphalts are widely acknowledged, not all asphalt mixes or treatments need to be modified. Each application should be evaluated to determine if the traffic loading, anticipated service life, environmental conditions, and desired performance justify the use of modifiers. Modified asphalts can be a good investment.
The rheological properties of conventional binders may be modified by the introduction of:
Elastomers;
Plastomers;
Crumb rubber;
The modification is costly and is normally justified when bituminous surfacing are subjected to severe conditions such as:
Steep gradients;
Very high road surface temperature;
High traffic loading; or
Heavily trafficked intersections.
Modification may also be advantageous for surfacing on highly flexible and cracked pavements, where an improvement in the rheological properties of the bitumen is required.
Use in such applications should be guided by expert opinion.
In addition to the primary aims above, the range of properties improved include
Durability;
Aggregate retention;
Resistance to permanent deformation;
Resistance to fatigue cracking;
Cohesion (internal strength);
Elasticity;
Viscosity less susceptible to temperature changes.
Modification agents
The primary aim of the modification of bitumen for use in structural layers is to increase the resistance of these layers to permanent deformation at high road temperatures without compromising the properties of these layers over the rest of the prevailing temperature range.
The use of polymer modified bitumen to obtain improved performance is rising as a result of increases in tire pressures, axle loads, and higher traffic volumes.
Improved performance can be achieved in two ways, both of which are aimed at reducing the permanent strain:
An increase in the elastic component with an associated reduction in the viscous component; and
Stiffening of the bitumen to reduce the total viscoelastic response of the layer.
The modification is achieved by the introduction of polymers (including crumb rubber), aliphatic synthetic wax, or naturally occurring hydrocarbons. Polymers can be broadly categorized as “elastomers” (sometimes referred to as thermoplastic elastomers) for improving the strength and elastic properties of a binder, and “customers” (sometimes referred to as thermoplastic polymers) for increasing the viscosity of the bitumen.
Performance Grade Bitumen
Performance Grade Bitumen Description

The performance grade bitumen is based on the evaluation of the material performance when in use, unlike being rational as in the viscosity grading system. The viscosity grading system is more into the experience-based method of grading. And this has proved to have excellent performance for over 20 years in US pavement construction.
The Superpave grading was developed as a part of a 5year strategic highway research planning (SHRP) from 1987 to 1992, to have a performance-based grading system for bitumen. These were developed based on the engineering features that will help in solving many of the engineering problems.
Penetration grading and viscosity grading are somewhat limited in their ability to fully characterize asphalt binders for use in HMA pavement. Therefore, as part of the Superpave research effort, new binder tests and specifications were developed to more accurately and fully characterize asphalt binders for use in HMA pavements. These tests and specifications are specifically designed to address HMA pavement performance parameters such as rutting, fatigue cracking, and thermal cracking.
Superpave Performance Grade Bitumen is based on the idea that an HMA asphalt binder’s properties should be related to the conditions under which it is used. For asphalt binders, this involves expected climatic conditions as well as aging considerations. Therefore, the PG system uses a common battery of tests (as the older penetration and viscosity grading systems do) but specifies that a particular asphalt binder must pass these tests at specific temperatures that are dependant upon the specific climatic conditions in the area of use. Therefore, a binder used in the Sonoran Desert of California/Arizona/Mexico would have different properties than one used in the Alaskan tundra. This concept is not new – the selection of penetration or viscosity graded asphalt binders follows the same logic – but the relationships between asphalt binder properties and conditions of use are more complete and more precise with the Superpave PG system. Information on how to select a PG asphalt binder for a specific condition is contained in the Superpave mix design method. Table 1 shows how the Superpave PG system addresses specific penetration, AC, and AR grading system general limitations.
Performance Grade (PG) bitumen is bitumen which is graded based on its performance at different temperatures. The Long-Term Pavement Performance(LTPP) has given certain algorithm to calculate the temperature of the pavement based on the temperature of the air above. From this, the highest and the lowest temperatures of the pavement is calculated and the bitumen that performs well in that temperature range is selected.
Limitations of Penetration, AC and AR Grading Systems | Superpave Binder Testing and Specification Features that Address Prior Limitations |
---|---|
Penetration and ductility tests are empirical and not directly related to HMA pavement performance. | The physical properties measured are directly related to field performance by engineering principles. |
Tests are conducted at one standard temperature without regard to the climate in which the asphalt binder will be used. | Test criteria remain constant, however, the temperature at which the criteria must be met changes in consideration of the binder grade selected for the prevalent climatic conditions. |
The range of pavement temperatures at any one site is not adequately covered. For example, there is no test method for asphalt binder stiffness at low temperatures to control thermal cracking. | The entire range of pavement temperatures experienced at a particular site is covered. |
Test methods only consider short-term asphalt binder aging (thin film oven test) although long-term aging is a significant factor in fatigue cracking and low temperature cracking. | Three critical binder ages are simulated and tested:Original asphalt binder prior to mixingwith aggregate.Aged asphalt binder after HMAproduction and construction.Long-term aged binder. |
Asphalt binders can have significantly different characteristics within the same grading category. | Grading is more precise and there is less overlap between grades. |
Modified asphalt binders are not suited for these grading systems. | Tests and specifications are intended for asphalt “binders” to include both modified and unmodified asphalt cements. |
How to read a Performance Grade?
The PG grading system is based on climate, so the grade notation consists of two portions: high and low pavement service temperature. The major concern for high-temperature performance is rutting, which typically takes time to cumulate, therefore an average of 7-day maximum pavement temperature is used for describing the high-temperature climate. On the low-temperature side, thermal cracking can happen during the one really cold night; therefore the minimum pavement temperature is used for describing the low-temperature climate. For both high and low-temperature grades, PG grades are graded in a 6°C increment. The average 7-day maximum pavement temperature typically ranged from 46 to 82°C, and minimum pavement temperature typically ranged from −46°C to −10°C.
A binder identified as PG 64-10 must meet performance criteria at an average 7-day maximum pavement temperature of 64°C and also at a minimum pavement temperature of −10°C. Please note that maximum pavement temperature is typically higher than the air temperature by about 20°C since the dark color pavement absorbs the heat and retains it. The maximum pavement temperature is typically measured at about 1 inch below the pavement surface. However, the minimum pavement temperature occurs on the surface of the pavement and is equal to the air temperature.
The common minimum reliability used is 98%, so that means when the PG 64-10 binder is selected, the asphalt binder in the AC pavement should perform satisfactorily under normal traffic condition at the location where the extreme pavement temperature is within the range of −10°C and 64°C throughout its service life with a minimum 98% confidence level. Where the traffic condition is not typical, such as the really heavy traffic like an interstate highway, or slow traffic such as bus stop or intersection area, one or two grades stiffer asphalt binder may be used to help prevent the rutting problem.
Polymer modified binders are used wherever extra performance and durability are desired. Improvement in resistance to rutting, thermal cracking, fatigue damage, stripping, and temperature susceptibility have led polymer modified binders to be substituted for asphalt in many paving and maintenance applications. Especially when good rutting resistance for high temperature and good thermal cracking resistance for low temperatures are concurrently required in the same application, the polymer modification is generally required.
rule of thumb to differentiate the polymer modified binder from unmodified binder is to add both low and high-temperature grades together, if the sum is greater than 90, it is likely to be a polymer modified binder. For example, a Performance Grade bitumen 76-22 is likely to be a polymer modified binder since the sum is 98, while a Performance Grade Bitumen 64-10 is likely to be unmodified since the sum is 74.
PG Bitumen – Unmodified CHARACTERISTICS
PG 46-34 | PG 46-28 | PG 52-28 | PG 58-28 | PG 58-22 | PG 64-22 | AASHTO Method | |
---|---|---|---|---|---|---|---|
Original Binder | |||||||
Flash Point, COC,°C | 230 | T 48 | |||||
Flash Point, P-M, °C | NS | ≥ 204 | ASTM D93 | ||||
Rotational Viscosity @ 135°C, Pa·s | 3.00 | T 316 | |||||
Dynamic Shear @ Grade Temperature,°C | 46 | 46 | 52 | 58 | 58 | 64 | T 315 |
G*/sin @ 10 rad/sec, kPa | ≥ 1.00 | ||||||
RTFOT Residue | |||||||
Mass Loss, % | ≤ 1.00 | T 240 | |||||
Dynamic Shear @ Grade Temperature,°C | 46 | 46 | 52 | 58 | 58 | 64 | T 315 |
G*/sin @ 10 rad/sec, kPa | 2.20 | ||||||
PAV Residue (Aging Temperature, °C) | 90 | 100 | R 28 | ||||
Dynamic Shear @ Grade Temperature,°C | 10 | 13 | 16 | 19 | 22 | 25 | T 315 |
G*/sin @ 10 rad/sec, kPa | 5000 | ||||||
Creep Stiffness | -24 | -18 | -18 | -18 | -12 | -12 | |
S, Mpa | ≤ 300 | T 313 | |||||
m-value | ≥ 0.30 | T 313 |