Anionic Bitumen Emulsion
Anionic Bitumen Emulsion Description
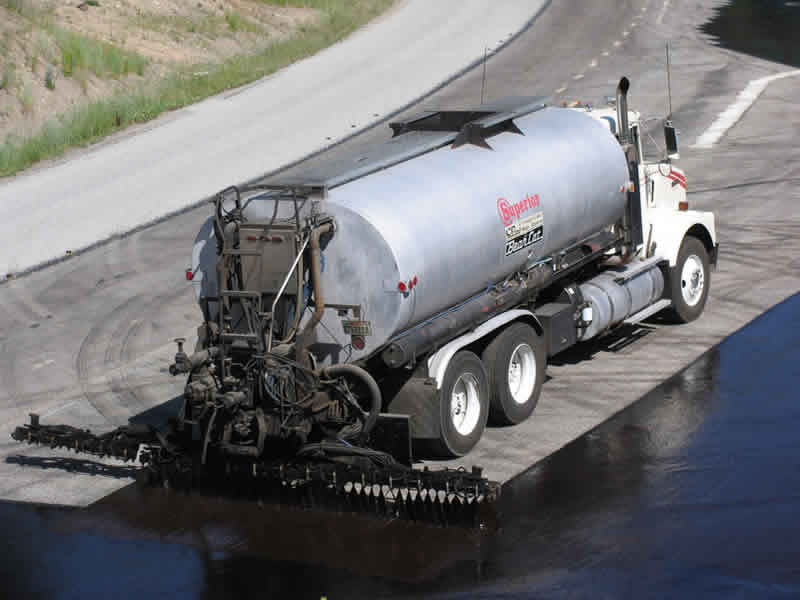
HJ Oil Group is a supplier of high-quality Anionic Bitumen Emulsion.
The preparation of bitumen emulsion is essentially the grinding of bitumen in water with a surfactant. Therefore, the emulsifier is one of the most important components of bitumen emulsions, which directly influences the quality and characteristics of the product. The emulsifier is a surfactant. By chemical nature, surfactants are divided into several types, depending on the charge of its particles. Since water bitumen emulsions are used intensively as binding and film-forming material in construction, two types of emulsifiers are used: anionic and cationic.
Chemical surface-active agents, which serve as emulsifiers, are classified by the electrochemical charge that is attained when they dissociate in a water solution. In the case of anionic emulsions, the chemical charge is negative. The chemical type and quantity of surface-active agent used in the manufacturing process govern the process in which the resulting asphalt emulsion can be used.
The term Anionic Bitumen Emulsion is derived from the migration of particles of bitumen under an electric field. The droplets migrate toward the anode (positive electrode), and hence the emulsion is called anionic. In an anionic emulsion, there are “billions and billions” of bitumen droplets with the emulsifying agent at the water bitumen interface. The tail portion of the emulsifying agent aligns itself in the bitumen while the positive portion of the head floats around in the water leaving the rest of the head negatively charged and at the surface of the droplet. This imparts a negative charge to all the droplets. Since negatives repel each other, all the droplets repel each other and remain as distinct bitumen drops in suspension. A typical anionic emulsifying agent is shown below along with a diagram showing the orientation of the agent at the bitumen-water interface and the negative charge imparted to each drop.
ANIONIC EMULSION
RS | MS | SS |
RS-1 RS-2 | MS-1 MS-2 MS-2h HFMS-1 HFMS-2 HFMS-2h HFMS-2s | SS-1 SS-1h |
The difference is that the anionic bitumen emulsion is negatively charged, while the cationic emulsions are positively charged. The choice of emulsifier used in the preparation of the emulsions determines the efficiency and reliability of the product.
For certain reasons, cationic systems have a significant advantage over anionic emulsions. Most of the fillers used in road construction have a limited amount of positively charged particles, which can attract the negatively charged particles of the anionic emulsion. Therefore, it is more difficult to create a uniform structure and ensure a high degree of adhesion with an anionic surfactant. When using anionic emulsion, bitumen should be modified by additives, while in the cationic emulsion, the emulsifier itself serves as an adhesion additive.
Unlike cationic emulsions, which readily interact with alkaline and acidic minerals, anionic emulsions are less versatile and work well only with alkaline minerals.
The amount of emulsifier applied influences emulsion breakdown rate, i.e. the time until the bitumen precipitating from the emulsion, returns to its original state.
Slow Curing Cutback Bitumen
Slow Curing Cutback Bitumen Description
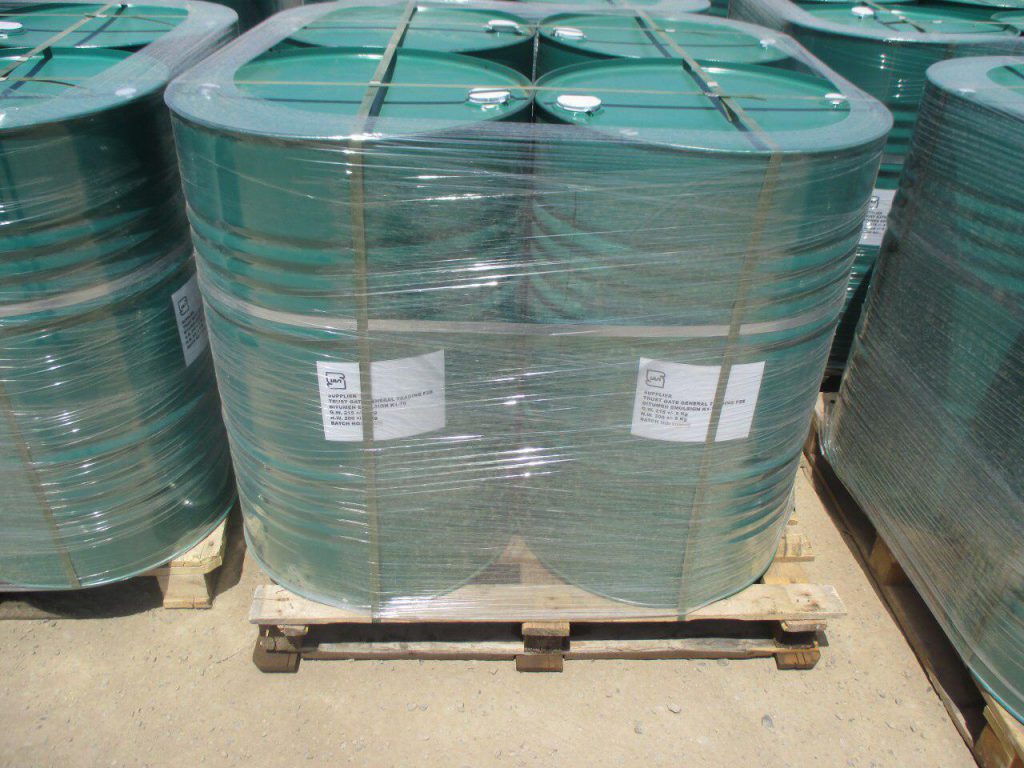
Slow curing Cutback Bitumen and oils of low volatility generally in the heavy distillate range (SC–70, 250, 800, 3000). The degree of liquidity developed in each case depends principally on the proportion of solvent to asphalt cement. To a minor degree, the liquidity of the cutback may be affected by the hardness of the base asphalt from which the cutback is made. The degree of fluidity results in several grades of cutback asphalt some quite fluid at ordinary temperatures and others somewhat more viscous. The more viscous grades may require a small amount of heating to make them fluid enough for construction operations.
Slow Curing often called “road oils,” are usually a residual material produced from the fractional distillation of certain crude petroleums. Traditionally any kind of aromatic, naphthenic and paraffinic oils are used. Slow Curing liquid bitumen materials can be prepared by blending bitumen with an oily petroleum fraction.
Slow Curing Cutback Bitumen Applications
Current common uses are in penetrating prime coats and in producing patching or stockpile mixtures. Cutback asphalt used in mixing with aggregate will usually contain an adhesion agent to assist in the coating of the aggregate surface.
Cutback agents are used to lowering the viscosity of bitumen when it is applied as a primer to the surface of a road pavement aggregate base course or substrate. Kerosene is used as a bitumen cutback agent at different concentrations according to local conditions and requirements.
The cutback bitumen is ideal for prime coat and cold applied because of easy uses and no need to thinning and heating.
Cutback bitumen SC consist of initial incorporation of asphalt into the surface of non-asphalt based course preparatory to any superimposed treatment of construction.
The cutback asphalt SC applying to waterproofing of surfaces, plug capillary voids, coat and bond loose mineral particles.
Slow curing (SC) cutback asphalt cement and oils of low volatility generally in the heavy distillate range (SC-70, 250, 800, 3000). The degree of liquidity developed in each case depends principally on the proportion of solvent to asphalt cement. To a minor degree, the liquidity of the cutback may be affected by the hardness of the base asphalt from which the cutback is made. The degree of fluidity results in several grades of cutback asphalt—some quite fluid at ordinary temperatures and others somewhat more viscous. The more viscous grades may require a small amount of heating to make them fluid enough for construction operations.
Slow curing (SC) cutback asphalt are often called road oils and are used primarily in road-mixing and dust-laying applications. This term originated in earlier days when asphalt residual oil was used to give roads a low-cost, all-weather surface. SC cutback asphalts are also used for stockpile patching mixes, plant-mixed with graded aggregates and occasionally for priming.
Medium Curing Cutback Bitumen
Medium Curing Cutback Bitumen Description
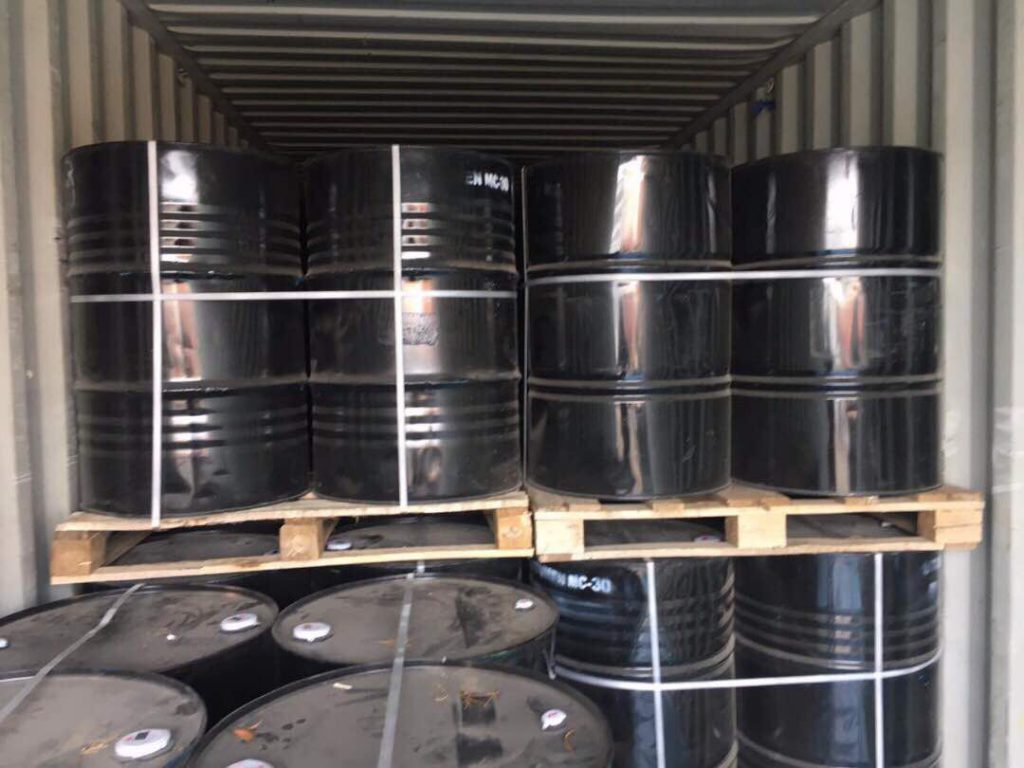
Medium Curing Cutback Bitumen is a compound of different oil solvents such as kerosene in order to transform bitumen to soluble bitumen which is evaporated in oil solvent using process and the bituminous layer is remained to make cohesion, penetration and form a sealing layer. A famous sort of it known as MC250 or liquid bitumen in asphalt section including pavement (cohesive between 2 Tack coat asphaltic layers), cold asphalt (Roadmix) and substructure (cohesive between asphaltic and soil layers-Prime coat) has been previously used. Available kerosene in MC250 would lead to promoting bitumen restoration, better penetration in infrastructure application (Primecoat) but yet will increase environmental hazards, price and heating cost in using and discharging time comparison with various types of water-based emulsions. Bitucut bitumen is produced and supplied in these types: MC800, MC250, MC70, MC30 and MC3000 which have the different percentage of solvent. Bitucut usage differs in various conditions such as substructure (continuous grading with low free space, open grading, and soil percentage). Using Bitucut in substructures (Primecoat) is the most demanded application.
Medium curing (MC) cutback asphalts are defined as those asphalt grades, which are prepared by using the medium volatile kerosene as the prime coat with boiling point ranges (MC-30, 70, 250, 800, 3000). The mix is done in a cold manner.
Cutback bitumen or asphalt is classified based on the curing as follows, 1) Slow, 2) medium and 3) rapid curing.
The degree of evaporation in the medium curing cutback asphalt is intermediate because the kerosene is intermediate volatile liquid as compared to the naphtha and diesel. The degree of liquidity depends on the proportion in which the kerosene is mixed in the asphalt cement.
The following specification for the medium curing cutback asphalt with its properties are as given below.
The medium curing cutback asphalt is used in the flexible pavements for surface dressing, prime coating, and tack coating. Evaporation of the solvents will be at a moderate rate. This grade is used with aggregates for ensuring better work-ability in the mix.
The degree of liquidity developed in each case depends principally on the proportion of solvent to asphalt cement. To a minor degree, the liquidity of the cutback may be affected by the hardness of the base asphalt from which the cutback is made. The degree of fluidity results in several grades of cutback asphalt—some quite fluid at ordinary temperatures and others somewhat more viscous. The more viscous grades may require a small amount of heating to make them fluid enough for construction operations.
The medium setting grades are designed for mixing with aggregates. Because these grades do not break immediately upon contact with aggregate, mixes using them can remain workable for extended periods of time and lend themselves to cold mix stockpiles.
Medium Curing Cutback Bitumen Applications
The medium setting grades are designed for mixing with aggregates. Because these grades do not break immediately upon contact with aggregate, mixes using them can remain workable for extended periods of time and lend themselves to cold mix stockpiles.
A cutback bitumen medium curing MC is simply a combination of asphalt cement and petroleum solvent. Like emulsions, cutbacks are used because they reduce asphalt viscosity for lower temperature uses (tack coats, fog seals, slurry seals, stabilization material).
Similar to emulsified asphalts, after a cutback asphalt is applied the petroleum solvent evaporates leaving behind asphalt cement residue on the surface to which it was applied. Cutback asphalt is said to “cure” as the petroleum solvent evaporates away. The use of cutback asphalts is decreasing because of environmental regulations.
MC Cutback Bitumen Packing
Packing of MC Cutback Bitumen is in new thick steel drums on pallet to prevent any leak inside of container also bulk in bitutainer and tanker.
Rapid Curing Cutback Bitumen
Rapid Curing Cutback Bitumen Description

Rapid curing cutback Bitumen cement is a combination of light diluents of high volatility, generally in the gasoline or naphtha boiling point range (RC-70, 250, 800, 3000), and asphalt cement.
Cut-back asphalts is defined as the bitumen whose viscosity value will be greatly reduced by the addition of volatile diluents (high viscosity). It mainly depends upon the diluents used. Generally, three types of cutbacks are used as follows, 1) rapid curing, 2) medium curing and 3) slow curing.
Rapid curing cutback asphalt combinations are prepared starting from the lighter diluents, and even from the fluid of higher viscosity. The grades used for rapid curing cutback bitumen are RC-70, RC-250, RC-800 and RC-3000. Here, the value given by numbers 70, 250, 800, and 3,000 represents the kinematic viscosity of the bitumen given in centistokes. The solvent concentration of rapid curing asphalt is 15-45% of the volume of asphalt cement used.
Different degrees of fluidity exists for each case and it depends on the proportion of the solvent of asphalt cement. In a minor degree cutback, liquidity may get affected by the hardness of base asphalt from which the cutback is made. It is used for the prime coats.
It is used in the pavement design process. It reacts quickly for the spray applications of bond and tack coats. It is helpful to seal the aggregate chips and sand seals. Rapid curing asphalts are mainly used for surface treatment.
Cut back asphalt RC 800 is useful for waterproofing surfaces and plug capillary voids. Grade RC250 acts as a seal coat in roadway pavements.
Mainly two tests are conducted on cut-back asphalt and are given as 1) residue and 2) cut back test. The testing of residue focusses on examination of penetration, ductility, and solubility. The testing of cutback bitumen includes the distillation, viscosity and flash point tests.
The degree of liquidity developed in each case depends principally on the proportion of solvent to asphalt cement. To a minor degree, the liquidity of the cutback may be affected by the hardness of the base asphalt from which the cutback is made. The degree of fluidity results in several grades of cutback asphalt—some quite fluid at ordinary temperatures and others somewhat more viscous. The more viscous grades may require a small amount of heating to make them fluid enough for construction operations.
Cutback Bitumen Rapid Curing Applications
Rapid Curing Cutback Bitumen is made by reducing the viscosity of and ordinary bitumen by adding mostly petroleum type solvent. Cutback Bitumen are used because their viscosity is lower than that of neat asphalt and can thus be used in low-temperature applications.
The rapid-setting grades are designed to react quickly primarily for spray applications, such as bond/tack coats, aggregate chips seals, sand seals and similar surface treatments.
Rapid curing Cutback bitumen are typically used as prime coats and tack coats. Generally, Cutback Bitumen are divided into three groups depending on their volatility of the solvent added
After a RC cutback is applied the solvent evaporates away and only the Bitumen is left. A rapid curing cutback bitumen is said to cure as the petroleum solvent evaporates.
RC Cutback Bitumen Packing
Bulk as IBC Tank, Flexi Tank
Reconditioned steel drums 220 lit., Net Weight: 191 ± 3 Kg
New steel drums 220 lit., Net Weight: 191 ± 3 Kg
RC Cutback Bitumen Safety
Refer to Safety Data sheets before use.
Transport, use and store at the lowest temperature possible.
Eliminate all potential ignition sources during application.
Avoid breathing vapors. Avoid contact with skin.
Always wear appropriate PPE including heat protection when used hot.
DO NOT allow product or washings to enter stormwater or sewer systems.