Polybutadiene Rubber (PBR)
Butadiene Rubber
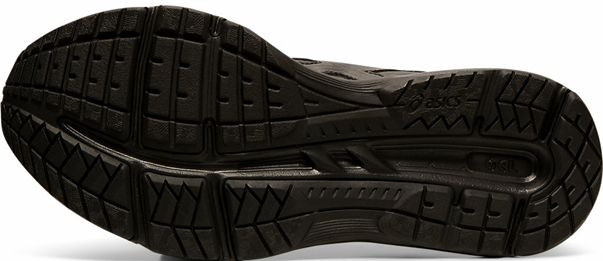
Polybutadiene rubber is rubber for general use. The most usage of butadiene rubber is tire sidewall, floor covering-bicycle tire, foot wear, rubber toy, cable and rubber pipes. They are produced by butadiene. It may be present in macromolecules in form of cis-1.4, trans-1.4 and 1.2 structural units. 1.2 units have pendant vinyl group; thus, they may create isomeric forms (syndiotactic, isotactic or atactic).
Content of individual forms of butadiene rubber structural units in polymeric chain depends on the polymerization method and type of used initiator and it determines basic properties of butadiene rubber.
Butadiene rubber-BR is a synthetic rubber. Polybutadiene rubber is a polymer formed from the polymerization of the monomer 1,3-butadiene. Polybutadiene has a high resistance to wear and is used especially in the manufacture of tires, which consumes about 70% of the production. Another 25% is used as an additive to improve the toughness (impact resistance) of plastics such as polystyrene and acrylonitrile butadiene styrene (ABS). Polybutadiene rubber accounted for about a quarter of total global consumption of synthetic rubbers in 2012.
Butadiene rubber, synthetic rubber widely employed in tire treads for trucks and automobiles. It consists of polybutadiene, an elastomer (elastic polymer) built up by chemically linking multiple molecules of butadiene to form giant molecules, or polymers. The polymer is noted for its high resistance to abrasion, low heat buildup, and resistance to cracking.
Description of Poly Butadiene Rubber (PBR)
Polybutadiene [butadiene rubber BR] is a synthetic rubber. PBR is a polymer formed from the polymerization of the monomer 1, 3-butadiene. Polybutadiene has a high resistance to wear and is used especially in the manufacture of tires, which consumes about 70% of the production. Another 25% is used as an additive to improve the toughness (impact resistance) of plastics such as polystyrene and acrylonitrile butadiene styrene (ABS). PBR accounted for about a quarter of total global consumption of synthetic rubbers in 2012. It is also used to manufacture golf balls, various elastic objects and to coat or encapsulate electronic assemblies, offering high electrical resistivity.
Application of Poly Butadiene Rubber
ATDM 1220 is appropriate for rubber compounds used in:
- the inner tube of hoses for sandblasting, along with natural rubber.
- cover of hoses, mainly pneumatic and water hoses.
- railway pads, bridge blocks, etc.
- manufacturing of the high-restitution toy Super Ball.
- fuel in combination with an oxidizer in various Solid Rocket Boosters such as Japan’s H-IIB launch vehicle.
- Tires
- Conveyor belts
- Crack pads
- Footwear soles
- V-belts
- Golf balls
Packing of Polybutadiene Rubber
35 ±0.5 KG bales wrapped with polyethylene film.
36 bales per crate (1260±18 KG).
Specification of Polybutadiene Rubber
Typical Properties | Units | Values | Test methods |
Compound Mooney Viscosity | MU | MAX 77 | ASTM D – 1646 |
Tensile Strength(35 Min) | Kgf/cm3 | MIN 150 | ASTM D412 |
Elongation at Break (35 Min) | % | MIN 440 | ASTM D412 |
300% Modulus at 145 °C | |||
25 Min | Kgf/cm3 | 68-108 | ASTM D412 |
35 Min | Kgf/cm3 | 74-114 | ASTM D412 |
50 Min | Kgf/cm3 | 74-114 | ASTM D412 |
Asphalt oil
Asphalt
Asphalt, also known as bitumen is a sticky, black, highly viscous liquid or semi-solid form of petroleum. It may be found in natural deposits or may be a refined product, and is classed as a pitch. Before the 20th century, the term asphaltum was also used. The word is derived from the Ancient Greek ἄσφαλτος ásphaltos. The Pitch Lake is the largest natural deposit of asphalt in the world, estimated to contain 10 million tons.
Petroleum Asphalt
Petroleum asphalt is a sticky, black and highly viscous liquid or semi-solid that is present in most petroleum crude oils and in some natural deposits. Petroleum crude oil is a complex mixture of a great many different hydrocarbons. Petroleum asphalt is defined as that part of crude oil which is separated from the higher-boiling hydrocarbons in crude oil by precipitation upon the addition of lower-boiling hydrocarbon solvents such as propane, pentane, hexane or heptane. The precipitated material consists of asphaltenes which have an average molecular weight of about (800 – 2500 g/mole) and exist in the form of flat sheets of polyaromatic condensed rings with short aliphatic chains.
Over the years, petroleum asphalt has been referred to as bitumen, asphaltum or pitch. The terminology varies from country to country and from individual to individual. Asphalt is often confused with coal tar (or coal pitch) derived from the pyrolysis of coal and which has a different chemical structure than asphalt.
When petroleum asphalt is combined with construction aggregate (sand, gravel, crushed stone, etc.) for use in road construction or paving, it has often been referred to as asphaltic concrete, asphaltic cement, bituminous concrete, blacktop or road tar.
Asphalt Oil

Technology of asphalt pavements by asphalt oil started 170 years ago, with an experiment involving natural rubber with bitumen in the 1840s, attempting to capture the flexible nature of rubber in a longer lasting paving surface. Now a day’s especially rubber process oil use instead of natural rubber for bitumen rubber blend as asphalt oil for pavement.
Nowadays the rubberized asphalt technology is being adopted in many other parts of the world: Taiwan is pioneer inasphalt mixtures for flexible pavement rehabilitation; furthermore, rubberised asphalt oil has been trialled in Beijing and for use in new and maintenance work as part of the preparation for the 2008 Olympics in China and it has also been used in EcoPark Project in Hong Kong.
Blending rubber oil with bitumen in asphalt
The principal objects of adding rubber to bitumen are to give the bitumen elasticity, to increase its ductility and to reduce its susceptibility to temperature changes. The effectiveness of rubber in bringing about these desirable changes depends on the extent to which the rubber dissolves in the bitumen. To dissolve read ily, the rubber must be unvulcanised and be in a finely divided state. Rubber exists in this condition in the form of latex, and it is known to add rubber in this form both to bitumen emulsions and to hot bitumen and to add rubber in the forms of vulcanized and unvulcanised rubber powder to hot bitumen and to asphalt paving mixtures during the process of mixing.
Distillate Aromatic Extract (DAE)
Description of Distillate Aromatic Extract

Distillate Aromatic Extract is an aromatic oils with a large number of aromatic cycles in their composition; they are characterized by their low aniline point and their high solvent power. They are primarily used in formulation with polar rubbers of the SBR and NR types.
DAE aromatic rubber oil (distillate aromatic extract, abbreviated as DAE) distillate aromatic extracts have very high aromatic contents. DAEs are obtained as a byproduct of the process of solvent extraction of vacuum distillates used as a raw material in the manufacture of p m lubricant base oils. DAE grades are DAE 10 , DAE 11 , DAE 20 , DAE 40 ,DAE 50 , DAE 60 .
Estimation of mixture behaviors was accomplished through the use of a suite of representative structures that are expected to be present in these DAEs. In general, the components of DAEs are poorly soluble in water, very hydrophobic, and moderately to poorly volatile, although some will evaporate readily from water. DAEs are expected to predominantly reside in sediment and soil, with some lighter components partitioning to air.
Application of Distillate Aromatic Extract
DAE distillated aromatic extract combination is used as:
- Carrier oils
- Plasticizer
- Diluents & filling agent
- Good Solubility Properties
- processing ability of rubber in milling and mixing
- Heavy fuels
- Feed stock for production of carbon black
- Petroleum pitches and resins
- Manufacture of rubber and plastics
Packing of Distillate Aromatic Extract
Packing DAE10, DAE20, DAE40, DAE50, DAE60 can be in new steel drum, one new steel drum capacity is 200-210 liter , recondition or used drum also can contain same quantity per drum totally 16.500 to 17.000 MT DAE different grade can load on one 20foot container equal to 80 drum , ISO tank capacity is 20 MT net weight same as flexi tanks.
Specification of DAE
Characteristic | Test method | 60 | 50 | 40 | 20 | 11 | 10 |
Kinematic viscosity @ 100°C, cSt | ASTM D-445 | 60.0 | 50.0 | 40.0 | 20.0 | 11.0 | 10.0 |
Flash point, °C | ASTM D-92 | 300 | 265 | 265 | 240 | 215 | 215 |
Pour point , °C | ASTM D-97 | 20 | 20 | 15 | 15 | 9 | 9 |
Specific gravity @ 15 , Kg/m3 | ASTM D-1298 | 995 | 1020 | 1010 | 1005 | 1000 | 1000 |
Aniline point, °C | IP-2 | 65 | 40 | 50 | 45 | 30 | 35 |
Sulphur content, Wt% | ASTM D-2622 | 5 | 5 | 5 | 4 | 5 | 3 |
Ash content , Wt% | ASTM D-482 | 0.15 | 0.15 | 0.15 | 0.15 | 0.1 | 0.1 |
Carbon type analysis , % | |||||||
CA | ASTM D-3238 | 35 | 50 | 30 | 40 | 60 | 55 |
CN | 5 | 5 | 4 | 15 | 1 | 1 | |
CP | 60 | 45 | 65 | 45 | 39 | 44 |
Treated Distillate Aromatic Extracts (TDAE)
Description of Treated Distillate Aromatic Extracts

Treated distillate aromatic extracts (TDAE) is a rubber processing oil with high aromatic content. It is used rubber softening additive in the process of vulcanization of rubber. Its high viscosity-gravity constant has made it highly preferable in the tire manufacturing applications, thereby, reducing heat buildup. Due to this characteristic of treated distillate aromatic extracts, it is possible to produce large rubber based intermediate products.
TDAE (Treated Distillate Aromatic Extract.) is a non-carcinogenic mineral oil, used as aromatic process oils for the manufacture of oil extended natural or synthetic rubber and tire compounds. This environment friendly process oil is used as a softening additive in the process of vulcanization of natural rubber and as a component of rubber compounds. Its high viscosity gravity constant (VGC) leads to the reduction in heat buildup and rotational resistance during the usage of tires. Such characteristics enable our TDAE to be used in the production of high quality tire and rubbers.
TDAE is Eco friendly rubber oil which is according European standard , low PCA content which is below 3% makes TDAE as safe oil , more than 3% of PCA may cuase skin cancer in human, also PAH should be below 10 ppm .
The global TDAE market has been experiencing moderate growth in terms of consumption over the past few years. The market is heading towards growth expansion and it is expected to grow progressively in the coming years. Demand for TDAE is largely belongs to the growth of the transportation industry. It is primarily used in the production of the tire, which is highly required in the transportation industry. As per the industry experts, transportation industry is poised to grow beyond USD 1.3 trillion by 2020, expanding at dynamic CAGR of over 8%, and likely to set enhanced consumption of TDAE. Rubber products are being increasingly used in a broad spectrum of application in the industries ranging from the agriculture to textile with emergence of FMCG sector as a game changer. Widening application scope of TDAE is providing enhanced growth prospects year by year to this market. On the split side, TDAE contains high polymeric hydrocarbon content which us highly hazardous to the environment. Due to which European Union have regulated strict regulation on the consumption of TDAE and regulations are further followed by non-European countries by restraining the global demand for TDAE.
Treated distillate aromatic extract (TDAE), used as rubber softening additive in rubber processing, and rubber has diverse application across the industrial manufacturing. Increasing industrial output as a result of rising industrial manufacturing is set to uplift the consumption of TDAE and is likely to provide tremendous growth opportunities.
Application of Treated Distillate Aromatic Extracts
- industry ink formulations
- isolation manufacturers
- automobile tire making factory
- rubber manufacturing
- shoes
- flooring
- cables and any other industrial interface
- as an ingredient (softener/plasticizer)
- as a processing aid in the production of natural and synthetic rubber products.
- as an ingredient in certain engine, gear and lubricating oils.
Packing of TDAE
Packing can be in new steel drum, recondition or used drum also can load on one 20foot container equal to 80 drum , ISO tank capacity is 20 MT net weight same as flexi tanks.
Specification of TDAE:
Characteristic | Unit | Result | Test Method |
Sp.gr @ 15˚C | kg/m3 | 953 | ASTM D-1298 |
Flash Point | ˚C | 246 | ASTM D-92 |
Congealing Point | ˚C | 33 | ASTM D- 938 |
TAN | mg KOH/gr | 0.12 | ASTM D-974 |
Kinematic Viscosity@40°C | cSt | 549.48 | ASTM D-445 |
Kinematic Viscosity @50 °C | cSt | 260.8 | ASTM D-445 |
Kinematic Viscosity @100 °C | cSt | 19.65 | ASTM D-445 |
RI@20˚C | — | 1.5227 | ASTM D-1218 |
RI@67˚C | — | 1.5113 | ASTM D-1218 |
VGC | — | 0.895 | ASTM D-2501 |
Aniline point | ˚C | 63 | ASTM D-611 |
Refractivity Intercept | — | 1.051 | AMS140.13 |
Water Content (Karl Fischer) | ppm | 412.2 | ASTM D-6304 |
Sulphur Content | %(W/W) | 3 Max | ASTM D-2622 |
Carbon Type Distribution | % CA/CN/CP | 23/39/38 | AMS 140.13 |
Content Of PCA Extract | %(W/W) | 2.2 | IP 346 |
Paraffinic Rubber Process Oil
Description of Paraffinic oils
This category of hydrocarbons constitutes branched chain or straight linked hydrocarbon molecules of various viscosities. Because the chain length will increase, the viscosity will increase, and also the rubber process oil becomes a lot of viscous. They find extensive usage in ethylene-propylene rubbers.
These are more stable and have the highest flash purpose for a given viscosity. This class of hydrocarbons constitutes branched chain or straight linked hydrocarbon molecules of various viscosities. As the chain length increases, the viscosity increases and the RPO becomes more viscous.
They find extensive usage in EPDM, Butyl rubbers. Include Paraffinic oils with high viscosity and high flash point is good for shelf life of the end product. The high viscosity and high flash point paraffinic oils are extensively used in EPDM profiles for automotive applications.
Advantages of Paraffinic oils
Paraffinic Oils are generally light in color having wide viscosity range, higher Aniline &Flash Point. It is extensively used in the manufacturing of butyl tubes, EPDM based rubber products, such as profiles, hose pipe& automotive Components.
Aromatic Rubber Process Oil
Description of Aromatic oils
The primary Characteristics of aromatic Hydrocarbons are the presence of the double bonded mix ring carbon structure. Aromatic extender oil well-known according to its viscosity which meets ASTM D-445 and Kinematic viscosity of transparent and opaque liquids it has different grades famous as high(heavy), medium, low (light) viscosity, TDAE, MES, and DAE.
Aromatic furfural extract rubber process oil (RPO) procured from selected refineries and suitably blended to meet stringent specifications, are used for compounding batches to manufacture tires, lactic, automotive tires and tubes, bicycle tires, tire re-treading materials, belting, hoses, battery casings and containers, extruded products, technical molded goods and rubber articles with reclaim rubber due to high solvency, calendared and molded sheets, Tread rubber TDAE oil. Also process oil (furfural extract) has color stability, solubility, and good thermal stability.
Aromatic Rubber Process Oil (RPO) is rich aromatic by products from solvent extracting process to modify physical properties of the vulcanization and to reduce the cost of the finished product.
Iran rubber process oil is special furfural extract RPO which can be broadly classified into two different groups (as below) depending on the physical arrangement of the carbon atoms. Paraffinic, aromatics. Rubber Process Oil are used during mixing of rubber compounds. These help in improving the dispersion of fillers and flow characteristics of the compound during further processing. Rubber process oil are specially developed taking into consideration the type of rubber and the end product applications.
Application of Aromatic RPO
- Used in manufacturing of products such as tires for automobiles, trucks and construction machinery, manufacture of microwave
- Used in connectors for household appliances such as washing machines and dishwashers, rubber roller
Rubber Process Oil
Rubber Process Oil Description
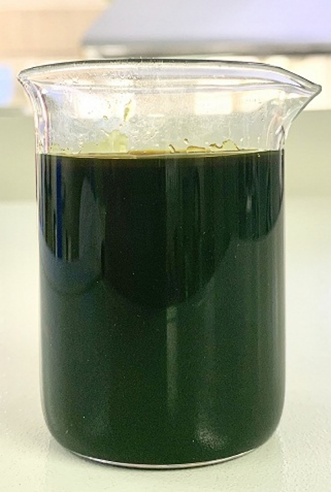
Rubber Process oil is produced by Crude oil distillation process obtained from the composition and chemical interactions and isolation material extracted called Raffinate.
The primary characteristics is the presence of the double bonded mix ring carbon structure. Aromatic extracts procured from refineries are suitably blended to meet stringent specifications with different Viscosity.
Heavy RPO is also an aromatic process oil with higher viscosity and is specifically developed for use as an extender oil in the manufacture of polystyrene butadiene rubber. This aromatic type of rubber process oil is dark in color and has good solvency. It is compatible with most rubber polymers.
Rubber process oil, both synthetic and natural is commercially used to produce products from rubber bands to a toy to the giant tires for various vehicles including aircraft. Rubber Process Oils are used during the mixing of rubber compounds.
Rubber process oil is an oil composition which has a kinematic viscosity at 100 °C of from 32 to 50 CST and which contains less than 3%. Polynuclear aromatic compounds are employed as a process oil for rubber compounds, especially aromatic rubbers.
Light Rubber Process Oil
light / Low viscosity Aromatic process oil product Is fully rich aromatic RPO By-Product from Solvent Extracting Process to Modify Physical Properties of the Vulcanization and to reduce the Cost of the Finished Product. This Product Has Good Elastomeric Compatibility And Low Volatility. Light Aromatic Process Oil Well-Known According To Its Viscosity Which Meet ASTM standards and ISO 3104 (American Society For Testing And Materials) Standard Test Method For Kinematic Viscosity Of Transparent And Opaque Liquids (Calculation Of Dynamic Viscosity) .
Heavy Rubber Process Oil
heavy / high Aromatic Process Oil Product Is Fully Rich Aromatic RPO By-Product From Solvent Extracting Process To Modify Physical Properties Of The Vulcanization And To Reduce The Cost Of The Finished Product. This Product Has Good Elastomeric Compatibility And Low Volatility. heavy Aromatic Process Oil Well-Known According To Its Viscosity Which Meet ASTM standards and ISO 3104 (American Society For Testing And Materials) Standard Test Method For Kinematic Viscosity Of Transparent And Opaque Liquids (Calculation Of Dynamic Viscosity).
Uses of RPO
It is compatible with most rubber polymers and suitable for use in the manufacture of automobile rubber tires, belting, battery case etc. where color is not an important parameter. Heavy RPO was specially developed for use in SBS rubber.
Automobile Tires
Rubber shock absorbers
Footwear
Industrial Hoses
Wire and cable coverings,
Flooring materials and carrier fluid
The solvent in the manufacture of adhesives
Sealants
Polishes and carbon black
Advantages of RPO
Good abrasion resistance
Good low temperature flexibility
Low amounts of waste tires in the process
Good resistance to reversion
According to with international standards (EU 2005/69/EC)
Save fuel and energy consumption
Extend tires life time
It is used by tire manufacturers who make tires for exporting to European Union.
Packing of RPO
packed in new or used 210 kg drums, iso tank, flexitanks, and IBC tank. Each 20-foot container takes 80 drums.
Specification
Heavy RPO
NO | Characteristic | Value | Test method |
1 | Flash point | 230 | ASTM D-92 |
2 | Kinematic viscosity @ 100 °C | 30-40 | ASTM D-7042 |
3 | Aniline point, ˚C | Max 45 | ASTM D-611 |
4 | Pour point, ˚C | Max +36 | ASTM D-97 |
5 | VGC (typical) | 0.96 | ASTM D-2501 |
6 | Density at 15.6 °C Kg/m3 | 1010 | ASTM D-4052 |
Light RPO
NO | Characteristic | Value | Test method |
1 | Flash point | 200-230 | ASTM D-93 |
2 | Kinematic viscosity @ 100 °C | 20-35 | ASTM D-445 |
3 | Aniline point, ˚C | ASTM D-611 | |
4 | Density@15°C | 1.01 | ASTM D-1298 |
5 | Refractive Index | 1.55 | ASTM D-1218 |
6 | Oil Type | Aromatic |
Base Oil SN500
Base Oil SN500 Description

Base Oil SN500 is a base oil at upper end of the specifications for Grade I base oils which has undergone solvent refining and dewaxing processes. It offers broad blending coverage with performance capabilities in a broad range of lubricant applications including marine, automotive and industrial applications.
It is a Group I base oil that has undergone solvent refining and dewaxing processes. This oil has no impurities or compounds that can have an adverse effect on the quality of the oil.
Base oils are used to manufacture products including lubricating greases, motor oil and metal processing fluids. Different products require different compositions and properties in the oil.
One of the most important factors is the liquid’s viscosity at various temperatures. Whether or not a crude oil is suitable to be made into a base oil is determined by the concentration of base oil molecules as well as how easily these can be extracted.
Since most of the base oil used in the production of lubricants obtained from oil resources.
base oil properties of the oil obtained is dependent on the type of crude oil and refining operations. base oil is chemical components during the refining process of crude oil from which it obtained, to inherit. Since crude oil containing different combinations such as paraffinic hydrocarbons, naphthenic and aromatic sulfur compounds are also, base oil are also made up of these compounds.
base oil composition comprising a major effect on the properties of spent oils, paraffinic compounds, naphthenic and aromatic.
Base Oil SN500 Applications
Base oil SN500 serves as a base stock for several industrial lubricants
- Motor oil
- Industrial oil
- Lubricating greases
- Metal processing fluids
- Additives
- Hydraulic oils
- Transformer oils
- Coating
- Medicine
- Paints
Packing
packed in new or used 210 kg drums, iso tank, flexitanks, and IBC tank. Each 20-foot container takes 80 drums.
Handling health & Safety
Lubricants consisting of highly refined mineral oils with specification additives. In normal conditions of use, this lubricant presents no particular toxic hazard. All lubricants, of any kind should be handled with great care, particularly avoiding can contact with the skin.
Prevent any splashing, and keep away from combustible materials. Store undercover and away from any risk of pollution. Dispose of the used oil correctly; don’t pour down drains, into watercourses or the soil.
Specification of SN500
SPECIFICATION | LIMIED | TEST RESULT | METHOD |
Viscosity @100˚C | Max 10.8 | 11 | ASTM D-445 |
Viscosity @40˚C | Report | 100 | ASTM D-445 |
Viscosity Index | Min 87 | 94 | ASTM D-2270 |
Flash Point ˚C | 235 | 240 | ASTM D-92 |
Pour point | Max -3 | -5 | ASTM D-6749 |
Total Acid Number mgKOH/g | 0 | 0.03 | ASTM D-664 |
Color | 2 | 2 | ASTM D-1500 |
Density at 15°C,Kg/L | Report | 0.895 | ASTM D-4052 |
Base Oil SN350
Description of Base Oil SN350

Base Oil SN350 For lubrication oil which is considered as a basis and after adding additives to the final lubricant called based oil.
In terms of volume of lubricant base oil is one of the most important components in the lubricant base oil formulation, on average, 95% up. Some groups, such as hydraulic and compressor lubricant, chemical additives and only 1% base oil makes up 99% combined.
Other lubricants like metal working fluids, lubricants and gear oils contain additives may be up to 30%. base oil can be obtained from oil or non-oil sources.
Mineral base oils are intended for the most commercial lubricants production. They are produced from the vacuum distillates and residual components using the traditional refining methods (selective treatment, dewaxing, further deresination for the residual components).
Base oil is produced by means of refining crude oil. This means that the crude oil is heated in order that various distillates can be separated from one another. During the heating process, light and heavy hydrocarbons are separated – the light ones can be refined to make petrol and other fuels, while the heavier ones are suitable for bitumen and base oils.
Uses
Base oil SN350 serves as a base stock for several industrial lubricants
- General-purpose oils
- Mould oil
- Transmission fluids
- Gear Oils
- Metalworking fluids
- Additives
- Hydraulic Oils
- Transformer Oils
Base Oil SN350 Packing
packed in new or used 210 kg drums, iso tank, flexibags, and IBC tank. Each 20-foot container takes 80 drums.
Handling health & Safety
Lubricants consisting of highly refined mineral oils with specification additives. In normal conditions of use, this lubricant presents no particular toxic hazard. All lubricants, of any kind should be handled with great care, particularly avoiding can contact with the skin.
Prevent any splashing, and keep away from combustible materials. Store undercover and away from any risk of pollution. Dispose of the used oil correctly; don’t pour down drains, into watercourses or the soil.
Specification of Base Oil SN350
SPECIFICATION | MIN | MAX | METHOD |
Viscosity @100˚C | 7.5 | 9 | ASTM D-445 |
Viscosity @40˚C | 67 | 70 | ASTM D-445 |
Viscosity Index | 90 | 100 | ASTM D-2270 |
Flash Point ˚C | 220 | 230 | ASTM D-92 |
Pour point | 0 | 0 | ASTM D-97 |
Total Acid Number mgKOH/g | 0 | 0.03 | ASTM D-664 |
Color | 2 | 2.5 | ASTM D-1500 |
Density | 0.880 | 0.882 | ASTM D-1298 |
Base Oil SN150
Description of Base Oil SN150

Base oil SN150 is known as a light grade base oil at the lower end of the specifications for Grade I light base oils. It is mostly used in lubricant and lubricant additives production. It is a Group I base oil which has undergone solvent refining processes. To finish the refining, it was hydrogen treated to clear out any impurities. These products have good solubility characteristics for additives in product formulations.
SN 150, is base oil categorized in group I is a common quality base oil which uses in different applications base oils SN150 are used to manufacture products including lubricating greases, motor oil, and metal processing fluids, and many other applications One of the most important ISSUE is the viscosity at various temperatures.
Whether or not a crude oil is suitable to be made into a base oil is determined by the concentration of base oil molecules as well as how easily these can be extracted. This oil has no impurities or compounds that can have an adverse effect on the quality of the oil.
The lubricant base oils under the SN classification are GI base oils produced at our refineries. They are non-labelled products that are mainly used as the primary raw material in
formulating lubricating oils for industry in general. They are paraffinic, with low polycyclic aromatic content.
These base oils are obtained by direct distillation of highly paraffinic crude or by extraction with propane of the vacuum residue obtained with this type of crude These products, supported in suitable conditions of storage, in sealed containers and preserved from the water and other agents, does not suffer degradation.
Nevertheless, from the commercial point of view, we can indicate that the shelf life is four years from the date of manufacture
Application
The main field of application for these base oils is the formulation of lubricating oils for automobiles, industry, maritime use, greases and other special applications. The wide range of viscosity levels of the SN series means it can cover all the most common lubrication needs of these applications. These base oils can also be used for the production of white oils and as a fluidifier in asphalt production
Base Oils are used to manufacture products including motor oil, Industrial oil, Grease and etc.
- General-purpose oils
- Mould oil
- Transmission fluids
- Gear Oils
- Metalworking fluids
- Additives
- Hydraulic Oils
- Transformer Oils
Packing
Packed in new or used 210 kg drums, Iso tank, flexi Tanks, and IBC tank. Each 20-foot container takes 80 drums.
Specification of Base Oil SN150
SPECIFICATION | MIN | MAX | METHOD |
Viscosity @100˚C | 4.7 | 5.7 | ASTM D-445 |
Viscosity @40˚C | 19 | 24 | ASTM D-445 |
Viscosity Index | 90 | 110 | ASTM D-2270 |
Flash Point ˚C | 200 | – | ASTM D-92 |
Pour point | 0 | -6 | ASTM D-97 |
Total Acid Number mgKOH/g | 0 | 0.03 | ASTM D-664 |
Color | – | 1 | ASTM D-1500 |