Bitumen Penetration Grade 40/50
Bitumen Penetration Grade 40/50 Description

Bitumen penetration grade 40/50 bitumen means the penetration value is in the range 40 to 50 at standard test conditions which commonly used as a Paving Grade. Bitumen is applicable for the production of hot mix asphalt for bases and pavements and for road construction. Penetration Grade Bitumen supplied by HJ Oil is produced through aeration on vacuum bottom (the raw material used for making bitumen left in vacuum distillation column in oil refineries) in bitumen production units. Its penetration grade ( the measure of bitumen hardness) is between 40 to 50. Bitumen is specified by the penetration and softening point test. Designing is by penetration range only. The penetration grade bitumen has a thermoplastic property which causes the material to soften at high temperatures and to harden at lower temperatures. This unique temperature-viscosity relationship is important when determining the performance parameters such as the adhesion, rheology, durability, and application temperatures of bitumen.
The Bitumen mode is dependent on temperature. The temperature-vs-stiffness relationship of bitumen is dependent on the type of crude oil and its refining method. Bitumen penetration grade 40/50 is semi-hard penetration grade bitumen used as a paving grade bitumen which is suitable for road construction and repair. It is also used for the production of asphalt pavements with the technical specification. This grade of bitumen is mainly used in the manufacturing of hot mix asphalt for bases and wearing courses. Bitumen 40/50 is one of the most used bitumen grades and it’s a basic material for all other bituminous products.
Bitumen Penetration Grade 40/50 Applications
Bitumen 40/50 is Suitable for road construction and for the asphalt pavements with superior properties. This type of bitumen used in the manufacture of hot mix asphalt for bases and wearing courses and the main usage of this product is used in the road in tropical regions. the bitumen is provided during the presses of oxidation of vacuum bottom in bitumen production units. Due to its high air blowing and penetration, it is used in tropical areas with the Warm weather. It is not softened at high temperatures and does not fail its qualities.
Guaranty and safety of bitumen 40/50
HJ Oil guaranty the quality of bitumen penetration grade 40/50 with the arrangement of the international inspector to check quality and quantity during the loading to the vessel and controlling the production by QC by batch test report before shipping. HJ Oil guarantees the quality to meet with ASTM.
Bitumen Penetration Grade 40/50 Specifications
Bitumen 40/50 | Test method | Unit | Specification |
Specific gravity @ 25°c | ASTM D70 | Kg/cm3 | 1.01/1.06 |
Penetration @ 25°c | ASTM D5 | mm/10 | 40/50 |
Softening point °c | ASTM D36 | °C | 52/60 |
Ductility @25 °c | ASTM D113 | cm | 100 min |
Loss on heating(wt) % | ASTM D6 | wt % | 0.2 max |
Drop in penetration after heating % | ASTM D5-D6 | % | 20 max |
Flash point °c | ASTM D92 | °C | 250 min |
Solubility is CS2(wt) % | ASTM D4 | wt % | 99.5 min |
Spot test | A.A.S.H.O.T102 | Negative |
Bitumen Mastic
Bitumen Mastic Definition

Bitumen Mastic is a type of asphalt composed of suitable graded mineral and asphaltic cement, also to take in proper proportion to consistent mass solid or semi-solid form. when it is heated it is in fluid form and then becomes solid.
Mastic asphalt (MA) is a dense mixture consisting of coarse aggregate, and/or sand, and /or limestone fine aggregate, and/or filler and bitumen, which may contain additives (for example polymers, waxes). The mixture is designed to be of low void content. The binder content is so adjusted that the voids are completely filled and that even a slight excess of binder may occur. Mastic asphalt is pour-able and able to be spread in its working temperature condition. It requires no compaction on site.
On the other hand asphalt mastic – abbreviation AM – is a term used in Europe to describe a mix of sand (that is, without aggregates > 2 mm), and/or limestone fine aggregate, and/or filler and bitumen that is used especially for waterproofing in a variety of applications.
The formulation of the mixture is chosen as a function of
– field of application
– mechanical load
– thermal load
– chemical load
– climatological influences.
Bitumen Mastic Applications
Bitumen Mastic is used for concrete and ordinary red brick masonry with cement plaster surface is the basic method for the construction of floors, foundation, tanks, etc. To protect the commercial and civil structure of plants and building from corrosive attack acid-resistant brick lining is mostly used, Bitumen Mastic has good resistance to weak, diluted acids, alkalis salts, etc, also used as open mastic flooring for heavy-duty flooring.
It is used in:
– Bridge decks
– Flooring (building)
– Flooring (industrial)
– Road construction
– Rooftop car parks
– Hydraulic constructions
– Flat roofing
– Tanking
Production Process
In the past, that means approximately until 1970, mastic asphalt was often manufactured in mobile cookers (usually at the worksite) that were filled with the various components. By slowly heating them, the components were brought to the right temperature, where the mix-ing device (then mostly a horizontally rotating mixer shaft) served to make sure that the mix was homogeneous for processing. Of course, in this way, no high production rates could be achieved.
Nowadays mastic asphalt is manufactured in (specially designed) stationary industrial plants. These are designed to proportion the materials, dry the mineral aggregates, and mix them in a heat-controlled environment. Application specifications control the temperatures at which material is produced. Typically, in the past, mastic asphalt production temperatures were in the range of 230 to 270 ºC. However in recent years considerable research and investments have been done (and are still ongoing) to lower these temperatures beneath 230 ºC – in some countries even below 200 °C.
Packing
Bitumen Mastic is available in 25 Kg Carton Box & 20 Kg new steel drum.
Anionic Bitumen Emulsion
Anionic Bitumen Emulsion Description
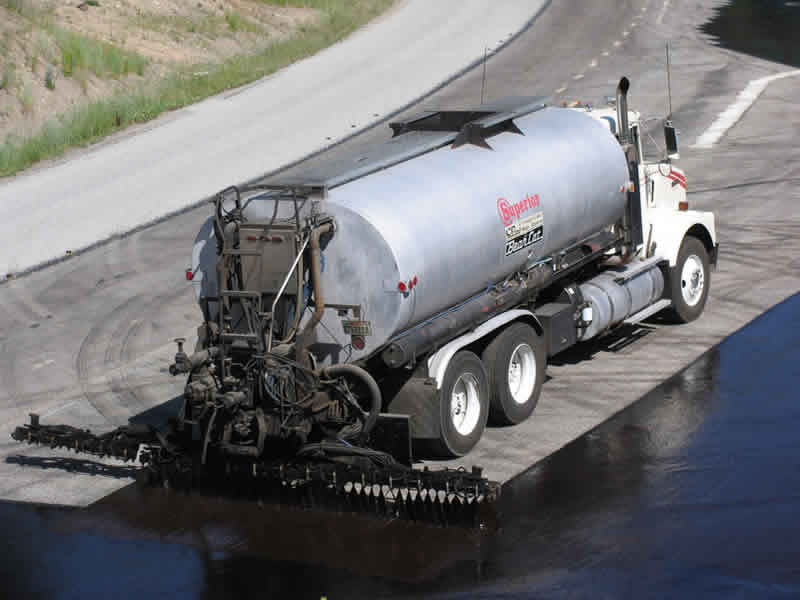
HJ Oil Group is a supplier of high-quality Anionic Bitumen Emulsion.
The preparation of bitumen emulsion is essentially the grinding of bitumen in water with a surfactant. Therefore, the emulsifier is one of the most important components of bitumen emulsions, which directly influences the quality and characteristics of the product. The emulsifier is a surfactant. By chemical nature, surfactants are divided into several types, depending on the charge of its particles. Since water bitumen emulsions are used intensively as binding and film-forming material in construction, two types of emulsifiers are used: anionic and cationic.
Chemical surface-active agents, which serve as emulsifiers, are classified by the electrochemical charge that is attained when they dissociate in a water solution. In the case of anionic emulsions, the chemical charge is negative. The chemical type and quantity of surface-active agent used in the manufacturing process govern the process in which the resulting asphalt emulsion can be used.
The term Anionic Bitumen Emulsion is derived from the migration of particles of bitumen under an electric field. The droplets migrate toward the anode (positive electrode), and hence the emulsion is called anionic. In an anionic emulsion, there are “billions and billions” of bitumen droplets with the emulsifying agent at the water bitumen interface. The tail portion of the emulsifying agent aligns itself in the bitumen while the positive portion of the head floats around in the water leaving the rest of the head negatively charged and at the surface of the droplet. This imparts a negative charge to all the droplets. Since negatives repel each other, all the droplets repel each other and remain as distinct bitumen drops in suspension. A typical anionic emulsifying agent is shown below along with a diagram showing the orientation of the agent at the bitumen-water interface and the negative charge imparted to each drop.
ANIONIC EMULSION
RS | MS | SS |
RS-1 RS-2 | MS-1 MS-2 MS-2h HFMS-1 HFMS-2 HFMS-2h HFMS-2s | SS-1 SS-1h |
The difference is that the anionic bitumen emulsion is negatively charged, while the cationic emulsions are positively charged. The choice of emulsifier used in the preparation of the emulsions determines the efficiency and reliability of the product.
For certain reasons, cationic systems have a significant advantage over anionic emulsions. Most of the fillers used in road construction have a limited amount of positively charged particles, which can attract the negatively charged particles of the anionic emulsion. Therefore, it is more difficult to create a uniform structure and ensure a high degree of adhesion with an anionic surfactant. When using anionic emulsion, bitumen should be modified by additives, while in the cationic emulsion, the emulsifier itself serves as an adhesion additive.
Unlike cationic emulsions, which readily interact with alkaline and acidic minerals, anionic emulsions are less versatile and work well only with alkaline minerals.
The amount of emulsifier applied influences emulsion breakdown rate, i.e. the time until the bitumen precipitating from the emulsion, returns to its original state.
Cutback Bitumen RC-3000
Cutback Bitumen RC-3000 Description

Our Cutback Bitumen RC-3000 complies with cutback petroleum asphalts of the rapid-curing type for use in the construction and treatment of pavements as per ASTM D2028-97 reapproved in 2004. Cutback Grade Bitumen is normally used in spraying and in some mixing applications. Cutback Bitumen is penetration grade bitumen blended with a solvent such as kerosene, white spirit, gasoline, and naphtha, controlling the curing time. Cut back petroleum asphalts of the rapid curing type supplied by us is petroleum grade bitumen manufactured from the fractional / vacuum distillation HJ Oil Group of crude oil blended with a solvent. Bitumen supplied by us is produced from the vacuum residue (short residue) feedstock. Penetration Grade bitumens are specified by the penetration and softening point test. The designation is by penetration range only. The penetration grade bitumens have a thermoplastic property which causes the material to soften at high temperatures and to harden at lower temperatures. This unique temperature/ viscosity relationship is important when determining the performance parameters such as the adhesion, rheology, durability, and application temperatures of bitumen. The cutback bitumen (Asphalts) supplied by us are blended from petroleum grade bitumen as stated herein.
Cutback asphalt is an asphalt cement that has a solvent or distillate such as gasoline, diesel fuel, kerosene, or naphtha added to make the asphalt liquid at ambient temperatures and improve its ability to coat aggregates. Two letters followed by a numerical digit designate or name a cutback asphalt.
Cutback asphalt can contain between 12 and 40 percent distillate. The high demand for the distillates to be used in energy applications and ever-increasing air quality regulations have caused a steady decline in the use of cutback asphalt.
When gasoline or naphtha is used to flux asphalt cement, the final product is called “rapid curing” (RC) cutback asphalt. Specifications permit up to 45 percent distillate in manufacturing an RC-3000 cutback asphalt.
Cutback Asphalt RC-3000 Applications
Current common uses are in penetrating prime coats and in producing patching or stockpile mixtures. Cutback asphalt used in mixing with aggregate will usually contain an adhesion agent to assist in the coating of the aggregate surface.
Cutback agents are used to lowering the viscosity of bitumen when it is applied as a primer to the surface of a road pavement aggregate base course or substrate. Kerosene is used as a bitumen cutback agent at different concentrations according to local conditions and requirements.
The cutback bitumen is ideal for prime coat and cold applied because of easy uses and no need for thinning and heating.
Cutback bitumen RC-3000 consist of initial incorporation of asphalt into the surface of non-asphalt based course preparatory to any superimposed treatment of construction.
The cutback asphalt RC-3000 applying to waterproof of surfaces, plug capillary voids, coat, and bond loose mineral particles.
Packing of Cutback Bitumen RC3000
Packing of cutback bitumen RC-3000 is in the new thick steel drum on the pallet to prevent any leak inside of container also bulk in bitutainer and tanker.
Safety of Cutback Asphalt RC-3000
Refer to Safety Datasheets before use.
Transport, use, and store at the lowest temperature possible.
Eliminate all potential ignition sources during application.
Avoid breathing vapors. Avoid contact with skin.
Always wear appropriate PPE including heat protection when used hot.
DO NOT allow product or washings to enter stormwater or sewer systems.
Specification of Cutback Asphalt RC 3000
we guarantee that the Rapid curing CutBack Grade RC-3000 it supplies under its offers is produced in compliance to and is in conformity to ASTM D-2028-97 Rev 2004 and is compliant to the following specification requirements.
Properties | Specification limit | Specification limit | Test method |
Min | Max | ||
Kinematic viscosity at 60°c ,cST | 3000 | 6000 | ASTM D2170 |
Flashpoint(tag open cup), °c | — | 27 | ASTM D3143 |
Distillation test Distillate, volume percent of total Distillate to 680°F(360°F) | |||
to 437°f(225°c) | — | — | ASTM D402 |
To 500°f(260°c) | 25 | — | |
to 600°f(316°c) | 70 | — | |
Residue from distillation to 680°f(360°c), percent volume by the difference | 80 | — | |
Test on Residue from distillation test | |||
Penetration 77°f(25°c) 100g,5s mm | 80 | 120 | ASTM D5 |
Ductility 77°f(25°c) 5cm/min cm | 100 | — | ASTM D113 |
Solubility in trichloroethylene % | 99 | — | ASTM D2042 |
Water, percent volume | — | 0.2 | ASTM D95 |
Cutback Bitumen RC-800
Cutback Bitumen RC-800 Description
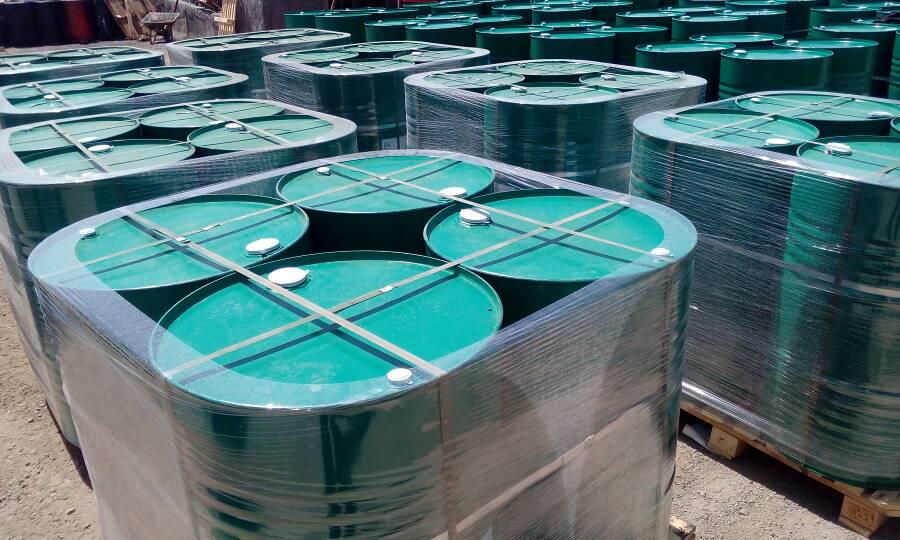
Cutback Bitumen RC-800 is Rapid curing (RC) cut-back asphalt consisting of penetration grade asphalt cement and diluent or cutter of rapid volatility.
Our Cutback Bitumen RC-800 complies with cutback petroleum asphalts of the rapid-curing type for use in the construction and treatment of pavements.
Cutback bitumen RC800 is dissolved of bitumen in solvents of Naphtha. Petroleum solvents such as naphtha, kerosene, etc. are cutback agents which can reduce the viscosity of the bitumen. As well as improving the ability to coat aggregates.
Cutback Bitumen RC-800 is a rapid curing cutback bitumen that contains 75% bitumen, is black in color, and is manufactured strictly as per ASTM D 2028M standard. The diluent temporarily reduces the viscosity of the asphalt cement for ease of handling and application. After application, the diluent evaporates, leaving asphalt cement to perform its function. RC–800 bitumen viscosity is between 800-1600 CST.
Cutback Bitumen RC-800 is dissolved of bitumen in solvents of gasoline. In many countries, kerosene and other volatile petroleum-derived products are added as a cutter or cutback agent to bitumen to reduce (or cutback) the viscosity of the bitumen. The mixture obtained may be called cutback bitumen.
gasoline or naphtha is used as the solvent in order to manufacture rapid curing bitumen cutback. RC-800 is one of the examples of a rapid curing cutback bitumen. The typical amount of solvent or distillate in a cutback bitumen is from 12% to 40%. Naphtha is used as a bitumen cutback agent at different concentrations according to local conditions and requirements.
The reduction in viscosity of the bitumen aids the construction of seal coats in road pavements as the softened mixture wets the chips more easily. The cutback agent evaporates from the seal coat, the cutback agent becoming a negligible component of the seal coat a few months after application. If significant amounts of the cutback agent remain in the seal coat an unwanted long term softening effect may result. Also, Cutback asphalt is an asphalt cement that has a solvent or distillate such as gasoline, diesel fuel, kerosene, or naphtha added to make the asphalt liquid at ambient temperatures and improve its ability to coat aggregates.
Cut back bitumen are easy to use because it is cold applied. Cut back grade bitumen is normally used in spraying. The main applications of RC-800 are in road pavement, tack coat, and prime coat.
CutBack Bitumen RC-800 Applications
Cutback agents are used to lowering the viscosity of bitumen when it is applied as a primer to the surface of a road pavement aggregate base course or substrate. Kerosene is used as a bitumen cutback agent at different concentrations according to local conditions and requirements.
The cutback bitumen is ideal for prime coat and cold applied because of easy uses and no need for thinning and heating.
Cutback bitumen RC-800 consists of initial incorporation of asphalt into the surface of non-asphalt based course preparatory to any superimposed treatment of construction.
The cutback asphalt RC800 applying to waterproof of surfaces plug capillary voids, coat, and bond loose mineral particles.
Also, It uses in Priming of all non-bituminous road buses, provision of temporary surfaces(deviations).
This kind of bitumen is suitable to be used in the construction and treatment of pavements as per ASTM D2028-97 reapproved in 2004. Cutback Grade Bitumen is normally used in spraying and in some mixing applications. Current common uses are in penetrating prime coats and in producing patching or stockpile mixtures. Cutback asphalt used in mixing with aggregate will usually contain an adhesion agent to assist in the coating of the aggregate surface. RC800 is used for pavement base and surfaces with dense-graded aggregate also for patching.
Guaranty and Safety of Bitumen RC-800
we guaranty the quality of cutback Asphalt RC800 with the arrangement of the international inspector. By checking the quality and quantity of the bitumen on each shipment during the loading to the vessel. Also controlling the production by the QC team via batch test report before shipping.
Here are the properties of Bitumen cutback RC800 which is classified by ASTM/EN15322:2009.
Bitumen RC800 Packing
Packing of cutback bitumen RC800 is in a new thick steel drum on the pallet to prevent any leak inside of the container, IBC Tank, and also bulk in bitutainer.
Specification of Cutback Asphalt RC800
property | Specification Limit | Specification Limit | Test method |
Min | Max | ||
Kinematic viscosity at 60°c, mm2/s | 800 | 1600 | ASTM D2170 |
Flashpoint(tag open cup), °c | +27 | — | ASTM D3143 |
Distillation test Distillate, volume percent of total Distillate to 680°f(360°c) | |||
to 437°f(225°c) | 15 | — | ASTM D402 |
To 500°f(260°c) | 45 | — | |
to 600°f(316°c) | 75 | — | |
Residue from distillation to 680°f(360°c), percent volume by difference | 75 | — | |
Test on Residue from distillation test | |||
Penetration 77°f(25°c) 100g,5s mm | 80 | 120 | ASTM D5 |
Ductility 77°f(25°c) 5cm/min cm | 100 | — | ASTM D113 |
Solubility in trichloroethylene % | 99 | — | ASTM D2042 |
Water, percent volume | — | 0.2 | ASTM D95 |
Cutback Bitumen RC-250
Cutback Bitumen RC-250 Description

Cutback Bitumen RC-250 complies with cutback petroleum asphalts of the rapid-curing type for use in the construction and treatment of pavements as per ASTM D2028-97 reapproved in 2004. Cutback Grade Bitumen is normally used in spraying and in some mixing applications. Cutback Bitumen is penetration grade bitumen blended with a solvent such as kerosene, white spirit, gasoline, and naphtha, controlling the curing time. Cut back petroleum asphalts of the rapid curing type supplied by are petroleum grade bitumen manufactured from the fractional / vacuum distillation of crude oil blended with a solvent. Bitumen supplied by HJ Oil is produced from the vacuum residue (short residue) feedstock. Penetration Grade bitumens are specified by the penetration and softening point test. The designation is by penetration range only. The penetration grade bitumens have a thermoplastic property which causes the material to soften at high temperatures and to harden at lower temperatures. This unique temperature/ viscosity relationship is important when determining the performance parameters such as the adhesion, rheology, durability, and application temperatures of bitumen. The cutback bitumen (Asphalts) supplied by us are blended from petroleum grade bitumen as stated herein.
Cutback asphalt is an asphalt cement that has a solvent or distillate such as gasoline, diesel fuel, kerosene, or naphtha added to make the asphalt liquid at ambient temperatures and improve its ability to coat aggregates. Two letters followed by a numerical digit designate or name a cutback asphalt.
Cutback asphalt can contain between 12 and 40 percent distillate. The high demand for the distillates to be used in energy applications and ever-increasing air quality regulations have caused a steady decline in the use of cutback asphalt.
When gasoline or naphtha is used to flux asphalt cement, the final product is called “rapid curing” (RC) cutback asphalt. Specifications permit up to 45 percent distillate in manufacturing an RC-250 cutback asphalt.
Cutback Bitumen RC-250 Applications
Current common uses are in penetrating prime coats and in producing patching or stockpile mixtures. Cutback asphalt used in mixing with aggregate will usually contain an adhesion agent to assist in the coating of the aggregate surface.
Cutback Asphalt RC-250 Packing
This cutback bitumen bulk in the tanker and also in new steel and thick drum on the pallet to prevent all leak inside of the container.
Safety of cutback bitumen RC-250
Refer to Safety Datasheets before use.
Transport, use, and store at the lowest temperature possible.
Eliminate all potential ignition sources during application.
Avoid breathing vapors. Avoid contact with skin.
Always wear appropriate PPE including heat protection when used hot.
DO NOT allow product or washings to enter stormwater or sewer systems.
RC-250 Specifications
HJ Oil Group guarantees that the Rapid curing CutBack Grade RC-250 it supplies under its offers is produced in compliance to and is in conformity to ASTM D-2028–97 Rev 2004 and is compliant to the following specification requirements.
property | specification limit | specification limit | Test method |
Min | Max | ||
Kinematic viscosity at 60°c ,cST | 250 | 500 | ASTM D2170 |
Flashpoint(tag open cup), °c | — | 27 | ASTM D3143 |
Distillation test Distillate, volume percent of total Distillate to 680°f (360°c) | |||
to 437°f(225°c) | 35 | — | ASTM D402 |
To 500°f(260°c) | 60 | — | |
to 600°f(316°c) | 80 | — | |
Residue from distillation to 680°f(360°c), percent volume by the difference | 65 | — | |
Test on Residue from distillation test | |||
Penetration 77°f(25°c) 100g,5s mm | 80 | 120 | ASTM D5 |
Ductility 77°f(25°c) 5cm/min cm | 100 | — | ASTM D113 |
Solubility in trichloroethylene % | 99 | — | ASTM D2042 |
Water, percent volume | — | 0.2 | ASTM D95 |
Cutback Bitumen RC-70
Description of Cutback Bitumen RC-70
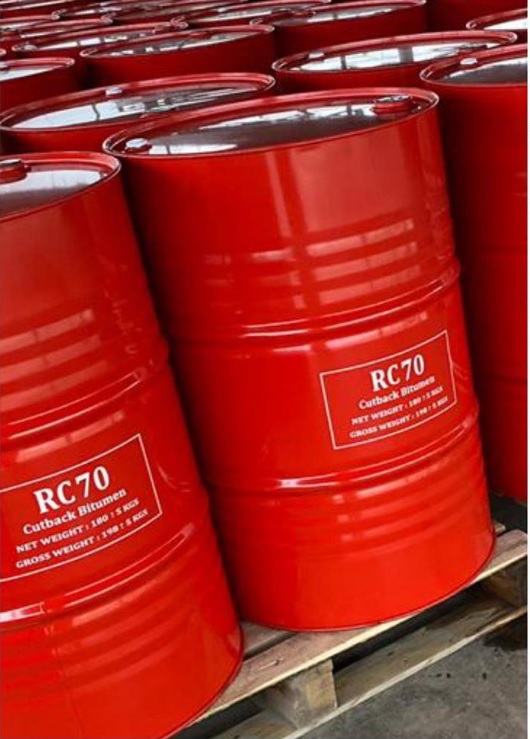
Cutback Bitumen RC-70 is Rapid curing (RC) cut-back asphalt consisting of penetration grade asphalt cement and diluent or cutter of rapid volatility.
Our Cutback Bitumen RC-70 complies with cutback petroleum asphalts of the rapid-curing type for use in the construction and treatment of pavements.
Cutback Bitumen RC-70 is a rapid curing cutback bitumen that contains 55% bitumen, is black in color, and is manufactured strictly as per ASTM D-2028M standard.
Cutback Bitumen RC-70 is dissolved of bitumen in solvents of gasoline. In many countries, kerosene and other volatile petroleum-derived products are added as a cutter or cutback agent to bitumen to reduce (or cutback) the viscosity of the bitumen. The mixture obtained may be called cutback bitumen.
The reduction in viscosity of the bitumen aids the construction of seal coats in road pavements as the softened mixture wets the chips more easily. The cutback agent evaporates from the seal coat, the cutback agent becoming a negligible component of the seal coat a few months after application. If significant amounts of the cutback agent remain in the seal coat an unwanted long term softening effect may result.
CutBack Bitumen RC-70 Uses
This kind of bitumen is suitable to be used in the construction and treatment of pavements as per ASTM D2028-97 reapproved in 2004. Cutback Grade Bitumen is normally used in spraying and in some mixing applications. Current common uses are in penetrating prime coats and in producing patching or stockpile mixtures. Cutback asphalt used in mixing with aggregate will usually contain an adhesion agent to assist in the coating of the aggregate surface.
Cutback agents are used to lowering the viscosity of bitumen when it is applied as a primer to the surface of a road pavement aggregate base course or substrate. Kerosene is used as a bitumen cutback agent at different concentrations according to local conditions and requirements.
The cutback bitumen is ideal for prime coat and cold applied because of easy uses and no need to thinning and heating.
Cutback bitumen RC-70 consists of initial incorporation of asphalt into the surface of non-asphalt based course preparatory to any superimposed treatment of construction.
The cutback asphalt RC-70 applying to waterproof of surfaces plug capillary voids, coat, and bond loose mineral particles.
This kind of bitumen is suitable to be used in the construction and treatment of pavements as per ASTM D2028-97 reapproved in 2004. Cutback Grade Bitumen is normally used in spraying and in some mixing applications.
Bitumen-Aggregate mixtures
Mixed-in-place (road mix):
- Pavement base and surfaces with sandy soi
Bitumen RC70 is ideal for surface treatment as:
- Prime coat on open surfaces
- Prime coat on tight surfaces
- Tack coat
- Dust binder
- Mulch treatment
Guaranty and Safety of Bitumen RC-70
We guaranty the quality of cutback Bitumen RC-70 with the arrangement of the international inspector. By checking the quality and quantity of the bitumen on each shipment during the loading to the vessel. Also controlling the production by QC team via batch test report before shipping.
Packing of Bitumen RC70
Packing of cutback bitumen RC-250 is in a new thick steel drum on the pallet to prevent any leak inside of the container, IBC Tank, and also bulk in vacutainer.
Specification of Cutback Asphalt RC70
property | Specification Limit | Test method | |
Min | Max | ||
Kinematic viscosity at 60°c , mm2/s | 250 | 500 | ASTM D2170 |
Flashpoint(tag open cup), °c | — | — | ASTM D3143 |
Distillation test Distillate, volume percent of total Distillate to 680°f(360°c) | |||
to 437°f(225°c) To 500°f(260°c) to 600°f(316°c) Residue from distillation to 680°f(360°c), percent volume by difference | 50 | — | ASTM D402 |
70 | — | ||
85 | — | ||
55 | — | ||
Test on Residue from distillation test | |||
Penetration 77°f(25°c) 100g,5s mm | 80 | 120 | ASTM D5 |
Ductility 77°f(25°c) 5cm/min cm | 100 | — | ASTM D113 |
Solubility in trichloroethylene % | 99 | — | ASTM D2042 |
Water, percent volume | — | 0.2 | ASTM D95 |
Cutback Bitumen RC-30
Cutback Bitumen RC-30 Description

Cutback bitumen RC-30 is an asphalt cement that has a solvent or distillate such as gasoline, diesel fuel, kerosene, or naphtha added to make the asphalt liquid at ambient temperatures and improve its ability to coat aggregates. Two letters followed by a numerical digit designate or name a cutback asphalt.
Cutback asphalt can contain between 12 and 40 percent distillate. The high demand for the distillates to be used in energy applications and ever-increasing air quality regulations have caused a steady decline in the use of cutback asphalt.
When gasoline or naphtha is used to flux asphalt cement, the final product is called “rapid curing” (RC)cutback asphalt. Specifications permit up to 45 percent distillate in manufacturing an RC-30 cutback asphalt.
Our Cutback Bitumen RC-30 complies with cutback petroleum asphalts of the rapid-curing type for use in the construction and treatment of pavements as per ASTM D2028-97 reapproved in 2004. Cutback Grade Bitumen is normally used in spraying and in some mixing applications. Cutback Bitumen is penetration grade bitumen blended with a solvent such as kerosene, white spirit, gasoline, and naphtha, controlling the curing time. Cut back petroleum asphalts of the rapid curing type supplied by us are petroleum grade bitumen manufactured from the fractional / vacuum distillation of crude oil blended with a solvent. Bitumen supplied by us is produced from the vacuum residue (short residue) feedstock. Penetration Grade bitumens are specified by the penetration and softening point test. Designation is by penetration range only. The penetration grade bitumens have a thermoplastic property which causes the material to soften at high temperatures and to harden at lower temperatures. This unique temperature/ viscosity relationship is important when determining the performance parameters such as the adhesion, rheology, durability, and application temperatures of bitumen. The cutback bitumen (Asphalts) supplied by HJ Oil Group are blended from petroleum grade bitumen as stated herein.
Cutback Bitumen RC-30 Applications
Current common uses are in penetrating prime coats and in producing patching or stockpile mixtures. Cutback asphalt used in mixing with aggregate will usually contain an adhesion agent to assist in the coating of the aggregate surface.
RC-30 Packing
This cutback bitumen bulk in the tanker and also in new steel and thick drum on the pallet to prevent all leak inside of the container.
RC-30 Safety
Refer to Safety Data sheets before use.
Transport, use and store at the lowest temperature possible.
Eliminate all potential ignition sources during application.
Avoid breathing vapors. Avoid contact with skin.
Always wear appropriate PPE including heat protection when used hot.
DO NOT allow product or washings to enter stormwater or sewer systems.
Cutback Bitumen RC-30 Characteristics
HJ Oil Group guarantees that the Rapid curing CutBack Grade RC-30 it supplies under its offers is produced in compliance to and is in conformity to ASTM D-2028-97 Rev 2004 and is compliant to the following specification requirements.
property | specification limit | Test method | |
Min | Max | ||
Kinematic viscosity at 60°c ,cST | 30 | 60 | ASTM D2170 |
Flashpoint(tag open cup), °c | — | — | ASTM D3143 |
Distillation test Distillate, volume percent of total Distillate to 680°f(360°c) | |||
to 437°f(225°c) To 500°f(260°c) to 600°f(316°c) Residue from distillation to 680°f(360°c), percent volume by difference | 55 75 90 50 | — | ASTM D402 |
Test on Residue from distillation test | |||
Penetration 77°f(25°c) 100g,5s mm | 80 | 120 | ASTM D5 |
Ductility 77°f(25°c) 5cm/min cm | 100 | — | ASTM D113 |
Solubility in trichloroethylene % | 99 | — | ASTM D2042 |
Water, percent volume | — | 0.2 | ASTM D95 |
Oxidized Bitumen
Oxidized Bitumen Description
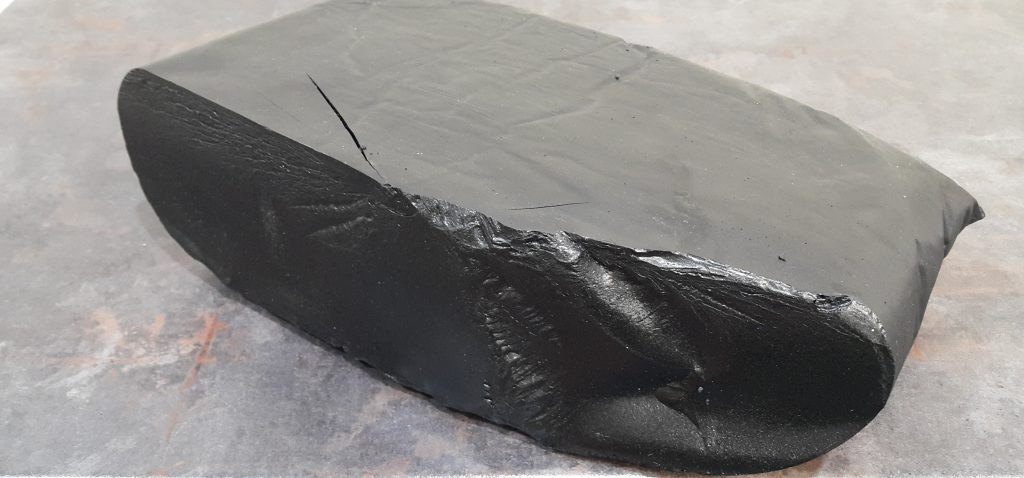
Blown bitumen grade or Oxidized Bitumen are produced by passing air through the penetration grades. This process gives the bitumen more rubbery properties than its original formula and they are simply harder bitumen. Hard bitumen under controlled temperature conditions is widely used as an anti-slip layer compound in the piling industry, for manufacture of roofing felts, the roofing and waterproofing industries, for sound dampening felts and under carriage sealant in the automotive industry, electric cable joint protection, joint filling compound, sealant compound and many others. Also used in sealing saw cuts and joints where expected movements are minimum. It is also used in the manufacturing of bituminous marine mastic for the oil & gas pipeline joints.
The most popular grades are; 95/25, 85/35, 90/40 and 115/15. We are also capable of producing other grades of Blown Bitumen upon request by our customers. Blown Bitumen high softening temperatures qualify them as excellent sealant for prevention from bleeding in high temperature applications. Blown Grade Bitumen shall be broken up into small pieces (for blown grade in molded cake form) and heated slowly to the application temperature of 220ºC to 230ºC. blown Bitumen is predominantly used in the piling industry as an anti slip compound for the manufacture of under carriage sealants in the automobile industry. It is also used as a sealant compound, as a joint filling compound apart from being used in the manufacture of roofing felts and sound dampening felts. Further, Blown Bitumen is used in the manufacture of bituminous marine mastic, which is required for the oil and gas pipeline joints. blown Bitumen is available in different grades like 95/25, 85/25, 75/25, 90/40 and 115/15. Tavoil is also capable of producing other grades of Oxidized Bitumen according to the specifications of individual clients.
Oxidized Bitumen Characteristics
Some of the major advantages of Oxidized Bitumen are that it is completely water resistant, highly flexible and durable. Further, it is chemically very stable. blown bitumen is a very flexible compound that is not only chemically stable but also a very durable compound apart from being completely water resistant. Lastly, Blown Bitumen has some very prominent technical advantages that makes it a very sought after compound in various applications.
Blown Bitumen Applications
Oxidized bitumens are used almost entirely for industrial applications, eg roofing, flooring mastics, pipe coatings, paints, etc, and are specified and designated by both softening point and penetration tests.
• Used As a bonding bitumen for roofing sheet membranes.
• Used As a hot-applied waterproofing layer.
• Used in Carpet tile manufacture.
• Used As a raw material for liquid bitumen coatings.
• Used in production of bituminous paint, mastic.
• Used in rust proof pipe coatings.
• Used as an anti-slip layer compound in the piling industry.
• Used in production of roofing and sound dampening felts.
• Used as under carriage sealant in the automobile industry, electric cable joint protection, joint filling compound, sealant compound and much more in our day to day life.
We are also capable of producing other grades of Blown Bitumen upon request by our customers. Oxidized Bitumen high softening temperatures qualify them as the excellent sealant for prevention from bleeding in high-temperature applications. Blown Grade Bitumen shall be broken up into small pieces (for the blown grade in molded cake form) and heated slowly to the application temperature of 220ºC to 230ºC. Oxidized Bitumen is predominantly used in the piling industry as an anti-slip compound for the manufacture of undercarriage sealants in the automobile industry. It is also used as a sealant compound, as a joint filling compound apart from being used in the manufacture of roofing felts and sound dampening felts. Further, Oxidized Bitumen is used in the manufacture of bituminous marine mastic, which is required for the oil and gas pipeline joints. This Oxidized Bitumen is available in different grades like 95/25, 85/25, 75/25, 90/40 and 115/15. Oxidized is also capable of producing other grades of Oxidized Bitumen according to the specifications of individual clients
Oxidized Bitumen Grades are suitable for sealing saw cuts and joints where there is expected to be the minimum amount of moving in the joint. Their wide temperature range prevents bleeding in high-temperature applications. Oxidized bitumen can also be used in industrial applications like roofing, flooring, mastics, pipe coatings, electrical applications to name a few.
Oxidised bitumen ” Oxidized Bitumen, Oxidized Asphalt ” range is used in the waterproofing industries, for carpet-backing, corrosion protection, acoustic panels and the manufacture of paints, amongst other applications.
Air-blowing: The manufacturing process used to make oxidized roofing asphalts in which air is blown through an asphalt flux. An exothermic oxidation reaction occurs, yielding an asphalt that is harder, more viscous, less volatile, and less temperature-susceptible than the asphalt flux used as the feedstock to the process.
Asphalt, oxidized (blown or air-refined) (CAS number 64742–93–4): Asphalt treated by blowing air through it at elevated temperatures to produce physical properties required for the industrial use of the final product. Oxidized asphalts are used in roofing operations, pipe coating, undersealing for Portland cement concrete pavements, hydraulic applications, membrane envelopes, some paving-grade mixes [AI 1990b], and the manufacture of paints [Speight 1992].
Blowing still: A closed-process vessel fitted at its base with a sparger and used in the air-blowing process to make many types of roofing asphalt.
Coating asphalt: An air-blown or oxidized asphalt used to manufacture roofing materials used in a variety of roofing systems such as asphalt shingles, polymer-modified bitumen roofing, reinforcing and underlayment felts, and roll roofing products.
Modified bitumen: A roofing system based on membranes manufactured by impregnating or coating one or more fabric plies with a straight-run or oxidized asphalt modified using a polymer, usually atactic polypropylene (APP) or styrene-butadiene-styrene (SBS). Modified bitumen systems may be torch-applied or installed by adhesion in hot asphalt or a cold-applied, solvent-based asphalt adhesive (cutback asphalt). Modified bitumen systems are used on low-slope (primarily commercial or industrial) roofs.
Bitumen
Bitumen Definition

Bitumen, also known as asphalt in the United States, is a substance that forms through the distillation of crude oil. It has waterproofing and adhesive properties. Bitumen production through distillation removes lighter crude oil components, such as gasoline and diesel, leaving the “heavier” Asphalt behind. The producer often refines it several times to improve its grade. Bitumen can also occur in nature: Deposits of naturally occurring bitumen form at the bottom of ancient lakes, where prehistoric organisms have since decayed and have been subjected to heat and pressure.
Bitumen is viscous, nonvolatile liquid or solid. Asphalt is a complex colloid system the chemical properties of which are dependent on the properties of crude oil from which it is produced. Pure bitumen is a colloid dispersion of microscopic asphalt particles (dispersion phase). The chemical composition of Asphalt is a mixture of various hydrocarbons with molecules of oxygen, sulfur, and nitrogen. Hydrocarbons present in bitumen are mostly condensed naphthene and aromatic rings with the small number of side paraffin chains. Mass fraction of hydrocarbons is 75-85%, hydrogen 9-10%, oxygen 2-8%, sulphur 5-7%, and nitrogen 0.1-0.5%. Bitumen is partially or completely soluble in various organic solvents. Dissolved fractions of Asphalt insolvent are called maltenes or petrolenes, and undissolved fractions are called asphaltenes. The maltenes are a mixture of resins and oil, and they are a dispersing agent. For the most part, the physical properties of bitumen depend on the dispersion degree of asphaltenes in maltenes.
Properties of Asphalt
– Adhesion: Bitumen has the ability to adhere to a solid surface in a fluid state depending on the nature of the surface. The presence of water on the surface will prevent adhesion.
– Resistance to Water: Bitumen is water-resistant. Under some conditions, water may be absorbed by minute quantities of inorganic salts in the bitumen or filler in it.
– Hardness: To measure the hardness of bitumen, the penetration test is conducted, which measures the depth of penetration in tenths of mm. of a weighted needle in bitumen after a given time, at a known temperature. Commonly a weight of 100 gm is applied for 5 sec at a temperature of 77 °F. The penetration is a measure of hardness. Typical results are 10 for hard coating asphalt, 15 to 40 for roofing asphalt and up to 100 or more for waterproofing bitumen.
– Viscosity and Flow: The viscous or flow properties of bitumen are of importance both at high temperature during processing and application and at low temperature to which bitumen is subjected during service. The flow properties of bitumen vary considerably with temperature and stress conditions. Deterioration, or loss of the desirable properties of bitumen, takes the form of hardening. Resultantly, a decrease in adhesive and flow properties and an increase in the softening point temperature and coefficient of thermal expansion.
– Softening point: Softening point is the temperature at which a steel ball falls a known distance through the bitumen when the test assembly is heated at a known rate. Usually, the test consist of a (3/8)in dia steel ball, weigh 3.5 gm, which is allowed to sink through a (5/8) in dia, (1/4) in the thick disk of bitumen in a brass ring. The whole assembly is heated at a rate of 9 °F per min. Typical values would be 240 °F for coating grade asphalts, 140 °F to 220 °F for roofing asphalt and down to 115 °F for bituminous waterproofing material.
– Ductility: The ductility test is conducted to determine the amount bitumen will stretch at a temperature below its softening point. A briquette having a cross-sectional area of 1 in2 is placed in a tester at 77 °F. Ductility values range from 0 to over 150 depending on the type of bitumen.
Bitumen Applications
The major bitumen produced in Middle East and the world known as Asphaltum is used in road construction. In road construction, It is used as a bonding agent for asphalt, and the use of it in the construction industry is ranked second as insulation. Estimates show that the annual amount of Egyptian bitumen in the world is about 102 million tons. Of this, about 85 percent of the Asphaltum is used in the road construction industry, and the 60/70 bitumen is most used. More than 10% of the bitumen produced in the world is used in the building industry and as insulation. And seagulls are used as sealing, insulating, pipe coating, etc.
- Surface coating
- Intruding Macadam
- Cold machine mixes
- Suspended seals
- Surface lining
- Lining reinforcement consolidation of soil-in-situ
- Dust Controlling
- Oil mulch
- Highways
- Airport runways
- Footways / Pedestrian Ways
- Car parks
- Racetracks
- Tennis courts
- Roofing
- Damp proofing
- Dams
- Reservoir and pool linings
- Soundproofing
- Pipe coatings
- Cable Coatings
- Paints
- Building Water Proofing
- Tile underlying waterproofing
- Newspaper Ink Production
- And many other applications
Pipe Coating
Coating systems advanced and at the same time modified polymers on the basis of economic the result is a wide research and long-lasting oil companies shell and Phoenix are Denmark. the characteristics of the coating causing severe epidemics can be high adhesion and resistant top of that soil degradation and stresses cathodic. Has your unique restorative properties. An article for corrosion protection of steel pipes buried in soil for a long period of time, with an appropriate yield. This coating due to being economical and safe for the environment continues to be an option in the transmission lines projects.
Bituseal Coating System
The Bituseal Coating system which was jointly developed by Phoenix International A/S and Shell International Petroleum Co.
bituseal is a PMB pipe coating system which combines the ease of hot applied coating processes with a high degree of corrosion protection and offers both reliability and affordability to clients. In terms of its technical properties, Bituseal matches and even outperforms 3-layer polyethylene coating.Bituseal has an excellent record in gas, water, and offshore pipelines.
Bituseal Coating Field Joint Membrane
Joints are the weakest link in any pipeline. The Bituseal Field Joint Membrane is specifically designed for fast, easy application on-site and to afford the same level of corrosion protection both in pipelines and joints. Bituseal Membrane is to cover pipeline joints or repairing damaged sections of coatings. It can be supplied either in the form of rolls or patches. It is a unique form of cover from both technical and economical viewpoints and a superb substitute for heat shrinkable sleeve. Apart from Bituseal system, it is also applicable on several other coatings like 3-layer polyethylene, bitumen enamel and coal tar with great consistency.
Roll Sheet
WaterProofing Bitumen Membrane Sheet (Here referred to as WPBS) are the best industrial outcome in the area of waterproofing ever attained by scientific and technological advancement. These products enable us to prevent the adverse effects of rain and snow water penetration into structures from their foundation up to roof. Employing different polymers and synthetic fibers, WPBS pass through well-equipped labs to be amended for attaining resistance against, high and low temperatures, tearing tension, and penetration of water
In addition to low weight and resistance against cold, heat, expansion and contraction, HJ OIL WPBS show high endurance being produced in two aluminum-covered and polyethylene film-covered versions. There two types of base products: single layered (nonwoven Spunbond polyester), and double layered (stringed fiber gloss tissue and 110 gr polyester) giving the product higher tensile strength against vibrations of the structure. WPBS is used in waterproofing of roofs, water canals, the foundation of tunnels, dams, pools, sloped surfaces, and the like.
Also, HJ OIL Bitumen membrane sheet reinforced by two layers of fiberglass and non-woven tissues with “needdle type” polyester. Azargum humidity polyester in spite of economic point of view possesses perfect utility qualities, therefore, resolves additional directional stability and ordinary surface replacements.
Types of Bitumen By Grade
There are different types of asphalt cement available with different properties, specifications and uses based on requirements of consuming industry.
Oxidized Grade
Blown bitumen grades or Oxidized Bitumen are produced by passing air through the penetration grades. This process gives the bitumen more rubbery properties than its original formula and they are simply harder bitumen. Hard asphalt under controlled temperature conditions is widely used as an anti-slip layer compound in the piling industry, for manufacture of roofing felts, the roofing and waterproofing industries, for sound dampening felts and under carriage sealant in the automotive industry, electric cable joint protection, joint filling compound, sealant compound and many others. Also used in sealing saw cuts and joints where expected movements are minimum. It is also used in the manufacturing of bituminous marine mastic for the oil & gas pipeline joints.
Penetration Grade
Graded Bitumen is classified by the depth to which a standard needle will penetrate under specified test conditions. This “pen” test classification is used to indicate the hardness of bitumen, lower penetration indicating a harder bitumen. Specifications for penetration graded bitumens normally state the penetration range for a grade, e.g. 50/70. Other tests are used to classify the bitumen for specification purposes, such as softening point, solubility, flash point etc.
Performance Grade
Performance Grade (PG) bitumen is Asphaltum which is graded based on its performance at different temperatures. The Long-Term Pavement Performance(LTPP) has given certain algorithm to calculate the temperature of the pavement based on the temperature of the air above. From this, the highest and the lowest temperatures of the pavement is calculated and the bitumen that performs well in that temperature range is selected.
Viscosity Grade
Viscosity Grade Bitumen (Asphalt) is a standard grade Asphaltum usually used as a Paving Grade Bitumen suitable for road construction and for the production of asphalt pavements with superior properties. This grade of Asphaltum is mainly used in the manufacture of hot mix asphalt for bases and wearing courses, and possesses characteristics and qualities unique sand quite different from other agents. They achieve very flexible and tenacious connections with other materials due mainly to viscoelastic response of Asphaltum, which behaviour depends on how fast charges are applied.
Polymer Modified
Polymer modified bitumen (PMB) is one of the specially designed and engineered Asphaltum grades that are used in making pavement, roads for heavy duty traffic and home roofing solutions to withstand extreme weather conditions. PMB is a normal bitumen with the added polymer, which gives it extra strength, high cohesiveness and resistance to fatigue, stripping and deformations, making it a favorable material for infrastructure.
Other Types of Bitumen
Cutback Bitumen
Cutback or Liquid Bitumen is asphaltum that is dissolved in a solvent. Typical solvents include Naphtha, gasoline and kerosene, white spirit etc. The type of solvent controls the curing time while the amount determines the viscosity of the Cutback Bitumen. Bitumen is ‘cutback’ by adding controlled amounts of petroleum distillates such as kerosene. This is done to reduce the viscosity of the asphaltum temporarily so it can penetrate pavements more effectively or to allow spraying at temperatures that are too cold for successful sprayed sealing with neat Asphaltum. The materials used to cutback bitumen will evaporate after application to leave the remaining material similar in hardness to the original asphaltum.
Blown Bitumen
It comes from hot air blown to pure asphaltum in the last stage of refining. In this process, hot air having 200-300 degree centigrade temperature is blown to bitumen container with porous tubes. In this process, hydrogen atoms in Asphaltum hydrocarbon are combined with oxygen in the air and by forming water, polymerization happens. Compared with pure Asphaltum, blown asphalt has a low penetration rate and a high softness point. This kind is used in making roof sheets, automobile battery, and coating.
Natural Bitumen
Natural bitumen or native asphalts are a class of Asphaltum which have been naturally produced due to climate conditions in the course of time, and are used without the need to be processed in distillation ways; they are very varied regarding their composition and properties.
Coating Bitumen
Bitumen coating compositions having substantially improved application and drying properties and producing coatings of improved properties including resistance to ultraviolet rays and alligatoring resulting therefrom said coating compositions comprising volatile solvent solutions of a bitumen coating material having softening point between 110 F To 250 F. The bitumen coating are also characteristically non-viscous materials which are not thixotropic and are therefore ordinarily applied as thin films. It’s compositions may also contain filler materials which tend to settle from the non-thixotropic compositions after storage for only a short time. It has been proposed in the past to add inert colloidal fillers such as silica to obtain thixotropic properties and thicker films on the application of the compositions. However, even such inert fillers tend to affect only solution properties and generally exist in the finished coating as an expensive additive which does not benefit other properties of the coating.
Bitumen Emulsion
This is a mixture of water & asphaltum. Hey wait, we know that asphaltum is a oil product and it cannot be mixed with water. That is why we add an emulsifier (a surface active agent) with water before adding asphaltum. Addition of emulsifier with water facilitates breaking of asphaltum into minute particles and keeps it dispersed in suspension.Therefore we can say that a bitumen emulsion is a liquid product consisting of three things, (i.e. water + Emulsion + Asphaltum) where droplets of asphaltum are suspended in water.