Polybutadiene Rubber (PBR)
Butadiene Rubber
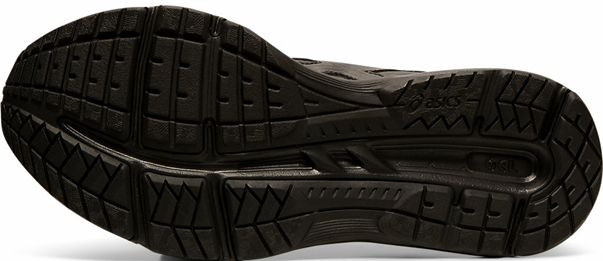
Polybutadiene rubber is rubber for general use. The most usage of butadiene rubber is tire sidewall, floor covering-bicycle tire, foot wear, rubber toy, cable and rubber pipes. They are produced by butadiene. It may be present in macromolecules in form of cis-1.4, trans-1.4 and 1.2 structural units. 1.2 units have pendant vinyl group; thus, they may create isomeric forms (syndiotactic, isotactic or atactic).
Content of individual forms of butadiene rubber structural units in polymeric chain depends on the polymerization method and type of used initiator and it determines basic properties of butadiene rubber.
Butadiene rubber-BR is a synthetic rubber. Polybutadiene rubber is a polymer formed from the polymerization of the monomer 1,3-butadiene. Polybutadiene has a high resistance to wear and is used especially in the manufacture of tires, which consumes about 70% of the production. Another 25% is used as an additive to improve the toughness (impact resistance) of plastics such as polystyrene and acrylonitrile butadiene styrene (ABS). Polybutadiene rubber accounted for about a quarter of total global consumption of synthetic rubbers in 2012.
Butadiene rubber, synthetic rubber widely employed in tire treads for trucks and automobiles. It consists of polybutadiene, an elastomer (elastic polymer) built up by chemically linking multiple molecules of butadiene to form giant molecules, or polymers. The polymer is noted for its high resistance to abrasion, low heat buildup, and resistance to cracking.
Description of Poly Butadiene Rubber (PBR)
Polybutadiene [butadiene rubber BR] is a synthetic rubber. PBR is a polymer formed from the polymerization of the monomer 1, 3-butadiene. Polybutadiene has a high resistance to wear and is used especially in the manufacture of tires, which consumes about 70% of the production. Another 25% is used as an additive to improve the toughness (impact resistance) of plastics such as polystyrene and acrylonitrile butadiene styrene (ABS). PBR accounted for about a quarter of total global consumption of synthetic rubbers in 2012. It is also used to manufacture golf balls, various elastic objects and to coat or encapsulate electronic assemblies, offering high electrical resistivity.
Application of Poly Butadiene Rubber
ATDM 1220 is appropriate for rubber compounds used in:
- the inner tube of hoses for sandblasting, along with natural rubber.
- cover of hoses, mainly pneumatic and water hoses.
- railway pads, bridge blocks, etc.
- manufacturing of the high-restitution toy Super Ball.
- fuel in combination with an oxidizer in various Solid Rocket Boosters such as Japan’s H-IIB launch vehicle.
- Tires
- Conveyor belts
- Crack pads
- Footwear soles
- V-belts
- Golf balls
Packing of Polybutadiene Rubber
35 ±0.5 KG bales wrapped with polyethylene film.
36 bales per crate (1260±18 KG).
Specification of Polybutadiene Rubber
Typical Properties | Units | Values | Test methods |
Compound Mooney Viscosity | MU | MAX 77 | ASTM D – 1646 |
Tensile Strength(35 Min) | Kgf/cm3 | MIN 150 | ASTM D412 |
Elongation at Break (35 Min) | % | MIN 440 | ASTM D412 |
300% Modulus at 145 °C | |||
25 Min | Kgf/cm3 | 68-108 | ASTM D412 |
35 Min | Kgf/cm3 | 74-114 | ASTM D412 |
50 Min | Kgf/cm3 | 74-114 | ASTM D412 |