Medium Curing Cutback Bitumen
Medium Curing Cutback Bitumen Description
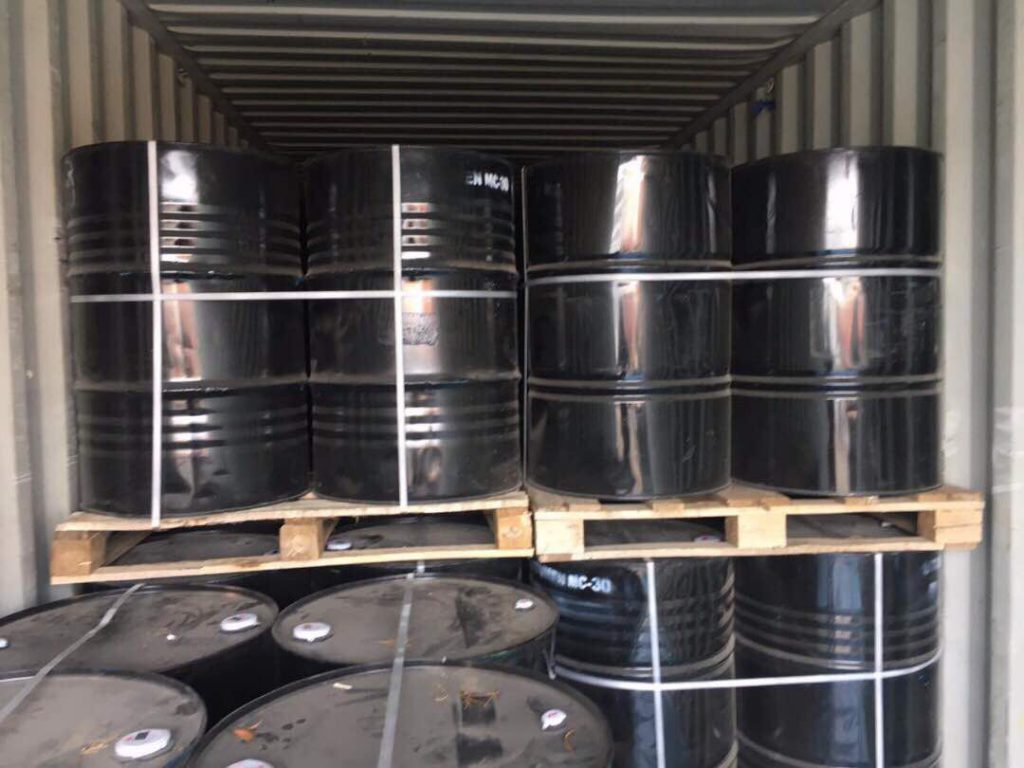
Medium Curing Cutback Bitumen is a compound of different oil solvents such as kerosene in order to transform bitumen to soluble bitumen which is evaporated in oil solvent using process and the bituminous layer is remained to make cohesion, penetration and form a sealing layer. A famous sort of it known as MC250 or liquid bitumen in asphalt section including pavement (cohesive between 2 Tack coat asphaltic layers), cold asphalt (Roadmix) and substructure (cohesive between asphaltic and soil layers-Prime coat) has been previously used. Available kerosene in MC250 would lead to promoting bitumen restoration, better penetration in infrastructure application (Primecoat) but yet will increase environmental hazards, price and heating cost in using and discharging time comparison with various types of water-based emulsions. Bitucut bitumen is produced and supplied in these types: MC800, MC250, MC70, MC30 and MC3000 which have the different percentage of solvent. Bitucut usage differs in various conditions such as substructure (continuous grading with low free space, open grading, and soil percentage). Using Bitucut in substructures (Primecoat) is the most demanded application.
Medium curing (MC) cutback asphalts are defined as those asphalt grades, which are prepared by using the medium volatile kerosene as the prime coat with boiling point ranges (MC-30, 70, 250, 800, 3000). The mix is done in a cold manner.
Cutback bitumen or asphalt is classified based on the curing as follows, 1) Slow, 2) medium and 3) rapid curing.
The degree of evaporation in the medium curing cutback asphalt is intermediate because the kerosene is intermediate volatile liquid as compared to the naphtha and diesel. The degree of liquidity depends on the proportion in which the kerosene is mixed in the asphalt cement.
The following specification for the medium curing cutback asphalt with its properties are as given below.
The medium curing cutback asphalt is used in the flexible pavements for surface dressing, prime coating, and tack coating. Evaporation of the solvents will be at a moderate rate. This grade is used with aggregates for ensuring better work-ability in the mix.
The degree of liquidity developed in each case depends principally on the proportion of solvent to asphalt cement. To a minor degree, the liquidity of the cutback may be affected by the hardness of the base asphalt from which the cutback is made. The degree of fluidity results in several grades of cutback asphalt—some quite fluid at ordinary temperatures and others somewhat more viscous. The more viscous grades may require a small amount of heating to make them fluid enough for construction operations.
The medium setting grades are designed for mixing with aggregates. Because these grades do not break immediately upon contact with aggregate, mixes using them can remain workable for extended periods of time and lend themselves to cold mix stockpiles.
Medium Curing Cutback Bitumen Applications
The medium setting grades are designed for mixing with aggregates. Because these grades do not break immediately upon contact with aggregate, mixes using them can remain workable for extended periods of time and lend themselves to cold mix stockpiles.
A cutback bitumen medium curing MC is simply a combination of asphalt cement and petroleum solvent. Like emulsions, cutbacks are used because they reduce asphalt viscosity for lower temperature uses (tack coats, fog seals, slurry seals, stabilization material).
Similar to emulsified asphalts, after a cutback asphalt is applied the petroleum solvent evaporates leaving behind asphalt cement residue on the surface to which it was applied. Cutback asphalt is said to “cure” as the petroleum solvent evaporates away. The use of cutback asphalts is decreasing because of environmental regulations.
MC Cutback Bitumen Packing
Packing of MC Cutback Bitumen is in new thick steel drums on pallet to prevent any leak inside of container also bulk in bitutainer and tanker.
Cutback Bitumen
Cutback Bitumen Description
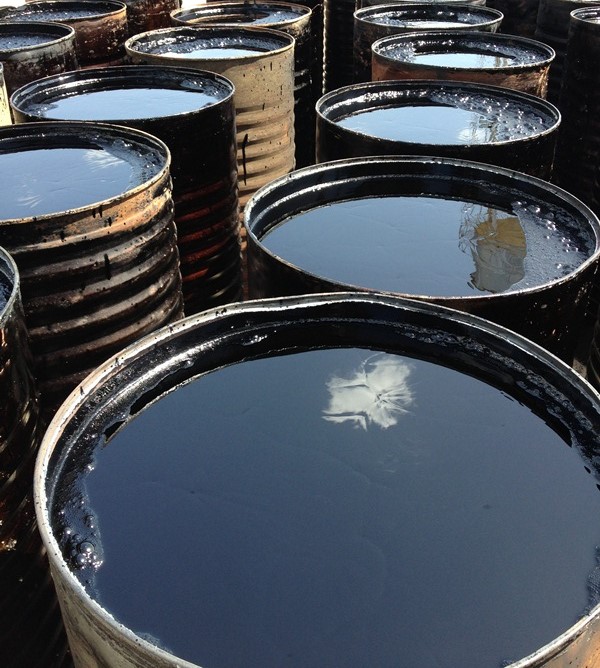
Cutback Bitumen ( Liquid Bitumen ) is Bitumen that is dissolved in a solvent. Typical solvents include Naphtha, gasoline and kerosene, white spirit etc. The type of solvent controls the curing time while the amount determines the viscosity of the Liquid Bitumen. Bitumen is ‘cutback’ by adding controlled amounts of petroleum distillates such as kerosene. This is done to reduce the viscosity of the bitumen temporarily so it can penetrate pavements more effectively or to allow spraying at temperatures that are too cold for successful sprayed sealing with neat bitumen. The materials used to cutback bitumen will evaporate after application to leave the remaining material similar in hardness to the original bitumen.
Cutback bitumen is a range of binders that are produced by blending (mixing) penetration grade bitumen and a hydrocarbon solvent, such as paraffin or mineral turpentine.
When the solvent has evaporated, the binder returns to its original penetration grade to tie the particles together. Cutback bitumen gets its name from the solvent that is involved in the process, because the solvent “cuts back” or evaporates, leaving behind the binder to “get on with the job”. The solvent used in cutback bitumen is called the “cutter” or “flux”.
Three types of solvents are used for the blending process: slow-curing, medium-curing or rapid-curing solvents. The latter two are the most common in South Africa. The choice of the solvent determines the rate at which the bitumen will cure when exposed to air. A rapid-curing (RC) solvent will evaporate faster than a medium-curing (MC) solvent. Curing relates to the evaporation rate of the solvent which influences the setting time of the bitumen. The viscosity of the cutback bitumen is determined by the proportion of solvent added: the higher the proportion of solvent, the lower the viscosity of the cutback.
Cutbacks differ from penetration grade bitumen in that they are more workable — in other words, they can be more easily reshaped. Less heat is required to liquefy cutback bitumen than penetration bitumen, making it easier to use at lower temperatures.
Typical cutback bitumens are MC 30 and RC 250. The letters in the name refer to the curing action of the solvent, and the number to the viscosity of the binder.
Cutback bitumen is classified based on viscosity grade. It is divided into three categories:
1- Rapid-Curing (RC) :The cutback bitumen is known as rapid-curing (RC) if the bitumen is solved in gasoline. The reason is that evaporation occurs quickly and the bitumen is deposited.
2- Medium-Curing (MC) :MC cutbacks are prepared by solving bitumen in kerosene which evaporates more slowly than gasoline.
3- Slow-Curing (SC) :Slow-curing cutback may be achieved from solving bitumen in gasoil or fuel oil or directly from distillation of crude oil.
Application of Cutback Bitumen
Cutback bitumens suitable for primer sealing can also be used in the manufacture of pre-mix asphalt, which is used in patch repairs. Cutback bitumens are used extensively in sprayed sealing applications, particularly in cooler weather where they provide improved initial stone retention due to their lower viscosity. Typically, a single application of the appropriate cutback bitumen is sprayed onto the primed pavement onto which aggregate is laid.
Prime and Tack Coating
The process of priming involves applying a low viscosity binder to a prepared but usually unbound aggregate base. It is intended to be absorbed by the top layers of the base and provide a surface more easily ‘wetted’ by a subsequent bituminous covering. The primer will be able to carry traffic for a short time (although this practice is uncommon) and help control dust. Generally, primers are applied at rates between 0.5 and 1.4 L/m2. Cutback bitumens suitable for priming are also used for tack coats, which are applied to an underlying surface to help with the adhesion of subsequent asphalt layer. A typical application rate is between 0.2 and 0.4 L/m2.
Prime Sealing
Where temperatures are too cool for an effective priming operation, or where traffic is likely to upset a primed surface before the final seal can be sprayed, a primer seal can be used to give adequate protection of the pavement for periods of up to 6 to 12 months. Cutback bitumens suitable for primer sealing can also be used in the manufacture of pre-mix asphalt, which is used in patch repairs.
Spray Sealing
Cutback bitumens are used extensively in sprayed sealing applications, particularly in cooler weather where they provide improved initial stone retention due to their lower viscosity. Typically, a single application of the appropriate cutback bitumen is sprayed onto the primed pavement onto which aggregate is laid.
HJ Oil GRUOP supplies and provides transfer of technology for production of all cutback Bitumens in correspondence to ASTM D2026, D2027, D2028, AASHTO M82-75 (2008), AASHTO M92-92 (2008). For any inquiries, please contact our sales team on info@www.hjoilgroup.com
- Slow Curing Cutbacks (ASTM D2026)
- Medium Curing Cutbacks (ASTM D2027 or AASHTO M82-75 2008)
- Rapid Curing Cutbacks (ASTM D2028 or AASHTO M81-92 2008)
USES OF CUTBACK & EMULSION BITUMEN IN DIFFERENT SYSTEMS OF ROAD MAINTENANCE
System | Description & Uses | Recomende Product |
SurfaceDressing | An application of binder on the road surface by a bitumen distributor followed by a covering of aggregates/chippings spread by a hopper gritter. Can be a single or double-layer surface dressing | Cutback: MC -3000 |
Prime Coating | An application of binder on a granular base to prepare for an asphalt surfacing .Normally a slow setting emulsion or cutback is used for better penetration purposes to seal off the road base. The rate of application can vary from 0.4-1.4 liter/m2 | Cutback : MC-30 MC -70 |
Tack Coating | A very light application of binder –hand or machine sprayed –to ensure bonding between the existing layer and the new overlay. The rate of application is normally between 0.25-0.7 liter/m2, depending on the surface being sprayed | Emulsion: K1-40 : RS-1K: RS-2K |
Semi– Grouting /Penetration Macadam | An application of hot binder on a compacted layer of coarse aggregate | Emulsion : RS-3K : MC-3000 Other : Bitumen |
Slurry Sealing | A maintenance technique where specially tailored emulsion, aggregates, water, and /or mineral filler is mixed in an on-site distributor and spread on an existing road surface at a thickness of 3-6 mm. It is both a preventive and corrective maintenance method for sealing of surface cracks, waterproofing asphalt surfaces and stopping oxidation | Emulsion: ALFA/SS |
Fog Sealing /Mist Spraying | It is similar to tack coating in that is a very light application of diluted emulsion for renewal/rejuvenation of old asphalt surfaces. The emulsion is usually diluted to a concentration of about 25-30% binder and applied at a rate of 0.3-0.8 liter/m2 | Emulsion : K1-40 : SS-1K : ALFA |
Dust Binding | A light application of 0.5-2.0 liter/m2 using diluted bitumen emulsion for dust control on unpaved roads | Emulsion: K1-40: SS-1K |